În țările occidentale, conceptul de Lean Manufacturing de management bazat pe principiile de bază ale bunului simț, este considerat unul dintre cele mai promițătoare modele de organizare.
Acum, în special în legătură cu intrarea România în OMC, punerea în aplicare a Lean Manufacturing devine popular în rândul producătorilor români, pe care viata le-a pus înainte de realizarea că producția de bunuri competitive nu este posibilă fără o restructurare globală a producției.
Reorganizarea mai necesară a procesului de producție în industria de panificație, în cazul în care în mod tradițional rentabilitatea scăzută în comparație cu alte sectoare ale complexului agro-industrial, dar, în același timp, există o mulțime de resurse pentru a îmbunătăți eficiența producției.
Dar, în acele zile, noi principii nu au fost acceptate de comunitatea de afaceri, pentru că atunci ei sunt mult înaintea timpului lor.
Părintele Lean Manufacturing a devenit Tayiti Ono din Japonia, care la mijlocul anilor 1950 a început să construiască un sistem special de organizare de producție numită Toyota Production System sau Toyota Production System (TPS).
Sistemul Toyota a câștigat popularitate în Occident în anii 1980. În sistemul de interpretare occidentală a devenit cunoscut sub numele de Lean Production, Lean Manufacturing, Lean. Termenul macră ( «slabă, slabă, cost-eficiente.“ - în limba engleză) a fost propus de John Krafcik, unul dintre consilierii americani.
contribuție semnificativă la dezvoltarea teoriei producției slabe au Shigeo Shingo, care a creat metoda SMED, și Masaaki Imai - primul distribuitor al filozofiei Kaizen.
În primul rând, conceptul de producție slabă (BP), utilizate în industriile cu fabricație discrete, în special în industria de automobile. Apoi, conceptul a fost adaptat la condițiile de producție continuă. Treptat, ideea de stânga Lean și dincolo de producție - conceptul a fost aplicat în comerț, servicii, utilități, asistență medicală, militară și sectorul public.
În multe țări, introducerea de sprijin de stat PD. În timpul perioadei de cea mai mare concurență și escaladarea crizei în afaceri peste tot în lume, nu există nici o altă cale decât utilizarea celor mai bune tehnologii de management din lume pentru a crea produse și servicii care îndeplinesc pe deplin de calitate și preț clienților.
Obiectivele și principiile Lean
În economia de astăzi supraviețui numai acele companii care sunt în măsură să fie eficiente, care este, puteți obține cele mai la costuri minime. Pentru a realiza acest lucru, puteți fie crește prețurile pentru produsele lor proprii sau de a reduce costurile.
Costurile, la rândul său, poate fi redusă fie prin utilizarea resurselor cu costuri mai reduse, ceea ce înseamnă adesea o calitate mai scăzută a produsului finit, fie prin optimizarea producției. Este sarcina de optimizare și este proiectat pentru a rezolva sistemul de Lin (dar și: Lean, Lean Manufacturing, TPS).
Principii de Lean Manufacturing este o metodă sistematică de a găsi soluții simple pentru a elimina pierderile ascunse în producția de bunuri și servicii rapid și eficient satisface nevoile clienților. Aceste principii simple ar trebui să fie puse în aplicare de către personalul din magazine și birouri, scopul lor - pentru a ajuta angajații să scape de problemele de zi cu zi de rutină.
. J. Womack și D. Jones a expus esența producție slabă sub forma a cinci principii:
1. Se determină valoarea unui anumit produs.
2. Identificarea fluxului de valoare pentru acest produs.
3. Pentru a asigura un flux flux continuu de valoarea produsului.
4. Lăsați produsul consumatorului tragere. Trăgând de producție (producție a „tras“ de către client, și nu impuse de către producător).
5. Straduiti pentru excelență. Kaidzen (Kaizen) - îmbunătățirea continuă a producției.
Introducerea Lean
Există trei faze principale de punere în aplicare a conceptului de fabricație slabă:
• cercetare de piață;
• Asigurarea continuității fluxurilor de valoare;
• netezirea fluxurilor.
Se recomandă să treacă cele trei faze, în aceeași ordine în care au loc punerea în aplicare a studiului. Numai în studiul aprofundat al cererii, fluxuri de valoare și metode de netezire, împreună cu recomandări pentru gestionarea fluxurilor de valori pot da nu numai fiabilitatea procesului de transformare, dar, de asemenea, pentru a asigura stabilitatea lor.
1. Faza de cercetare a consumatorilor. Este necesar, în primul rând, pentru a identifica cine este clientul rezultatelor unor lucrări, care sunt cerințele lor. Numai atunci va fi capabil de a satisface cererea consumatorilor pentru performanță. Pentru a identifica și de a satisface cererea consumatorilor pot fi folosite o varietate de instrumente și tehnici, cum ar fi calculele de timp tact tampon de calcul și de asigurare rezerve, utilizarea sistemului 5S, utilizarea tehnicilor de rezolvare a problemelor.
