În prezent, val de lipit este aplicată ca atașamente de lipire și componente SMD. proces de lipire este simplu. Carduri instalate pe banda transportoare sunt supuse fondant și preîncălzire, ceea ce exclude accident vascular cerebral de căldură în etapa de lipire. Apoi placa trece peste val de lipire. Unda în sine, forma și performanțele dinamice sunt cei mai importanți parametri ai echipamentului pentru lipit. Folosind forma de undă a duzei poate fi modificată; în instalațiile anterioare modele pentru val simetrice de lipit. În prezent, fiecare producător utilizează propria formă de undă (în forma literei grecești „omega“, în formă de Z, în formă de T, etc.). Direcția și viteza fluxului de lipire ajunge la bord poate varia, de asemenea, dar ele trebuie să fie aceeași pe întreaga lățime a undei. Unghiul de înclinare a transportorului este de asemenea ajustat pentru plăci. Unele instalații pentru deshuntiruyuschim lipit echipat cu un cuțit de aer, care prevede o reducere a cantității de jumperi de lipire. Cuțitul este situat direct în spatele porțiunii undei de sudură și care trece în funcțiune atunci când aliajul de lipit este încă în stare topită de pe placa de circuit. Fluxul îngust de aer încălzit, se deplasează cu viteză mare, poartă cu ea excesul de lipire, distrugând astfel nervurilor și facilitând îndepărtarea resturilor de lipire.
Tehnologia procesului de lipire în val poate fi împărțit în următoarele operații:
- fondant, eliminarea excesului de flux;
- preîncălzire;
- de lipit;
- răcire.
Cerințele generale de clasificare și metode de încercare fluxuri lichide moderne sunt date în standardul IPC / ANSI-J-STD-004 „Cerințe pentru fluxuri de lipire“.
Fondarea se realizează de obicei în două moduri:
- fondare spumă
- spray
Pentru metoda de aplicare a fluxului de spumă fondanți se utilizează filtre tubulare care formează spumă cu bule fine, oferă o mai bună umectare, în special atunci când prin placare.
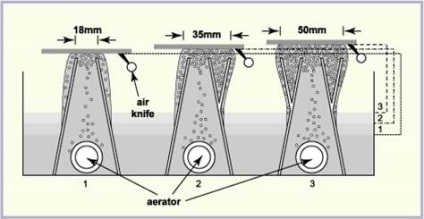
Avantajele acestei metode de aplicare a fluxului - echipamente de cost redus și ușurința procesului de configurare fondant. Printre neajunsurile pot fi evidențiate - un consum mare de flux și necesitatea de a fi drenate și se spală bine cu flux de spumare de piatră după fiecare ciclu de lipit.
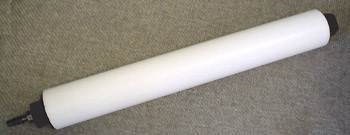
Filtrele Tubular care formează o spumă cu bule fine
Optimul piatra dimensiune a porilor este de 3-10 microni. Înainte de a instala piatra trebuie spălate într-un solvent.
Fluxare condiții optime poate fi atins atunci când înălțimea spumei mai mică de 2 cm.
Când fluxare spumă trebuie eliminată scurgeri, stropiri, suflare (cuțit aer) flux pe partea superioară a plăcii de circuit în conectorul de margine.
Pentru a îndepărta excesul de flux de pe suprafața plăcii cu circuite în fluxare spumă
se recomandă utilizarea unui cuțit de aer.
Acest dispozitiv reduce cantitatea de reziduuri de flux după lipire, și reduce contaminarea zonei de preîncălzire.
Este o conductă cu găuri pe aceeași linie, în care aerul este furnizat sub presiune. cuțit de aer stabilit sub banda transportoare, perpendicular pe acesta din urmă.
Unghiul recomandat cuțit de aer de înclinare de 10 ° între planul plăcii și planul fluxului de aer cuțit. cuțit aer direcția de curgere ar trebui să fie împotriva direcției de mișcare bord. Distanța dintre cuțitul de aer și zona fondant trebuie să fie de cel puțin 10 cm, în scopul de a preveni suflarea spumei de flux.
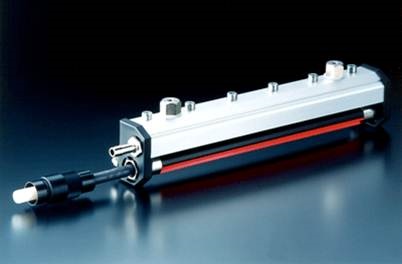
Distanța recomandată între placa de circuit și un cuțit de aer. - presiunea aerului de 5 cm este selectat astfel încât să se asigure îndepărtarea excesului de flux. În acest caz, fluxul nu ar trebui să fie expus la partea de sus a PCB, în conectorii de margine. Fluxul de aer nu este, de asemenea, ar trebui să arunce în aer flyusovatelya spumă.
