Selectarea țaglei inițiale
Pentru fabricarea detalii cum ar fi o flanșă pot fi utilizate astfel de metode de fabricație, ștanțare flanse inchise die forjare pe șaibe (presare), electrozgura centrifugal de turnare (TSESHL), producția de inele laminate (forjare), o plasma (laser sau gaz) tăierea din foaie.
Metoda cea mai productivă de fabricare a unei flanșe de perforare flanșe în matrițe închise. flanse cu diametre mai mari sunt realizate din inele laminate sau metode TSESHL.
Producere de piese de metal ștanțare volumetrica necesită cheltuieli considerabil mai mică decât forjare. Atunci când prelucrarea scade complexitatea pieselor forjate și cheltuiala instrumente de tăiere de prelucrare. Un avantaj important al forjare muri este mare performanta. Deoarece producția de masă, vom folosi o metodă de formare în matrițe închise.
Secvența de tratament de suprafață.
Deoarece piesa este realizată prin ștanțare într-o matriță închisă, tratamentul de suprafață, este suficient să două metode:
1.Rastachivanie T5K10 dur
2. Finish T15K6 Boring
Pentru a obține un produs fin artizanale, trebuie să eliminați cel puțin două cipuri. Prima trecere este numit degroșare, al doilea - finisajul sau decor.
Selectarea instrumentelor de tăiere
Capetele traverselor și notare tratate, prin pasaj sau prin pasaj îndoite incisivi de rezemare.
Scoring tăietor pentru prelucrarea suprafețelor de capăt exterioare. trunchiere tăietor cu alimentare de capăt este perpendicular pe axa piesei. Scoring instrument soclu permite să se ocupe de diferite fețe frontale și alte suprafețe, folosind alimentarea longitudinală și transversală.
Globul tăietor de îndoit se poate efectua tunderea de capăt în teren transversal și rotirii - atunci când se deplasează din fluxul de intrare.
Globul tăietor încăpățânat poate tăiați capetele și macină traverselor la furaje longitudinale.
Din moment ce avem nevoie de un instrument proiectat pentru degroșare și finisarea suprafețelor exterioare și de capăt, precum și șanfrenare, cel mai bine este să se apropie de intrare dalta îndoită.
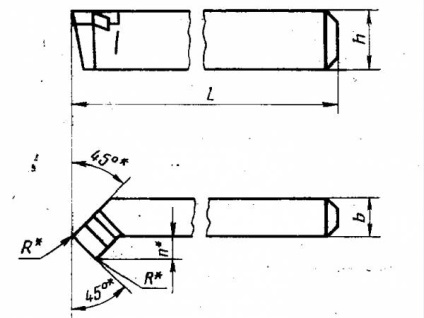
Calculul condițiilor de tăiere
1. Rezistenta la rupere: 45 din oțel are o rezistență la curgere de 600 MPa scurt
2. Rezistența la tracțiune MPa 170 Brinell
3. scoring Cutter, GOST 1050-88
Material Oțel 45: T5K10 pentru degroșare, finisare T15K6
4. Alocația totală de procesare h = 8 mm.
5. Diametrul D = piesei de prelucrat 125 mm.
6. Swing (după tratament) d = 120 mm.
7. Lungimea suprafeței de tratament l = 40 mm.
8. Rugozitatea dorită Ra = 2,5 m
Numirea adâncimii de tăiere
Când termina adâncimea de tăiere cotitură este luat t2 = 1 mm. Apoi, adâncimea de tăiere în timpul rotației dur este determinată de formula t1 = h / 2 - t2 = 8/2 - 1 = 3 mm, unde t1 - adâncimea de tăiere în timpul strunjire aspră, t2 - adâncimea de tăiere în timpul de cotitură finisaj.
Numirea sumei de aprovizionare
In timpul furaje degroșare este selectat conform tabelului. P 3.4
Astfel, S1 = 1,0 mm / rev (până la 0,7-1,2mm / v).
Când furajele de finisare este selectată conform tabelului. P 3.3 în funcție de rugozitatea suprafeței Ra = 2,5 mm și o rază r = 35 mm.