2. Faza valoare continuitate fluxului. În această etapă, luând măsurile necesare pentru a se asigura că rezultatele lucrărilor în primit toți clienții interni și externi, în timp util și în cantități corespunzătoare, de exemplu, sistemul „Kanban», aplicarea principiului FIFO ( «prima, primul ieșit»), realizarea unui echilibru în producția de furaje linii, munca de standardizare, planificare adecvată a siturilor industriale.
3. Faza de netezire. În cele din urmă, după cererea de consum a identificat pentru rezultatele muncii este ajustat și un proces continuu de punere în aplicare a acestora, se trece la netezirea acesteia, în scopul de a asigura distribuirea uniformă și eficientă a sarcinilor zilnice, săptămânale și lunare. În acest scop, următoarele mijloace de fluxuri de netezire: bord cerere pentru discuția de idei și propuneri (vizibile de bord pas), cutii de echilibrare a sarcinii (heydzunka), utilizarea logisticii.
Condiții pentru implementarea cu succes a principiilor Lean Manufacturing:
• Elaborarea unui plan de educație și formare a personalului care se ocupă de specificul întreprinderii. Toate organizațiile au diferite nevoi, bugete și resurse. Diferite grupuri de oameni sunt la diferite seturi de cunoștințe și abilități. planificarea activităților de formare ar trebui să țină cont de aceste diferențe și nivelul nevoilor oamenilor de cunoștințe specifice.
• Utilizați gama completă de instrumente și resurse pentru învățare. Unii dintre ei prefera cursuri de formare, altele - monitorizarea activității colegilor. Planul de formare trebuie să includă utilizarea unor metode și mijloace care sunt potrivite pentru majoritatea angajaților.
• Obținerea de informații și idei prin intermediul unor analize comparative. Instruirea oamenilor de producție slabă implică dezvoltarea abilităților lor creative. Este foarte important să fie în măsură să meargă dincolo de propriile afaceri și chiar industrii pentru a vedea cum putem face afaceri mai eficient și pentru a găsi modalități de aplicare a ideilor noi în ceea ce privește organizarea lor. De exemplu, în industria de panificație și de patiserie destul de o mulțime de metode utile de organizare, practicate în inginerie mecanică.
Tayiti Ono a identificat șapte tipuri de pierderi în cursul unei proceduri judiciare. Pierdere - toate operațiunile care necesită timp și resurse, dar nu cresc valoarea produsului sau serviciului finit. Scopul producție slabă - să identifice, să analizeze și să elimine toate pierderile din procesul de producție.
1. Mișcare excesivă - mersul pe jos excesivă, mișcare sau de manipulare (mișcare inutile datorită ergonomie scăzută, amplasarea incomodă de mașini, unelte, echipamente de birou, de transfer manual de documente, etc ...).
2. Transport excesivă - informații și materiale de mișcare care nu adaugă valoare (transportul de materiale între magazine situate la o distanță considerabilă unul față de celălalt, un aspect ineficientă a instalațiilor de producție, etc ...).
3. Tratamentul excesiv - inutil pentru proprietățile clienților care pot ascunde defectele (produse de fabricație cu opțiuni de utilizator neutilizate, design nerezonabil complexitate, ambalarea mărfurilor scumpe, etc ...).
4. Timpul de așteptare - simpli muncitori sau mașini în anticiparea sau precedente următoarele operațiuni, materiale sau informații (lipsa de materii prime, lipsa de informații, timpii morți din cauza defecțiuni, nefuncționare a lucrătorilor, etc ...).
5. Supra-producție - care produc mai mult decât a cerut de către client. Tipul cel mai periculos de pierdere, ca și cealaltă atrag după sine. Este norma în multe companii (de planificare o încărcare completă de echipamente și forței de muncă, care lucrează cu cantități mari, volumul de producție care depășește nivelul cererii). Pentru produsele care aparțin perisabile, un astfel de principiu de organizare poate duce la deteriorarea produselor și a reciclării inutile.
6. Excesul de rezerve - probleme de producție ascunde și de întreținere (achiziționarea de materii prime pentru viitor, costul de spațiu chirie depozit, salariile personalului depozit).
7. Defecte si reciclare - orice defect cauzat în timpul executării lucrărilor asociate cu necesitatea de a elimina (reprelucrare, defecte eliminând, documentele perepodpisanie datorate erorilor).
Dzheffri Layker a subliniat în cartea sa „The Tao Toyota» tip de pierdere a opta:
potențiale pierderi creative - îndeplinirea sarcinilor angajatului nu este necesar pentru punerea lor în aplicare de toate cunoștințele și abilitățile. idei inutilitate, angajat de propuneri care vizează îmbunătățirea societății (lucrători cu înaltă calificare care desfășoară munci necalificate, respingerea conducerii de schimbări utile, pierdere de timp, idei, abilități).
Motivele pentru introducerea de eșecuri Lean
Motivele pot fi evidențiate foarte mult, ele sunt, în principal legate de înțelegerea greșită a principiilor Lean Manufacturing. Aici sunt unele dintre cele mai importante probleme de acest gen.
În primul rând, una dintre cele mai mari greșeli este eșecul de a înțelege rolul de lider în implementarea Lean. Directori și șefi de departamente trebuie să înțeleagă planul noului sistem și să formuleze propunerile lor cu privire la modul în care acestea pot contribui la acest proces. Unii dintre acești lideri au devenit „dirijori“ ai noii inițiative și sprijină direct pe cei care implementează sistemul și de a face îmbunătățiri la niveluri mai scăzute.
În al doilea rând, unii oameni reduce din greșeală introducerea Lean la construcția sistemelor de producție ideale nu au flexibilitatea necesară. Sistemul de fabricație introdus trebuie să țină cont de specificul producției în România, precum și caracteristici specifice de fabricație, și să nu fie exact la fel ca și sistemul de producție „Toyota“ sau „Ford“.
Trebuie să fim pregătiți pentru a lucra cu un sistem care nu este perfect, dar este flexibil și poate fi ajustat în timp util sau modificate.
În al treilea rând, introducerea de Lean complicată de faptul că mulți oameni doresc să fie difuzate imediat - înainte de a fi învățat să meargă. Ca rezultat, sistemul de dezvoltare nu începe cu elementele de bază, dar cu tehnici complexe de organizare de multe ori în mod nejustificat laborioase pentru acele condiții în cazul în care acestea se vor utiliza.
În al patrulea rând, va începe reorganizarea locurilor de muncă, fără clarificare sistem de personal. Ca urmare a unor obiceiuri vechi, stocate într-un condiții noi, îmbunătățite, duce la dezastru.
În al cincilea rând, liderii de multe companii încearcă să pună în aplicare Lean fără asistență. Din păcate, acest lucru duce aproape întotdeauna la eșec sau poate cauza o problemă atunci când executați o mulțime de noul program. Adesea este un observator extern, cu o abordare deschisă a procesului se poate vedea de fapt, pierderile.
Lean de fabricație nu poate fi introdus, acesta poate fi utilizat - este un proces nesfârșit de îmbunătățire continuă. Deși nu exclude rezultate rapide. Gama de aplicații de succes - de la zero la parametrii de mai sus.
Lean ca un colac de salvare
Aspectele operaționale ale Lean Manufacturing va permite noi lideri să propună, la sfârșitul crizei și chiar și în timpul fundamental noile sale oferte, competitive pe preț, calitate și de livrare.
De obicei, rezultatul Lin-programe, fără investiții suplimentare:
• reducerea perioadei de ordinul a 5-10;
• Creșterea productivității muncii cu 50-200%;
• reducerea 10-30% a costurilor;
• reducerea defectelor cu 30-80%.
În investiții și aspectele financiare ale întreprinderii, nu vorbesc de această tehnică, uneori abandoneze programele de investiții sau de a le reduce în mod semnificativ. propria noastră experiență arată în mod clar că aplicarea principiilor Lean Manufacturing pentru a obține rezultatul dorit în procesul de investiții:
• semnificativ (cu 10-30%, iar în unele cazuri cu 100%), reducerea necesității de investiții pentru a obține aceleași „fâșii“, care a fost considerată de neconceput fără alimentare cu energie;
• redus cu 10-20% calendarul de proiecte de investiții începute.
Atunci când este utilizat în mod corespunzător, rezultatul sistemului Lean vine in cateva saptamani sau zile, iar beneficiile observate aproape imediat.
Pentru a evalua impactul economic al introducerii Lean, trebuie să începem cu contul de cantitatea de materie primă în activitatea în acest moment, care este, pentru a face un fel de „imagine Polaroid“, a stadiului actual al afacerilor în cadrul companiei. Apoi intreaba-te, și inginerii săi cum să reducă aceste fonduri. De multe ori, multe milioane de ruble sunt cheltuite pentru stocarea excesului de inventar al materialelor și intermediari prime, care afectează în mod negativ interesele societății.
În al doilea rând, necesitatea de a lua în considerare pe deplin unul dintre procesele de producție la nivelul întreprinderii și a calcula cât de mult timp (ore, zile sau săptămâni) ocupă loc procesul de la materia primă la plante pentru a obține un produs final de către client. Timpul de ciclu lung este, de asemenea, în valoare de bani pentru ca materii prime, nu primiți nici un comision atâta timp cât clientul nu primește de la tine produsul finit și nu veți plăti.
În al treilea rând, ar trebui să ceară manageri și ingineri pentru a determina cât de departe de alimentare a instalației va birui (material de martor), la secțiunea de procesare și de ieșire ca pe un produs finit la client. De obicei, această distanță pentru toată lumea surprinzător, și se poate reduce în mod semnificativ, fără a compromite producția. Mișcarea de materiale pe distanțe lungi și de suprasarcină frecvente - un proces foarte costisitor, consumă bani și muncă. Dacă aceste trei lucruri - preț, timp și distanță - studiat, managerii au deja trei bun punct de plecare pentru îmbunătățirea procesului de producție folosind instrumente Lean.
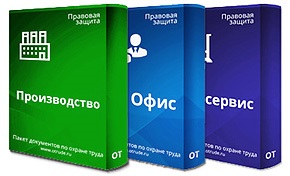
Muncii și Protecției Personalului
de la 3500 ruble
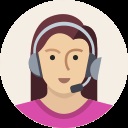