Fluxare prin pulverizare cu ajutorul duzelor de pulverizare care se deplasează (flux pulverizare simultană) către modulul electronic, se deplasează de-a lungul transportorului.

Metoda de pulverizare fondant este preferată din mai multe motive:
1. Eliminarea oxizilor de contaminare cu flux și alte impurități sunt îndepărtate de pe suprafața PCB.
2. Controlul precis al grosimii fluxului, acoperirea unei plăci cu circuite imprimate (1 până la 2 microni).
3. Reducerea cantității de reziduuri de flux de pe placa de după lipire.
4. Stabilirea unei condiții prealabile tehnologice pentru trecerea la tehnologia bezotmyvochnuyu.
5. Reducerea consumului de flux.
6. Excluderea aproape completă de contact cu fluxul de aer, creșterea duratei de utilizare.
7. Reducerea evaporarea solventului.
8. Contaminarea redusă zona fondant și preîncălzită.
Dezavantajul acestei metode este costul ridicat al echipamentului.
Când fluxare pulverizare trebuie să împiedice pătrunderea fluxului pe partea superioară a plăcii de circuit în conectorul de margine.
2. bord preincalzire
Scopul preîncălzirii este de a pregăti placa de circuit imprimat în contact cu valul de lipire și reducând șocul termic.
Un alt proces nu mai puțin important - îndepărtarea solventului. evaporarea incompletă a solventului conduce la formarea nediferențiată de bile de lipire atunci când sunt expuse circuite imprimate bord și val de lipire.
Astfel, preincalzirea este necesară pentru:
• încălzirea plăcii cu circuite imprimate cu componente electronice pentru a reduce șocul termic;
• După îndepărtarea solventului din fluxul;
• activarea fluxului.
Temperatura Selectarea Preincalzirea depinde de proiectarea PCB,
Temperatura de evaporare a solventului.
Surse de incalzire utilizate pentru preîncălzire:
în infraroșu IR, convecție, cuarț.
Pentru o fluxuri pe bază de alcool sunt moduri convenționale, astfel cum sunt enumerate mai jos:
Atunci când se utilizează un flux pe bază de apă este necesară creșterea temperaturii de preîncălzire la 130-140 ° C (PCB) pentru evaporarea completă a apei (fără exces de zel principal și să ia în considerare temperatura care se menține componente montate pe placa).
Atunci când se lucrează cu un multi-strat plăci cu circuite imprimate o atenție specială trebuie acordată o încălzire temeinică în sus, care este de a asigura calitatea lipirea prin găuri placate.
Modificarea temperaturii într-o etapă de preîncălzire trebuie efectuată într-un ritm care să nu depășească 2 ° C / s.
În cazul încălzirii insuficiente și îndepărtarea parțială a solventului, la fluxul de lipire are loc gazarea în valul de lipire, impietează umectarea și poate duce la concluzii nepropayam componentelor.
Temperatura de lipire în zona de lipire poate fi stabilit în intervalul 235-260 ° C Temperaturile mai scăzute de lipire pentru a reduce șocul termic la componentele electronice și placa de circuit imprimat, oxidarea aliajului de lipit, dar din cauza creșterii tensiunii superficiale este capabilă să dea naștere la nepropaev, conectori, crampoane de lipire. Temperaturi mai mari de până la 260 ° C este de obicei setat la plăcile cu circuite imprimate multistrat de lipit. Pentru a asigura o bună calitate a îmbinărilor sudate este necesară pentru a asigura perioada totală de lipire în intervalul de la 2,5 la 4 secunde. Timpul de contact cu aliajul de lipit, de asemenea, depinde de temperatura de lipire. De exemplu, de obicei, la o temperatură de 250 ° C este suficient de 2,5 sec, iar la 235 ° C, în timp de lipire trebuie crescută la 3,5 sec. Temperatura reală a suprafeței PCB poate fi măsurată prin profilurile de dispozitiv de măsurare a temperaturii, de exemplu, senzor de transfer.
Pentru a seta înălțimea valului de lipire se recomandă utilizarea plăci de testare din sticlă rezistente la căldură, cu scala milimetrica. Pentru placa cu un singur strat, cu o înălțime de lipire optimă de undă trebuie să acopere 1/3 din grosimea de PCB.
Valori orientative pentru adâncimea de scufundare a PCB în val de lipire este prezentat în tabelul de mai jos: