Setări pentru sudarea automată a cusăturilor longitudinale de cochilii - în stoc!
De înaltă performanță, confort, ușurința de gestionare și fiabilitate.
Sudarea ecrane și perdele de protecție - în stoc!
protecția împotriva radiațiilor la sudare și tăiere. Sortiment mare.
Livrare in toata România!
Proprietățile undelor ultrasonice
Metoda de detecție defect cu ultrasunete a metalelor și a altor materiale a fost dezvoltat pentru prima oară și practicat în Uniunea Sovietică în 1928-1930 gg. prof. S. Ya. Sokolovym.
Undele ultrasonice sunt oscilații elastice ale materialului mediu, a cărui frecvență se află în afara domeniului de audibilitate 20 kHz (undă de frecvență joasă) la 500 MHz (unda de înaltă frecvență).
vibrațiile ultrasonice sunt longitudinale și transversale. În cazul în care particulele de medie mișcare paralelă cu direcția de propagare a undei, o astfel de undă este o secțiune transversală longitudinală, dacă este perpendiculara. Pentru a găsi defecte în suduri utilizate în principal val transversal îndreptate la un unghi față de suprafața componentelor sudate.
Valul ultrasonic poate pătrunde în materialul de mediu la o adâncime mai mare, refractate și reflectate în contact cu o delimitare între cele două materiale cu diferite permeabilitate a sunetului. Este această abilitate a undelor ultrasonice utilizate în testarea cu ultrasunete a sudurilor.
vibrații ultrasonice pot fi distribuite într-o varietate de medii - aer, gaz, lemn, metal, lichide.
Viteza de propagare a undelor ultrasonice C se determină prin formula:
unde f - frecvența oscilațiilor cps;
λ - lungimea de undă, cm.
Pentru a detecta defecte mici în sudurile trebuie să fie utilizate pe unde scurte unde ultrasonice ca valul, care este mai mare decât mărimea defectului, nu se poate detecta.
Prepararea undelor ultrasonice
Undele ultrasonice sunt mecanice, termice, magnetostrictiv (magnetostricțiunea - o modificare a magnetizării dimensiunea corpului) și piezoelectric (prefix „piezo“ înseamnă „push“) moduri.
Cel mai comun este ultima metodă se bazează pe efectul piezoelectric al anumitor cristale (cuarț, sare Rochelle, titanat de bariu), în cazul în care fețele opuse ale tăieturii plăcii de cristal, sunt incarcate electric opus, cu o frecvență de peste 20.000 Hz, ritmul semnului de încărcare al plăcii de schimbare va vibra prin transmiterea vibrațiilor mecanice în mediu sub forma unui val de ultrasunete. Astfel, vibrațiile electrice sunt convertite în mecanică.
Diferitele sisteme utilizate generatoare de defecte cu ultrasunete de înaltă frecvență la placa piezoelectrică definind oscilații electrice de la sute de mii la câteva milioane de Hertz.
plăci piezoelectrice pot servi nu numai ca emițătoare, receptoare, dar, de asemenea, cu ultrasunete. În acest caz, sub acțiunea undelor ultrasonice pentru cantități mai mici de sarcini electrice apar pe cristal se confruntă cu receptoare care au înregistrat dispozitive speciale de amplificare.
Metode pentru detectarea defectelor cu ultrasunete
Există două metode de ultrasunete defect: (. Metoda reflectat vibrațiile) umbră și puls ecou
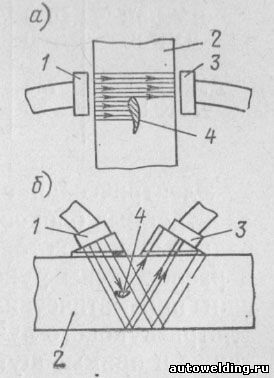
Fig. Schema 41. de testare cu ultrasunete
și - o umbră; b - ecou metoda impuls; 1 - emitor sondă; 2 - detaliu cercetat; 3 - Receptor sondă; 4 - defect
Atunci când metoda de umbră (. Figura 41 a), undele ultrasonice se deplasează prin cordonul de sudură de la sursa de ultrasunete (sonda-emițător) la o întâlnire cu defectul nu pătrunde prin ea, deoarece limita defectului este o limită între două medii diferite (metal - zgură sau din metal - gaz). Pentru o regiune defect este format din așa-numitele „umbre de sunet.“ Intensitatea vibrațiilor ultrasonice au primit sonda receptor scade brusc, iar valoarea variației pulsului pe ecran catodic detector tub defect indică prezența defectelor. Această metodă este de utilizare limitată, după cum este necesar accesul în ambele sensuri la cusătură, și, în unele cazuri, necesare pentru a elimina armatura de sudură.
