Una dintre cele mai răspândite în lumea conceptelor logistice este conceptul de Just-in-time -JIT (exact la timp). Apariția acestui concept se referă la sfârșitul anilor 1950, cand compania japoneza Toyota Motors, iar apoi alti producatori auto firmele japoneze au început să pună în aplicare în mod activ sistemul KANBAN.
Conceptul inițial a fost excepția sloganul JIT potențiale stocurilor de materiale, componente și produse semifinite în procesul de fabricație de asamblare mașini și unitățile lor principale. Problema inițială arată astfel: dacă setați programul de producție, este necesar să se organizeze o mișcare a fluxurilor de materiale, astfel încât toate materialele, componente și produse semifinite primite în cantitatea potrivită, la locul potrivit (pe o linie de asamblare) și exact la timpul stabilit pentru producerea sau asamblarea produsului finit. În această formulare a problemei mai multe rezerve de asigurare, înghețarea fondurilor societății, sunt inutile.
Conceptual, JIT -Suitable a servit ca bază pentru punerea în aplicare ulterioară a conceptelor / tehnologii, cum ar fi Lean Production logistica, ( «plat“ sau «subțire» de logistică de producție) și valoarea adăugată -. «Logistica valoare adăugată“
Este de a izola și caracteriza ideea fundamentală a metodei, care se bazează pe trei ipoteze (care a fost confirmat în mod empiric în mod repetat corect).
În primul rând, se presupune că cererile consumatorilor de produse finite trebuie să respecte rezerve cu ea nu pre-acumulate și capacitatea de producție, gata de a fi materii prime prelucrate, a primit aproape „cu roți.“ Ca urmare, volumul stocurilor, capacitatea de calificare ca congelată este redusă la minimum.
În al doilea rând, în ceea ce privește rezervele minime obligatorii raționalizarea continuă a organizației și managementul producției, pentru volumul mare de niveluri de inventar, într-un măști sens greșelile și deficiențele din acest domeniu, locul îngust de producție, non-sincronizate funcționare, capacitatea de producție neutilizate, lucru nesigure furnizorilor și distribuitorilor .
În al treilea rând, pentru a evalua eficacitatea procesului de producție, în plus față de nivelul fondurilor de cost și de performanță ar trebui să ia în considerare perioada propunerii, așa-numita lungime a ciclului de producție. termene scurte de punere în aplicare a propunerilor facilitează gestionarea societății și să contribuie la creșterea competitivității, cu capacitatea de a răspunde rapid și flexibil la schimbările în condițiile externe.
Spre deosebire de metodele convenționale de administrare, în conformitate cu care elementul central al problemelor de planificare comenzilor de producție de producție toate departamentele și unitățile industriale, folosind metoda „just in time“ se referă de planificare centrală numai ultima verigă a lanțului logistic, t. E. produselor finite depozit. Toate celelalte unități de producție și de furnizare primesc comenzi direct de la un alt situat în apropiere de sfârșitul link-ul de lanț logistic. De exemplu, un depozit de produse finite aplicații date (ceea ce echivalează cu sarcina de producție de emitere) pentru un anumit număr de produse în sala de asamblare, atelierul de asamblare dispune de magazine fabricarea subansamblele de prelucrare și departamentul de cooperare și t. D.
Acest lucru înseamnă că obiectivul de producție este întotdeauna unitatea de ieșire care utilizează (sau proces) acest detaliu. fluxul de acest fel de material de la „sursă“ la un „consumator“ este precedată de un flux de informații în sens invers, adică producția "tocmai la timp" informații prealabile "just in time".
Baza acestui concept este credința că stocurile apar din cauza managementului defectuos, coordonarea slabă a muncii și, astfel de probleme sunt ascunse în rezerve. Am tras concluzia că este necesar să se găsească cauzele diferenței dintre cerere și ofertă, pentru a îmbunătăți performanța operațiunilor, după care stocurile vor dispărea. Conceptul de Just-in-time (Just in Time) conduc la schimbări în atitudini în următoarele domenii:
· Stocurile. Organizațiile trebuie să identifice și să rezolve problemele, ceea ce duce la stocuri, tinzând la un nivel minim (inventar zero) resurse materiale, în procesul de lucru și a produselor finite.
· Calitate. Nu este necesar pentru a atinge un nivel acceptabil de căsătorie, iar absența sa completă într-un control integrat al calității.
· Furnizori. Clienții trebuie să se bazeze pe furnizorii lor, astfel încât acestea trebuie să se stabilească parteneriate pe termen lung cu un număr mic de furnizori și transportatori de încredere.
· Părți de volum. Trebuie să căutăm modalități de a reduce volumul de loturi de producție, pentru a realiza cicluri scurte de producție pentru a produce un surplus care nu a acumulat în stocuri de produse finite.
· Timp de plumb. Este necesar să se reducă timpii de plumb, în scopul de a reduce incertitudinile, care ar putea schimba situația pentru o lungă perioadă de timp de livrare.
· Fiabilitate. Toate operațiunile trebuie să fie efectuate în mod continuu, fără întrerupere, adică, nu trebuie să existe avarii, căsătorie, absenteism, etc.
· Numar de angajati. Are nevoie de spiritul de cooperare, atât între lucrători și între manageri și lucrători, în calitate de fiind de toate depinde de succesul în procesul de muncă, toți angajații trebuie tratați în mod egal, un tratament echitabil. Incurajati orice inițiativă creatoare, exprimată de către orice angajat cu privire la posibile îmbunătățiri ale lucrărilor.
· Suport informational ar trebui să permită schimbul rapid de informații și de a sincroniza toate procesele de furnizare a resurselor materiale, producție și asamblare, furnizarea de produse finite.
Astfel, JIT - nu este doar un mod de a minimiza inventar, dar, de asemenea, pentru a elimina risipa de toate tipurile de resurse, pentru a îmbunătăți coordonarea și eficiența.
Una dintre primele încercări de punerea în practică a conceptului JIT tocmai la timp să devină o corporație sistem dezvoltat de Toyota Motors KANBAN (în japoneză - „Card“). Sistemul KANBAN este un prim „tragere» JIC la locul de muncă cu privire la punerea în aplicare, care de către firma Toyota a inceput de dezvoltare a durat aproximativ 10 ani. O astfel de perioadă lungă de timp, datorită faptului că sistemul KANBAN foarte nu a putut funcționa fără mediu logistic adecvat.
Elementele cheie ale acestui mediu au fost:
· Organizarea rațională a producției și a echilibrului;
· Un management cuprinzător al calității în toate etapele procesului de producție și a calității resurselor de materii prime de la furnizori;
· Parteneriat cu furnizori de încredere și transportatori;
· Îmbunătățirea responsabilității profesionale și de etică a muncii ridicată a personalului.
Sistemul KANBAN. pionier de Toyota Motors Corporation în 1972 la uzina „Takahama“ (Nagoya), este un sistem de organizare a producției continue, care vă permite să schimbați rapid producția și necesită stocuri mici sau nici o asigurare. Esența sistemului KANBAN este că toate unitățile de producție ale instalației, inclusiv linia de asamblare finală, furnizat resursele materiale numai în cantitatea și pentru astfel de termen, ceea ce este necesar pentru îndeplinirea ordinului, sdelannnogo diviziune-consumator. Astfel, spre deosebire de abordarea tradițională a unui producător de unități structurale de producție nu are program operațional greu generale și de a optimiza activitatea în volum ordine, ca urmare a ciclului de producție și diviziunea tehnologică a companiei.
Micrologistical Sistemul KANBAN este generat de producție linie de asamblare, dar principiile sale pot fi aplicate pe tot parcursul lanțului de aprovizionare și în orice tip de producție. KANBAN este „trage“ un sistem care este controlat de cererea in punctul „dreapta“, a lanțului logistic.
Scopul principal - de a face numai cantitatea necesară de producție în funcție de sfârșitul cererii sau un intermediar (următor) consumator. De exemplu, atunci când sunt necesare componente de pe linia de asamblare, acestea sunt furnizate cu site-ul de producție anterior în lanțul în cantitatea potrivită și la momentul în care acestea sunt necesare. Și așa mai departe de-a lungul lanțului logistic al producției.
Sistemul KANBAN reduce semnificativ stocul de resurse materiale la intrare și a produselor neterminate la ieșire, care să permită identificarea „blocaje“ în procesul de producție. Managementul poate direcționa atenția asupra acestor „blocaje“ pentru a aborda cele mai profitabile mijloace. În cazul în care problema este rezolvată, volumul stocurilor tampon a scăzut din nou, până când nu există urme de „strangulare“. Astfel, sistemul KANBAN vă permite să setați echilibrul în lanțul de aprovizionare prin minimizarea stocurilor în fiecare etapă. Scopul final - „optime consumabile una dintre părți.“
Mijloace de transmitere a informațiilor în sistem este un card special KANBAN într-un plic de plastic. Frecvente două tipuri de carduri: ordinea de selecție și de producție. Selecția cardului indică numărul de piese (componente, produse semifinite), care ar trebui să fie luate la porțiunea de prelucrare anterioară (asamblare), în timp ce comanda de producție în card - numărul de piese care trebuie să fie fabricate (asamblat) în locul de producție precedent. Aceste carduri sunt vehiculate atât în cadrul companiilor Toyota, precum și între societatea și să interacționeze cu firme, precum și la întreprinderile de ramură. Astfel, carduri Kanban transporta informații despre produsele consumabile și cantitățile produse.
Elementele importante ale sistemului KANBAN sunt suportul informațional, inclusiv nu numai cărți, dar, de asemenea, tehnologia de placă grafică de producție, transport și furnizare grafica, tablouri de bord de informare, etc.; nevoile sistemului de reglementare și de rotație a personalului profesional; sistem integrat (MCT) și selectiv ( "Jidoka") de control al calității; Alinierea sistem de producție și un număr de alte persoane.
Punerea în aplicare a sistemului KANBAN. și apoi versiunea modificată vă permite să:
1. să îmbunătățească în mod semnificativ calitatea produsului;
2. reduce durata ciclurilor logistice, a crescut foarte mult, astfel, cifra de afaceri a capitalului societăților de lucru;
3. reduce costurile de producție;
4. elimina practic stocurile de asigurare și de a reduce în mod semnificativ activitatea în stocuri de progres.
Analiza mondială de aplicare experiență sistem Kanban multe companii de inginerie cunoscute arată că face posibilă reducerea stocurilor de 50% de mărfuri - 8%, cu un tiraj de accelerare considerabilă a capitalului de lucru și de a îmbunătăți calitatea produsului finit.
Exemplu ce ilustrează operarea sistemului KANBAN
Diagrama prezintă două centru de prelucrare (OC): OO1 folosind partea A pentru fabricarea B prefabricatului și OTS2 folosind produsul semifinit pentru fabricarea în C. Mai presus de toate, este necesar să se decidă cu privire la tipul de container care trebuie utilizat pentru fiecare poziție A, B C, și mărimea lor, adică, cât de multe unități din fiecare produs se pot încadra într-un container.
În sistemul nu există pe site-ul containere de depozitare a trece de la unul la altul OC folosind mijloacele de transport tehnologic.
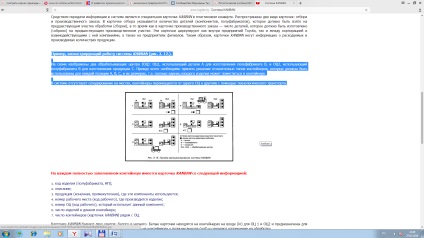
Pe fiecare recipient umplut complet are un card KANBAN cu următoarele informații:
1. Codul produsului (semi-NP);
3. Produse (finale, intermediar), în cazul în care se utilizează aceste componente;
4. Numărul de la locul de muncă (cod de lucru), în cazul în care este obținut produsul;
5. Camera OC cod (de lucru) care utilizează componenta activă;
6. Numărul de articole din container;
7. Numărul de containere (carduri Kanban) lângă OTs.
carduri Kanban vin în două culori: alb și negru. Carduri albe sunt pe containere la intrarea (în) pentru OZ 1 și OTS2 și sunt destinate să transporte. Carduri negru Kanban sunt pe containerele de la poziția de ieșire (out) și mijloace de prelucrare a permis.
Informațiile de pe carduri, care sunt atașate la containerele, se referă la un container specific.
articole negru Card C este ieșirea containerului gol. În acest caz, se referă la o soluție pentru OTS2 (de lucru pentru acest centru) pentru a produce produsul ca unități C după cum este necesar pentru umplerea unui recipient gol. Pentru acest OTS2 folosește un container în detaliu, unde au fost depozitate la intrare OTS2 și eliberează cartea de alb KANBAN (Schema 2).
Acest card autorizează transportul unui alt recipient cu articole din OO1 (ieșire) pentru a introduce OTS2. Lucrările la camion cu containerul nou liber și un card de alb vine la OO1, care îndepărtează placa neagră cu un recipient umplut cu detaliile și lăsați-l lângă containerul gol, iar cardul alb pentru a fixa containerul umplut cu detaliile și îl transportă la OTS2. carte de negru este gratuit pentru ca OO1 producția de piese de următorul container plin B. În procesul de fabricare a containerului este eliberat cu pozițiile A, și un card alb, servește ca un semnal pentru furnizor de piese de completare Un container unul, etc.
Exemplul de mai sus - o schemă tipică a sistemului logistic „tragere“ în instalație, în cazul în care containerele de (stoc de fabricație componente) piese se deplasează numai după detaliile de consum din secțiunile ulterioare.
Elementele importante ale sistemului KANBAN sunt suportul informațional, inclusiv nu numai cărți, dar, de asemenea, tehnologia de placă grafică de producție, transport și furnizare grafica, tablouri de bord de informare, etc.; nevoile sistemului de reglementare și de rotație a personalului profesional; sistem integrat (MCT) și selectiv ( "Jidoka") de control al calității; Alinierea sistem de producție și un număr de alte persoane.