Atunci când este încălzit în stratul de suprafață furnalele din articol este acoperit cu scală și decarburare. Această căsătorie crește odată cu creșterea temperaturii și creșterea timpului de staționare în cuptor.
Pentru componentele care nu sunt expuse la măcinare sau au o alocație mică pentru prelucrare ulterioară, această căsătorie incorigibil. Masuri de prevenire a produselor din scară și dedecarburare sunt: introducerea în cuptor a unui gaz special, pentru a evita, de asemenea, călire în apă și schimbările frecvente ale apei din rezervor de funcționare.
În practică, plante, în timpul întăririi unelte din oțel carbon configurație destul de complexă, ca quenchant folosit cu succes o soluție caustică 50 procente. Durificarea soluție de baie cu ventilație de evacuare trebuie să fie furnizate, deoarece o pereche a soluției formate în timpul călire, sunt nocive pentru organism.
Tabel. 7 prezintă datele. Uleiurile utilizate pentru călire și revenire a oțelului.
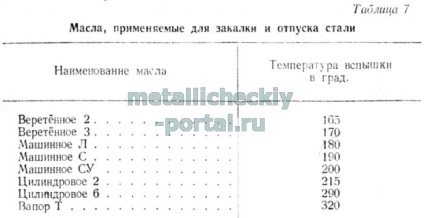
mediu bun pentru răcirea oțelului slab aliat și oțel carbon secțiuni mari mici este kerosenul având o viteză de răcire mai mare decât uleiul. Cu toate acestea, un dezavantaj al kerosen este inflamabil. Prin urmare, este necesar să se asigure că kerosenul nu este încălzit peste 35-38 °. Detalii evita contactul kerosen, este necesar să-l reducă rapid. Baie de temperare ar trebui să aibă un capac, care oferă o încetare completă a aerului în caz de incendiu.
templates plate disc freze și alte articole plate din oțel carbon la o grosime de 1 mm și până la 3-4 mm poate fi temperat oțel aliat între plăcile de răcire tubulare special echipate, în care circulă apa.
Atunci când se utilizează plăci solide dă rezultate bune ulei de lubrifiere în contact cu suprafața piesei de prelucrat călibile și deplasarea unei plăci în raport cu cealaltă. Placa de călire trebuie să fie plasate în ușa cuptorului, astfel încât produsul nu a avut timp să se răcească în jos atunci când îl transferați din cuptor.
Pentru oțeluri cu un aer austenită stabil poate servi ca un mediu de răcire furnizat de compresor sau ventilator, precum și aerul calm. La aer furnizat de compresor sau un ventilator de răcire, mai ales în timpul iernii, trebuie verificată înaintea stingerii, astfel încât linia de aer nu era apă, deoarece ei intrarea produsului poate provoca fisurarea.
In aplicarea sau stingerea izoterma în trepte într-un mediu de răcire sunt săruri de ulei sau de topire scăzut la cald. Deoarece temperatura lichidului de răcire trebuie să fie mai mare de 200 °, cel mai frecvent utilizate sare fuzibil topit. Tabel. 8 prezintă formulările sărurilor utilizate pentru baia de sare.
Atunci când cantități mari de baie de calire instrument solidificabil ar trebui să aibă o capacitate suficientă pentru a se asigura că mediul de răcire a fost fluctuații de temperatură nesemnificative. Dacă este necesar, sarea topită poate fi răcit prin suflare de aer uscat.
Metoda de selectare a călire depinde de compoziția oțelului, complexitatea produsului și proprietățile dorite.
Durificarea într-un răcitor, în special oțeluri carbon, însoțite cea mai mare rată de respingere a datorat fisurare și colmatare. Prin urmare, în acest fel produsul este stins doar o formă simplă și cimentată.
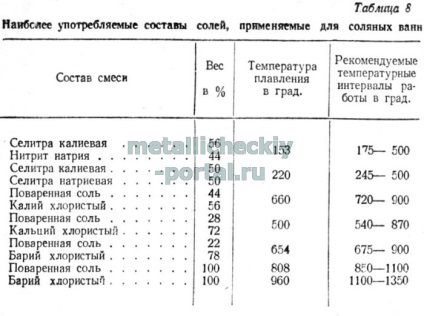
Călirea articole mai complexe fabricate din oțel carbon, produse în două răcitoare: mai întâi în apă, la o temperatură de aproximativ 150-180 °, apoi uleiul.