Dacă metoda puls ecou (Fig. 41.6) emițător sondă trimite prin impulsuri de sudură ale undelor ultrasonice care, atunci când se confruntă cu un defect reflectate de ea și sonda receptor capturat. Aceste impulsuri sunt fixate pe detector defect ecran tub catodic ca vârfuri care să indice prezența defectului. Prin măsurarea timpului de la trimiterea unui puls la recepția semnalului de retur poate fi determinată și adâncimea defectelor. Principalul avantaj al acestei metode este că, controlul poate fi realizat dintr-o parte cordonului de sudură fără a îndepărta amplificarea cusătură sau pre-procesare. Această metodă a fost utilizată cel mai des în defectoscopia cu ultrasunete a sudurilor.
Pulsul defectoscoape cu ultrasunete
Verificarea sudurilor se realizează prin intermediul detectorului de ultrasunete defect care pot detecta fisuri „penetrare slabă, incluziuni de zgură și gaz în cap la cap, unghiulare, T articulații și lap executate sudare cu arc electric, electrozgura, gaz și sudarea contactelor. Controlul este posibil ca sudarea otelurilor si sudarea metalelor neferoase și a aliajelor acestora.
defect Diagrama schematică care constă din componente electronice individuale, este montat într-o carcasă metalică, panoul frontal care este un ecran cu tub catodic și aranjate maneta de comandă. sonde defectoscoape echipate cu prismatice solicitanții (Figura 42.) Din fasciculul ultrasonic de intrare unghiuri de 30, 40 și 50 ° (0,53; 0,7 și 0,88 rad). De asemenea, sonde și directă, prin intermediul cărora vibrații ultrasonice sunt introduse perpendicular pe suprafața obiectului de testare atașat. Probe Kit vă permite să alegeți pentru fiecare caz are nevoie de sondare. Toate sondele ca o placă transductor piezoelectric utilizat titanat de bariu.
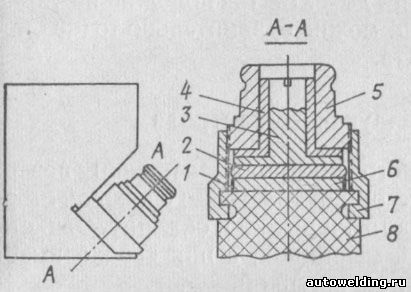
În funcție de numărul de sonde și un circuit de comutare defect lor cu ultrasunete poate fi dvuhschupovymi în care o sondă este un emițător și celălalt receptor sau odnoschupovymi, în care intrarea funcției și recepționarea undelor ultrasonice sunt efectuate de către o sondă. Acest lucru este posibil deoarece recepția semnalului reflectat are loc în timpul pauzelor dintre impulsuri, atunci când nici alte semnale, cu excepția nu se reflectă furnizat la placa piezoelectrică.
O diagramă bloc tipică a unui detector în impulsuri de ultrasunete defect acționat la circuitul odnoschupovoy prezentat în Fig. 43.
