Tehnologia de sudarea prin topire electrică a metalelor și aliajelor
Atunci când se analizează tehnologia de durificare de metal de sudură este împărțit în tipuri, în conformitate cu AII de clasificare de proiectare.
stava preparate folosind sârmă de sudură standard, în combinație cu fluxuri convenționale AN-348-A, AN-60 și 45 OSC. Principalele caracteristici tehnologice ale suprafetelilor la fel ca sudarea otelurilor cu compozitie similara.
Metale și electrozi de sudură 80H4SG 60H2SM, respectiv 13KN / LIVT și EN-60M și metale și 45H5G 70HZMN - folosind alierea ceramice flux ANC-19 (St. wire-08A) și LM-sinterizate bandă 70HZMN.
de metal mangan Austenitice de tip C este recomandat pentru sudarea pieselor supuse unor abraziune, în combinație cu bătăi puternice. Un reprezentant tipic al acestui tip este oțel ON G13, care cuprinde aproximativ 1,2% C
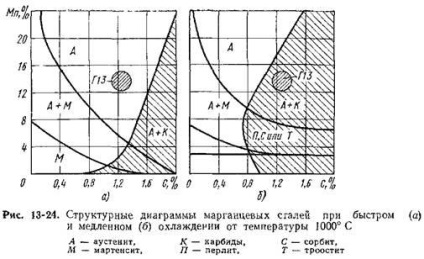
și 12% Mn. În funcție de conținutul de carbon și mangan, precum și viteza de răcire la temperaturi ridicate microstructura metalului de sudură devine diferit (Fig. 13-24) și proprietăți.
Răcirea rapidă la temperaturi mai mari de circa 950 ° C, care conține oțel 0.8-1.6% C și 12-20% Mn, dobândi o structură austenitică stabilă și se disting prin rezistență ridicată și ductilitate. Datorită solubilității ridicate a carbonului în soluția solidă y (cu un conținut mare de Mn) fara carburi. În această stare, duritatea metalului de sudură este scăzut, doar HB 180-220.
răcire lentă (vezi. Fig. 13-24) și descompunerea austenitei are loc de selecție a carburilor tip cementită la limitele granulei. Un astfel de metal sudură fragile, predispuse la fisurare și exfolierii. Carburilor sunt alocate încălzirii. De aceea, oțelul de tip C nu sunt recomandate pentru utilizare la temperaturi ridicate, în cazul în care este necesar să-și păstreze ductilitatea.
Suprafetelilor tehnologie oțelurile de tip C construct cu caracteristicile discutate mai sus. Pentru a evita embrittled-vanija strat depus și zona afectată de căldură (din oțel placare G13 110) procesul de sudare trebuie să conducă cu aport de căldură minime: curent și arcul tensiune mică, role înguste, creșterea ratei de depunere, procesul de încetare periodică și loc schimbarea de sudură .
În aceste condiții, precum și în timpul suprafetelilor pe părți masive ale vitezei de răcire este suficientă pentru a obține structura chistoaustenitnoy. Shirokosloynuyu suprafețe, care, în acest caz, creează un ciclu termic nefavorabil, de multe ori nu pot fi aplicate. Pentru sudarea cu electrozi înțepare și sârmă tubulara.
Atunci când la suprafață un arc deschis, ceteris paribus, acesta oferă o răcire mai rapidă a rolelor decât când ies la suprafață scufundat. Prin urmare, sudarea sârmă cea mai răspândită auto de ecranare flux-tubulara, de exemplu PP-AN105 (vezi. Tabelul. 13-8). Metalul de sudură este dopat suplimentar cu nichel (3-4%), stabilitatea crește austenită și devine posibilă creșterea ratei critice de răcire. Un defect comun de cristalizare fisurile care apar la niveluri ridicate de fosfor. Surfacing otel 110G13 pe otel carbon este utilizat mai puțin frecvent datorită șpagatul stratului depus.
Metal-bandă fabricate din pulberi de carbon pure permite suprafețe când conținutul minim mai multe straturi de carbon și o rezistență ridicată la stratul de coroziune intergranulară. Un exemplu de o astfel de bandă este bandă metalică LMA 00H21N9G (vezi. Tabelul. 13-11) utilizate pentru sudarea sub flux ponce AN-26 flanșe, țevi și vase echipamente chimice și petrochimice, precum și dispozitive de putere.
Oțel crom rezistent la coroziune este utilizat pentru suprafetelilor părți ale supapelor generale gaz și conducte de petrol industriale care funcționează la temperaturi de până la 400-450 ° C, prese și pistoane unele tipuri de matrițe, precum și camere de suprafață un traseu de curgere a turbinelor cu apă. Pentru suprafață armatură de conducte folosesc sârmă umplută cu interioare PP-AN106 si depunere camere pentru turbine hidraulice - sarma tubulara PP-AN138 (Tabelul 13-8 și 13-9 ..).
Pentru a se evita formarea de pori suprafețe trebuie efectuate la o tensiune de arc nu mai mare de 24-26 timbre tăiate V., precum și suprafețele de etanșare ale armaturii de sudură Electrozi VAW-2 (AHD tip 25H12-40). Atunci când conținutul de mai mult de 0,2% Deoarece metalic sudură este predispus la fisurare. Prin urmare, se aplică o încălzire preliminară și concomitent la o temperatură de 300-350 ° C
Kh12M oțel ledeburitic, scufundat arc de sudură H12VF tubulara fire ANYUZ PP și PP-AN104 (Tabel. 13-8 și 13-9). Surfacing oțel X12 conținând 1.8-2.0% C, implică anumite dificultăți din cauza tendinței de a formarea de fisuri la rece sudură din metal și cristalizare. Dacă fisura rece persistă piese încălzite la o temperatură de 400-550 ° C și răcirea lentă ulterioară, atunci acest lucru nu este întotdeauna posibil să se realizeze cu privire la fisuri de cristalizare.
fisuri Cristalizarea în oțeluri ledeburitic X12 apar datorită evoluției în timpul solidificării carburii de topire scăzut eutectic. Fisurile nu se produc cu condiția ca metalul de sudură conține 1,5-2,5% C. La un astfel de conținut de carbon crește cantitatea de eutectice, astfel încât se mișcă liber între dendrite Aust-niți și poate vindeca fisuri. Astfel, în timpul suprafetelilor oteluri X12 pentru oțel cu conținut redus de carbon ar trebui să depună eforturi pentru o proporție minimă a metalului de bază, altfel primul strat este lovit de fisuri de cristalizare din cauza unei cantități insuficiente de eutectic carbură de care se poate sparge vindeca.
X12 duritatea metalului de sudură este relativ scăzută și se ridică la HRC 40-44, datorită prezenței în structura unei cantități mari de austenită reziduală. Duritatea poate fi mărită prin călire, la o temperatură ridicată de 500-550 ° C (până la HRC 55-60). Pentru a putea suda produsul recopt de prelucrare. țagle maleabilizare trebuie efectuată de ciclu izoterm: încălzire la o temperatură de 870-900 ° C, care deține 1,0-2,0 ore, răcirea cu cuptorul la o temperatură de 700 ° C, care deține 5-8 ore, răcirea în continuare în aer. Duritate după recoacere a fost astfel HRC 25-29. Călirea produc duritate primară sau secundară, urmată de călire la regimuri de tip X12 a oțelurilor de scule de matriță.