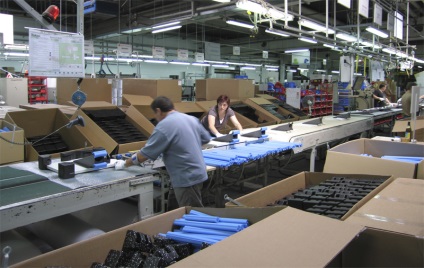
Am pregătit o serie de articole cu privire la metodele moderne de management al producției. Ne-am dorit să începem cu un concept numit „producție slabă“.
Principiile acestei filozofii de management este originar din Japonia, care le-au dezvoltat pentru a crea sistemul de producție Toyota a companiei. Cu toate acestea, ne acorde atenție și de a promova aceste metode americani, atunci când la mijlocul anilor 1980 au fost brusc confruntat cu o invazie masivă de pe piața americană de automobile japoneze,
avantajos diferă de producția de „industriei auto, locale“, de calitate și fiabilitate. Întrucât cele mai strălucite minți din America au fost aruncate pe studiul acestui fenomen - conectat specialiștii de la Institutul de Tehnologie din Massachusetts și alte universități și centre. Rezultatele au arătat că nu este nici mai mult, nici mai puțin, în tranziția către o nouă eră economică, care a început în Japonia, dar va devora în mod inevitabil, întreaga lume. Dacă părăsiți o eră definită ca „timpul de producție în masă“, noul - un „timp de producție slabă» sau «timp de producție slabă“ - care a tradus acest termen în limba română.
Cuvântul englezesc „lean“ literal înseamnă „slab, subțire, slabă, slabă, slabă, chiar și pe cei săraci.“ Menit capabil să livreze un produs cu resurse minime. Poate că ar fi mai bine de sunet „producție slabă“, producția tonifiat „dar a prins termenul“ producție slabă“. Și, uneori, numit LIN (de la macră) pentru concizie.
Aplicarea Lean presupune un anumit mod de gândire, luând în considerare orice activitate în termeni de valoare pentru client și pentru a reduce toate tipurile de pierderi.
Lean de fabricație se bazează pe următoarele principii:
1) se concentreze pe crearea de valoare pentru consumator și o reducere a pierderilor
2) Organizarea fluxului de valoare
3) Asigurarea flux continuu pentru valoarea.
4) "Sifon" produs de consum (în contrast cu "push").
5) Căutarea excelență.
În primul articol ne-ar dori să se oprească la primul principiu ciclu - valoare. Valoarea unui bun sau serviciu este creat de către producător, cu toate acestea definite, nu poate fi decât utilizatorul final. S-ar părea că este un truism, și nu necesită nici o clarificare suplimentară. Cu toate acestea, în practică, se pare că cele mai multe companii nu inteleg corect ceea ce se așteaptă de fapt, consumatorul a produsului lor. Acest fapt reduce în mod semnificativ competitivitatea și numărul de comenzi.
Valoarea în pierderi slabe de producție, spre deosebire de ureche discordantă notate română, dar demn de numele, cuvântul japonez - Muda (accent pe prima silabă, nn -. „Sac gol“). Prin acest concept include tot ceea ce consumă resurse, dar creează nici o valoare. În cadrul conceptului de producție slabă a introdus un criteriu foarte simplu pierdere: toate că munca în cadrul companiei, pentru care consumatorul nu ar fi dispus să plătească (dacă el știa despre ea), ar trebui să fie tratate ca pierderi. Aceasta este o gamă foarte largă - de pază la intrarea în partea defectă, de la poalele eboșe care așteaptă să fie procesate, nu a organizat în mod optim acceptarea comenzilor. Acesta este, de asemenea, departamentul de dezvoltare ineficientă a noilor modele, depozitarea mărfurilor la depozite intermediare, etc, etc.
Această abordare face relevă faptul că activitatea utilă este de obicei mai mică de 25-30% - pierderea de repaus. Și dezvăluie potențialul puternic pentru optimizarea producției și de afaceri în general.
Tayiti Ono, CEO al Toyota, stabilit la momentul în care șapte tipuri de pierderi:
1. pierderile datorate supraproducției;
2. Pierderea de timp din cauza de așteptare;
3. Pierderi inutile în timpul transportului;
4. pierderile datorate etapelor de prelucrare suplimentare;
5. Pierderea din cauza excesului de inventar;
6. pierderi din cauza deplasării inutile;
7. Pierderea din cauza eliberării produselor defecte.
Mai târziu a fost adăugat al optulea tip de pierdere: pierderea potențialului creativ (utilizarea parțială a capacității de resurse umane).
1. Acțiunile care creează valoare;
2. Acțiunile care nu creează valoare, dar inevitabilă din mai multe motive, cum ar fi tehnologia, cum ar fi controlul calității, curățarea pieselor, ansamblu de control (Muda de primul tip);
3. Acțiunile care nu creează valoare, care pot și ar trebui să fie excluse din procesul (Muda al doilea tip).
Probleme cu definiția de valoare reală, datorită faptului că produsul este considerat din punctul de vedere al serviciilor întreprinderii individuale un pic diferit. Designerii vedea avantajele tehnice, designeri - uite, vânzare - preț și termeni etc. Un client este important și întregul complex de proprietăți ale produsului în sine, iar procesul primirii ordinului, iar ambalajul și de livrare, instalare si service. Mai mult decât atât, o lucrare amănunțită pentru a identifica preferințele poate duce la rezultate neașteptate - poate fi bine ca aceste „clopotele și fluierele“ care se afla în designeri de produse de consum nu destul de interesant, dar el este dispus să mărească prețul, chiar de dragul schimbării, de exemplu, gama de culori. firmele de multe ori concurează unul cu altul pentru livrare, iar clientul ar fi fericit să aștepte pentru realizarea unora dintre alte cereri sale.
producție Lean oferă, de asemenea, o abordare puțin diferită față de evaluarea nivelului costurilor. În mod tradițional, prețul este stabilit, astfel încât va fi capabil să „susțină“ pe piață. Și apoi costurile de calcul acceptabile determinate, oferă un grad de rentabilitate. Această abordare relaxează - pentru că nu sunt controlate minim, iar costurile „acceptabile“. Care, la un anumit moment din fluctuațiile prețului de piață poate fi devenit „inacceptabil“.
De multe ori, nivelul prețurilor și a costurilor în comparație cu aceste cifre pentru concurenți întreprinderi (benchmarking). Fără a lua în considerare caracteristicile sistemului de producție și organizarea proceselor în alte fabrici, ceea ce poate duce la concluzii false.
În Lean Manufacturing oferă o metodă diferită. Setați țintă cost minim, în funcție de cantitatea de resurse și a costurilor forței de muncă, cu condiția ca toate pierderile identificate sunt complet excluse din proces. Obiectivul este de a trece treptat la aceste scopuri și validarea fiecărui pas în fluxul de valoare: dezvoltarea, acceptarea comenzii, fabricarea produsului și punerea sa în aplicare.
Aceste costuri țintă sunt absolut minime, acestea sunt garantate să fie mult mai mici decât costul de concurenți. Prin urmare, eliminând nevoia de timp și efort de analiză comparativă și o oportunitate de a nu acționa orbește, dar cu o înțelegere clară a cauzelor de pierdere și potențială a fiecăruia de reducere a acestuia. Un instrument pentru a evalua eficiența fluxului de valoare este kartirirovanie - dar mai mult pe faptul că într-un articol viitor.
A se vedea, de asemenea.
- Lean de fabricație. GLOSAR
- Lean de fabricație. valoare curs de apa
Angajații Holz Expert oferă servicii de consultanță pentru întreprinderile de mobilier.
managementul productiei - profesiei noastre.
Scopul nostru - îmbunătățirea eficienței mobilei și prelucrării lemnului întreprinderi.
Dar, la fel ca toți profesioniștii, avem nevoie, uneori, pur și simplu pentru a vorbi: pentru a discuta știri, un schimb de opinii, de a împărtăși experiențe. De aceea, am decis să creeze blog-ul nostru pentru mobilier.
Nu putem garanta o expunere completă și sistematică a tuturor evenimentelor din industrie - blog-ul va fi publicat doar ceea ce ne interesează personal. Sperăm că va fi interesant pentru tine.
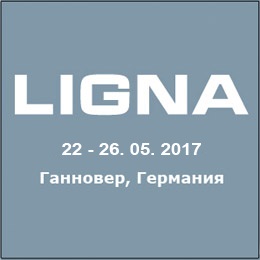
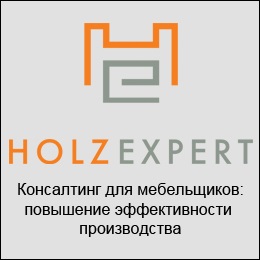