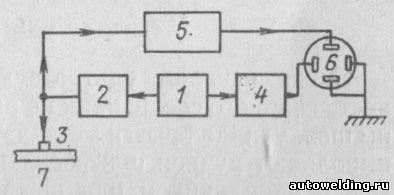
Fig. 43. Schema bloc a detectorului de ultrasunete defect de puls SPL-7H
1 - generator de conducere; 2 - un generator de impulsuri; 3 - sonda piezoelectric; 4 - generator de baleiaj; 5 - primirea amplificator; 6 - Tub cu fascicul de electroni; 7 - produs controlat
Oscilatorul de master alimentat de curent alternativ, generează oscilații electrice transmise la generatorul de impulsuri și sonda piezoelectric. De ultima inalta frecventa vibratiilor electrice sunt convertite în vibrații mecanice de frecvență ultrasonică și trimise produsului controlat. Intervalele dintre impulsuri individuale trimite sonda piezoelectric ridicată cu un comutator electronic conectat la un amplificator receptor care amplifică sonda derivată din vibrațiile reflectate și le trimite la ecranul tubului catodic. Astfel, sonda piezoelectric funcționează alternativ ca emițător și receptor de unde ultrasonice.
Generatorul Sweep oferă un tub fascicul electronic de scanare, care se bazează pe o linie luminos ecran tub catodic cu vârf al impulsului inițial.
In absenta unui defect al pulsului element monitorizat atinge suprafața de jos a articolului reflectat de acesta și de a reveni la o sondă piezoelectric. Aceasta vibrații frecvență ultrasonică mecanice sunt convertite în frecvență înaltă oscilații electrice din nou amplificate în amplificatorul receptor și alimentat la un catodice plăci tub de deflexie. În acest ecran există un al doilea impuls de fund vârf (ca în cazul reflectată de produsul de jos).
În cazul în care calea de defect întâlni cu ultrasunete, apoi o parte a undelor reflectate de ea înainte de semnalul ajunge la partea de jos a sondei piezoelectric. Această parte a receptorului de undă este amplificat în amplificatorul este furnizat la ecranul cu tub catodic și la baza ei între vârful inițial și puls impulsuri generate de un defect.
Datorită generatorului sincron fasciculului de scanare, generatorul de impulsuri, și alte dispozitive de defect impulsuri de poziție reciprocă pe un aranjament de afișare tub catodic caracterizează adâncimea defectului. Plasarea pe ecranul receptorului pe scară largă timp ștampila, puteți determina cu precizie relativ adâncimea defectului.
Metoda de testare cu ultrasunete
Înainte de începerea testării cu ultrasunete a suprafeței de sudură este curățat în regiunea de 50-80 mm pe fiecare latură a cusăturii, îndepărtarea resturilor stropilor, zgură și Zgura. Curățirea efectua polizor manual, dar, de asemenea, cu o cârpă fișier sau șmirghel, dacă este necesar.
Pentru a asigura un contact acustic între sondă și piesa de prelucrat-vizor, suprafața metalică curățată în mod direct, înainte de control este atent șters și aplicat ei ungere strat de contact. Ca lubrifiant aplicat avtol clasele 6, 10, 18, compresor, transformator sau ulei de motor.
Apoi verifica corectitudinea citirilor detector defect pe sudurile de referință cu defecte predefinite.
Rosturile de se realizează prin setarea alternativ sonda de pe fiecare parte a sudurii inspectate.
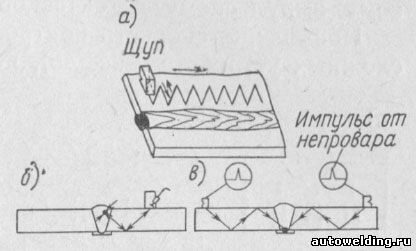
Fig. Schema 44. de testare cu ultrasunete
și - deplasarea sondei prismatic pe suprafața produsului; b - Controlul direct al fasciculului; în - controlul fasciculului reflectat
In monitorizarea sonda căutător lin deplasat pe ambele părți ale liniei de sudură zigzag (fig. 44 a), de cotitură în mod sistematic la 5-10 ° în ambele direcții pentru a detecta defectele localizate în mod diferit.
produc Ensounding atât direct (fig. 44, b) și reflectate (fig. 44, c) grindă. îmbinări cap la cap, atunci când grosimea de metal peste 20 mm, în mod normal sunt verificate fascicul direct. Când grosimea de metal mai mică de 20 mm câștig cusătură face imposibilă instalarea sondei, astfel încât un fascicul de ultrasunete a trecut prin rădăcina sudurii. În aceste cazuri, controlul este efectuat raze reflectate individual sau de două ori. Când grosimea de metal sub 8mm prozvuchivayut sa reflectat în mod repetat fascicul.
mișcarea Limite stiloului peste sudură depinde de unghiul fasciculului de intrare și metoda de sondare și determinat de nomograms prevăzute cu instrucțiunile privind funcționarea detectorului defect. Pentru a se asigura că deplasarea sondei în limitele prescrise, acestea sunt plasate într-un suport special (fig. 45).