Durata de înmuiere în apă pentru transfer și instrumentul kalilschikom determinată în ulei mărime medie este de aproximativ 2-5 secunde. de exemplu, bucata de oțel U8A 5 x 25 x 180 mm este răcită în apă timp de 2 secunde. și apoi transferat la ulei. Duritatea după călire Rc = 61 - 63. răcirea părții în apă timp de 5-6 secunde. Acesta a dat 50% -70 căsătorie datorită formării de fisuri.
Pentru întărirea produselor cu găuri străpunse și găuri înfundate sunt utilizate în principal struychataya întărire. Răcirea se realizează într-un jet de duș cu apă sau abur. După produs rumenire pentru a evita autorevenire este răcit în ulei.
Structura acicular trostita și duritatea proiobretaet produsului R0 = 40-50 în combinație cu o vâscozitate ridicată. În această metodă de călire cazuri de cracare și colmatare sunt drastic reduse. De fapt, instrument izoterma durificare este rar folosit din cauza duritate scăzută. Tabel. 9 prezintă cilindrul de răcire în săruri cu temperaturi diferite.
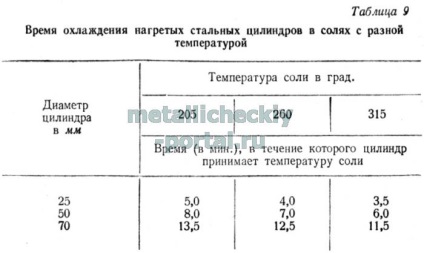
În practică, aceasta a justificat pe deplin ea însăși urmează o etapă de stingere:
În practică, tratamentul termic de instrumente, uneori combinate călire, revenire. O astfel de călire este în principal folosit pentru instrumentul de impact realizat din oțel carbon în care duritatea ar trebui să scadă de la porțiunea de lucru a gambei.
călire proces cu autorevenire fi realizată în această ordine: un instrument încălzit la temperatura de stingere; porțiunea inferioară de lucru a apei înainte de închidere la culoare; îndepărtat și curățați rapid porțiunea fișierul de lucru șmirghel și m. p. și când o decolorare instrument dorit răcit în ulei.
Procesul tehnologic al metodei quench este după cum urmează: 1) încălzire articol la o temperatură dorită; 2) călirea oțelului la un răcitor convențional; 3) refrigerare suplimentară la o temperatură -70-80 °; 4) pleacă.
După răcire la temperaturi joase, există tensiuni interne suplimentare, care pot provoca fisurarea. fisuri Măsuri de avertizare sunt călire viteza și răcirea lentă la temperaturi sub punctul de îngheț. Pentru a evita apariția de fisuri nu scufundați produsul direct într-un sistem de răcire, de asemenea, trebuie mai întâi să le zavortyvat la azbest sau de a folosi frigiderul, cu pereți dubli. Ca agent de răcire cu azot lichid utilizat, oxigen lichid, și m. P.
Calirea cu căldură în electrolit. Această metodă de întărire a dezvoltat câștigătorul premiului Stalin Ing. I. 3. Ploaie-oraș. Esența procesului este după cum urmează: o tensiune de curent continuu nu mai mică de 180 este trecut prin electrolit care servește ca anod și elementul, care este catod, provocând catod, o mare cantitate de căldură, o parte de încălzire la o temperatură ridicată. Electrolitul soluții apoase de săruri de sodiu, calciu, magneziu, bariu utilizat.
Au fost dezvoltate și utilizate în următoarele metode de fabricare de încălzire în electrolit:
1. Limita de încălzire utilizat pentru încălzirea capătului liber al articolului. În cazul în care elementul are o muchie ascuțită sau un con, sfârșitul izolat sale, stabilind pe un stand fabricat din cărămizi refractare și coborâte împreună cu ea în electrolit. După ce curentul este oprit partea de încălzire, iar partea este stinsă în electrolit.
2. Suprafața de încălzire locală și folosită pentru încălzirea electrolitului în orice porțiune a părții, de exemplu într-o întărire a rolelor jantei sau, părțile rotunde cu diametru mare și m. P.
3. încălzirea graduală care cuprinde acea parte a piesei, cufundat în electrolit poate fi împiedicat de încălzire. Această metodă de încălzire secvențial o parte sau întreaga parte.