Cele mai multe surse de fabricație slabă identificat în mod eronat cu TPS (sistemul de producție Toyota - Toyota Production System), Kaizen (îmbunătățirea continuă), sau chiar și cu unul dintre instrumentele de 5S și se caracterizează printr-o organizare a întreprinderii, în care produsele sunt fabricate în strictă conformitate cu cerințele consumatorilor și mai puține defecte în comparație cu produsele fabricate în conformitate cu principiile de producție în masă, reducând în același timp costurile forței de muncă, spațiu, de capital și de timp. Cu toate acestea, bazat pe sistemul de producție Toyota, conceptul Lean include o varietate de alte metode pentru a crește eficiența producției.
producție Lean (din limba engleză Lean Manufacturing / Lean Production / Lean Enterprise.) - concept de management la nivel are drept scop eliminarea deșeurilor și optimizarea proceselor de afaceri din stadiul de dezvoltare a produsului, de producție, precum și de a interacționa cu furnizorii și clienții. Lean Management posibil sa axat pe identificarea nevoilor pieței și crearea de valoare maximă pentru client la cel mai mic resursa de cost: efort uman, echipamente, timp, zone de producție, etc. Lean fabricație este fundamentul unei noi filosofii de management al producției.
Cele mai populare instrumente și tehnici de fabricație macră sunt:
1) cartografierea fluxului de valoare (Value Stream Mapping);
2) scoate producția de masă;
4) Kaidzen - îmbunătățirea continuă;
5) 5S Sistem - tehnologia de creare a unui spațiu de lucru eficient;
6) Sistemul SMED (Single Minute Schimb de Dies) - echipamente de conversie rapidă;
7) Sistemul TPM (Total Productive Maintenance) - echipamente de îngrijire universal;
8) Sistemul JIT (Just-In-Time - JIT);
10) Dispunerea celulelor.
Luați în considerare procesul de introducere a conceptului de producție slabă pe un exemplu de producție de Tatspirtprom. Obiectele de studiu au fost alese producția de vodca „Tatarstan“ și „Lacul Albastru“.
Pentru introducerea elementelor de Lean Manufacturing echipa sarcină specială a fost stabilită la uzina, care a constat din specialiștii principali de producție. Echipa a analizat toate tipurile de pierderi care ar putea apărea în întreprindere. În continuare a fost identificat modalități de reducere a pierderilor, optimizarea costurilor și îmbunătățirea productivității.
Pe două linii de numărul 1 și numărul 2 în magazin de îmbuteliere vodca „Tatarstan“ și „Lacul Albastru“ aceste pierderi aparente au fost descoperite care a necesitat o atenție urgentă de specialiști: întârzieri, avarii, tranzițiile, scurta oprire, defecte, reprelucrare, pierderi la pornire echipamente. Toate aceste pierderi au contribuit la o scădere bruscă a productivității, o creștere a ciclului de producție și a costurilor.
În acest sens, în prima etapă de lucru privind introducerea echipei de producție slabă a decis să folosească trei instrumente ale acestui concept: sisteme 5S, SMED și TPM.
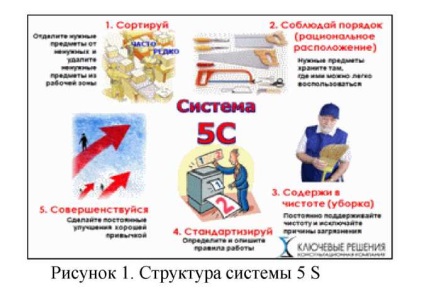
Sistemul SMED: etape și practici principale
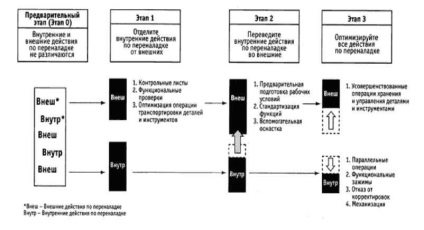
Figura 2. Algoritmul SMED implementarea sistemului
TPM System (Total Productive Maintenance) - «echipamente de îngrijire universală“, servește la îmbunătățirea calității echipamentelor, axat pe cea mai eficientă utilizare, datorită unui sistem general de întreținere preventivă. Acest lucru asigură faptul că o creștere a acestui indicator, deoarece eficiența deplină a echipamentului.
Ca urmare a punerii în aplicare a principiilor și instrumentelor de producție slabă în SA „Tatspirtprom“, au fost obținute următoarele rezultate: timpul și costurile de nefuncționare sunt reduse și capacitatea de producție a crescut. Rezultatele de introducere sunt prezentate în Figurile 3 și 4.