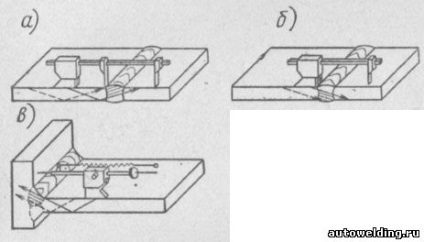
Fig. 45. Titularii sonde prismatice
și - pentru controlul îmbinărilor cap la cap reflectate grindă; b - controlul sudurile cap la cap fascicul directă; în - pentru controlul sudurilor
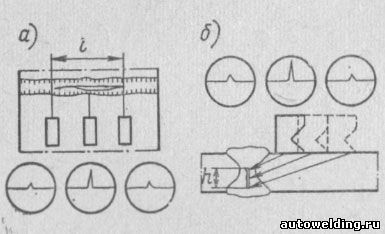
Fig. 46. Dimensiunile defectelor de circuit de determinare într-o cusătură cap la cap
și - lungimea l; b - înălțimea h
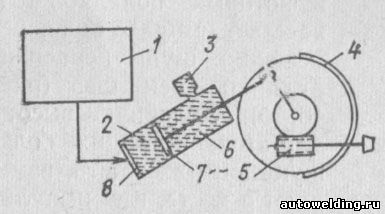
Fig. 47. Diagrama structurală a profundorul lichid
1 - generator de defect; 2 - un cilindru; 3 - compensarea volumului; 4 - adâncimea; 5 - mecanism pentru deplasarea pistonului; 6 - un lichid; 7 - pistonul; 8 - placa piezoelectrică
În cazul în care un defect în defectul de sudură apare pe puls. Lungimea condiționată a lungimii sale de deplasare măsurată de-a lungul zonei schupaiskatelya cusătură, în interiorul căruia există apariția și dispariția pulsului (fig. 46 a). Înălțimea defectului condițional este definită ca diferența dintre adâncimile măsurate în poziții extreme schupaiskatelya în care apare și dispare puls când sonda este deplasată perpendicular pe axa îmbinării (fig. 46 b). Înălțimea defectului condiționată de o lungime considerabilă, măsurată în locul unde pulsul defect are cea mai mare amplitudine.
Adâncimea defectului este determinată prin intermediul adâncimii. Adâncimea de lichid (Fig. 47) constă dintr-o placă piezoelectric, care este excitat de un generator defect simultan cu principala placa piezoelectrică radiante schupaiskatelya. Această placă este plasată într-un cilindru cu un volum compensator. Cilindrul este umplut cu lichid și are un piston asociat cu scala de adâncime. Când sondare pe tubul de sudură cu raze ecran catodic cu un fund și un semnal inițial apare așa-numitul puls aeriene reflectat de adâncimea cilindrului pistonului. Poziția pe ecran a defectului tubului determinată de poziția pistonului în cilindru. Deplasarea pistonului, aliniat cu pulsul de serviciu impuls reflectat de defect, iar scara determină adâncimea adâncimii defectului lui. Atunci când sunt combinate cu pulsul pistonului inferior poate determina grosimea metalului. Asemenea limitatorilor de adâncime poate fi atașat la orice detector în impulsuri de ultrasunete defect.
Ridicarea de control al vitezei poate fi realizată folosind dispozitive simple (Fig. 48), care permite deplasarea de-a lungul defectului de sudură și reciprocates sonda. Sonda căutător montat pe dispozitivul de cărucior și este conectat cu detectorul de ultrasunete defect. În același mecanism mișcare transport este compus dintr-o putere a motorului de 12 W, perechi de viermi și mecanismul manivelă.
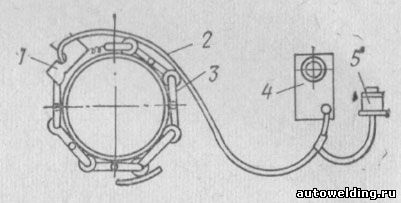
Fig. 48. Circuitul imbinarilor automate de comandă de conducte cu un dispozitiv special
1 - mecanismul de control; 2 - o conductă; 3 - lanțul cu role; 4 - cutie cu sonda; 5 - Defect cu ultrasunete
fiabilitate crescută semnificativ și de control al vitezei, folosind un ultrasunete defect automat Dowse-169, permițând sudurile să controleze grosimea când folia 6 până la 16 mm. Acesta reprezintă un senzor montat pe căruciorul se deplasează în mod automat, cablul flexibil conectat la dulapul cu componentele electronice.
Defectele sunt înregistrate pe o bandă de înregistrare diagramă și kraskootmetchikom pe cusătură controlată, a cărui activitate este duplicat lumini de avertizare. Viteza de control este de 1 m / min. Utilizarea sa crește foarte mult fiabilitatea și performanța procesului de inspecție a sudurilor.
Înregistrarea rezultatelor testelor
Rezultatele defectoscopia cu ultrasunete, în conformitate cu GOST 14782-69 fixat într-o revistă sau în stare de arest, indicând cu atenție:
a) tipul de sudat în comun; Codurile atribuite acestui produs și îmbinarea sudată; lungimea unei porțiuni de sudură controlată;
b) condițiile tehnice în care inspecția a fost efectuată;
c) tipul de defect;
g) frecvența vibrațiilor ultrasonice;
d) unghiul de intrare al fasciculului în metal sau tip crawler controlate sau sensibilitatea de limitare convențională;
e) porțiunile de cusătură care nu sunt supuse defectoscopia;
g) rezultatele inspecției;
h) data inspecției;
și) numele operatorului.
Când o descriere prescurtată a fiecărui rezultat de inspecție defect indică un grup separat.
Lungimea defectului caracteristic este indicată de una din literele A, B, C. Numerele indică: numărul de defecte ale piesei;. Lungimea defectului condițional în mm; adâncimea cea mai mare a defectului în mm; cea mai mare înălțime defect convenționale în mm.
litera A indică faptul că lungimea defectului nu depășește specificațiile admise. Litera B este utilizat pentru a descrie un grad mai mare de defect de tip A. litera B reprezintă un grup de defecte, distanțate la o distanță nu mai mare decât valoarea condițional pentru lungimea de tip A. defect
Aici este un exemplu abreviată rezultatele inspecției efectuate de înregistrare într-un jurnal sau în stare de arest.
Pe cusătură porțiune sudate C15 de compus (GOST 5264-69), indicat prin indicele MH-2, 800 mm lungime au fost găsite: două tip defect A la o adâncime de 12 mm, un tip de defect B lungime convențională de 16 mm, la o adâncime de 14-22 mm, o înălțime de convenționale 6 mm și un defect de tip B lungime convențională de 25 mm, la o adâncime de 5-8 mm.
Rezultatele testelor prescurtare este după cum urmează:
C15, MH-2, 800; A-2-12; B-1-16-22-6; In-1-25-8.
Siguranța în testarea cu ultrasunete
Prin colaborarea cu defectoscoape cu ultrasunete permite persoanelor care au fost instruiți cu privire la reglementările de securitate și au licența corespunzătoare. Înainte de a efectua un control la o înălțime mare, în spații închise sau în interiorul structurilor metalice operatorul trece o instrucțiune suplimentară, iar funcționarea sa este controlată de către serviciul de siguranță.
Este interzisă efectuarea lucrărilor de sudură apropiere de control în absența protecției împotriva razelor arcului electric.
LP Shebeko, AP Yakovlev. „Controlul calității îmbinărilor sudate“