În ciuda semnificative aspecte pozitive, există unele dificultăți și limitări care trebuie depășite pentru a crea un sistem eficient de fabricație macră la fabrica:
• Nevoia de schimbări organizaționale semnificative și disponibilitatea personalului la aceste schimbări;
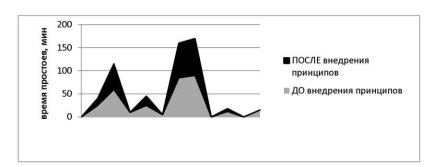
Figura 3. Timpul de repaus și a costurilor
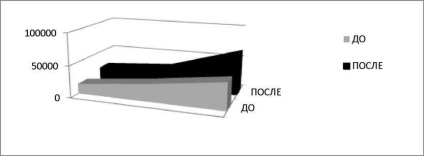
Figura 4. Produse de performanță
• posibilitatea de a costurilor materiale substanțiale;
• nevoia de interacțiune strânsă cu furnizorii, clienții, furnizorii și capacitatea de a livra produse de calitate corespunzătoare pentru o durată determinată;
• punerea în aplicare pe termen lung;
• lipsa de sprijin guvernamental adecvat.
Dificultatea constă în necesitatea de a utiliza aceste
instrumente tuturor personalului fabricii. În procesul de lideri de îmbunătățire continuă a stabili obiective, să inițieze o schimbare și să le ofere resurse și să mențină respectarea standardelor. angajații obișnuiți efectuează muncă standardizate și să ia inițiativa de a îmbunătăți activitatea susținută de sistemul de depunere a propunerilor și a cercurilor de calitate, în plus, de asemenea, să gestioneze propria situație în domeniul său de muncă. Toate acestea este imposibilă fără mentalitate specială a angajaților întreprinderii, în care este înțeles caracteristicile intelectuale și emoționale susținute care susțin aderarea la principiile menționate mai sus.
Având în vedere experiența de fabricație slabă, nu numai în România, ci în întreaga lume, putem vedea că este mentalitatea este principalul obstacol. scădere catastrofală a potențialului personal al industriei, pierderea prestigiului profesiilor de muncă și de muncă în fabrici, nivelul scăzut de gestionare, rezistența la schimbare - toate acestea conduc la dificultăți serioase în implementarea unor instrumente simple, cum ar fi 5S, TPM și SMED, care sunt baza pentru schimbări mai profunde.
Există exemple în cazul în care, sub rezerva politica de personal închis în termen de cinci până la șapte ani într-o companie separata format cultura economi, care permite realizarea deplină a beneficiilor tehnologiilor slabe. Aceste exemple arată că, chiar și cu probleme de Lean Manufacturing a menționat mai sus acum se deschide oportunități mari pentru a îmbunătăți eficiența și de a consolida poziția pe piață este cel mai promițător model de organizare de afaceri.
De ce nu există nici un efect de la introducerea de fabricație macră?
Dacă vă gândiți implementat cu succes și pe deplin de producție slabă, doar trei companii: Toyota, Honda si Danaher. Toate celelalte companii care au urcat pe calea punerii în aplicare a sistemului de producție, foarte superficial implicat în cererea de convenabil pentru ei instrumente Lean Manufacturing. Și, uneori, sunt irosite aceste eforturi.
Ca o regulă, în cele mai multe companii pentru a pune în aplicare de fabricație macră pe podea magazin. Ca urmare, în imposibilitatea de a obține rapid unele rezultate pozitive prin utilizarea celor mai comune instrumente. Cu toate acestea, măsuri suplimentare pentru punerea în aplicare a producției macră a încetinit în mod semnificativ în jos, deoarece acestea necesită sprijinul altor unități, ceea ce nu este. Principalul motiv pentru această situație - directori. Ei de multe ori nu înțeleg sau doresc să înțeleagă cât de adânc aveți nevoie pentru a înțelege filozofia Lean Manufacturing pentru a face să funcționeze în vigoare. Prin urmare, personalul proactiv la curbare în conformitate cu obiectivele realității și pe termen scurt existente ale companiei să devină o prioritate. Ca rezultat - punerea în aplicare a Lean Manufacturing dispare.
Astfel, folosind principiile și instrumentele de fabricație macră poate îmbunătăți semnificativ eficiența producției, calitatea produsului, productivitatea, reduce costurile de materiale și de timp, scurtarea timpilor de plumb, reduce perioada de dezvoltare a noilor produse, pentru a îmbunătăți competitivitatea companiei.
Odată cu introducerea sistemului de producție slabă, trebuie amintit faptul că producția de reorganizare - un proiect care necesită nu numai o analiză atentă și grijuliu, dar, de asemenea, o evaluare preliminară obligatorie a fezabilității punerii în aplicare. În plus, în prezent, există o dezvoltare activă de soluții informatice pentru automatizarea producției slabe, a căror utilizare în combinație cu sistemele de control convenționale este într-o mare măsură de ajutor pentru a optimiza punerea în aplicare a conceptului.
Ideile și metodele de producție slabă ar putea juca un rol crucial în transformarea sectoarelor individuale ale industriei românești și apropierea acesteia la nivelul țărilor dezvoltate de astăzi, pentru a le permite să reziste competiției la nivel mondial au crescut pentru consumatori și pentru a asigura dezvoltarea cu succes a afacerilor în economia mondială dur astăzi.