S2 = 0144 mm / rev.
hrana pentru animale de selecție specificate de către datele certificatului mașinii 16K20
Assigned următorul furaj: S1 = 1,0 mm / rev. S2 = 0,15 mm / rev.
Determinarea vitezei de tăiere și viteza arborelui
Determinarea vitezei de tăiere
Viteza de tăiere V, m / min, se determină prin formula
În cazul în care CV - factor în funcție de condițiile de prelucrare pentru degroșare
CV1 = 340; Finisare - CV2 = 420; T - rezistența cuter min (presupus
T1 = T2 = 60 min); x, y, m - exponenți (x = 0; y = 0.20; m = 0);
Kv - factorul de corecție totală reprezentând produsul dintre factorii individuali, fiecare dintre care reflectă efectul unui anumit factor de viteza de tăiere.
Pentru instrumente cu o placă de metal dur
în care Kμv - coeficientul de corecție totală ținând seama de influența fizico - mecanice ale materialului prelucrat fiind
Knv - un coeficient de corecție care reflectă starea de suprafață a piesei de prelucrat.
În timpul degroșare Knv1 = 0,8, atunci când finisare Knv2 = 1,0;
KUV - factor de corecție pentru a ține cont porțiune de tăiere material Kuv1 = 0.65;
Kuv2 = 1,0;
K # 966; v - ajustarea coeficientului de reflexie cuter unghi colț pentru # 966; = 45 # 730 ;;
K # 966; v1 = K # 966; v2 = 1,0;
Exponenții x, y și m:
Pentru degroșare - x1 = 0,15, y1 = 0,43, m1 = 0.20 (la S la 0,3 mm / rev.);
Pentru finisare - x2 = 0,15, y2 = 0,45, m2 = 0.20 (. S legare la 0,7 mm / rev.).
viteze de tăiere sunt egale cu m / m:
Viteza arborelui Determinarea
viteza de rotație n, rot / min, se determină, respectiv, pentru finisare și degroșare tratamente:
ax Rafinarea mașină de viteză pașaport
Pentru degroșare selectat 12 n1 etapă Transmission = 160 min-1.
pentru finisare selectat 16 Transmission etapă n2 = 400 min -1.
Determinarea vitezei reale de tăiere
Viteza VPH reală. m / min, determinată pentru, respectiv de degroșare și de finisare tratamente:
4. Verificați modul de tăiere selectat
Modul de tăiere selectat trebuie să verificați puterea unității axului mașinii
Puterea necesară pentru tăiere, Np ar trebui să fie mai mică sau egală cu puterea pe ax Nshp:
în cazul în care Ignorarea - putere strung cu motor, kW; pentru mașină 16K20
Ne = 10 kW; # 951; - eficiența strungului de antrenare a mașinii 16K20 # 951; = 0,75.
putere de taiere determinat prin formula
unde Pz - forța de tăiere, H; VPH - viteza reală de tăiere, m / s.
Pentru a determina puterea de tăiere pentru a determina forța de tăiere în timpul degroșare. forța de tăiere în timpul rotației se calculează după cum urmează:
unde Cp - coeficient ținând cont de proprietățile materialului prelucrat, materialul părții de tăiere a sculei de prelucrare și condițiile Cp = 300;
Kp - factorul de corecție totală numeric egală cu produsul dintre numărul de coeficienți, fiecare dintre care reflectă efectul unui anumit factor asupra forței de așchiere:
Kp = KMR K # 966; p K # 947; p K # 955; p,
în cazul în care KMR - factor de corecție care ia în considerare influența calității materialului prelucrat
K # 966; p - factor de corecție cont colț tăietor unghi, K # 966; p = 1,0;
K # 947; p - factor de corecție care ia în considerare unghiul tăietor greblă K # 947; p = 1,25;
K # 955; p - factor de corecție care ține seama de unghiul de înclinare a palei principale K # 955; p = 1,0;
Factorul de corecție K # 955; p. ținând cont de raza de la vârful cuțitului este determinat să accelereze instrumente de tăiere din oțel.
Apoi, factorul de corecție generală
Kp = 0,85 1,0 1,25 1,0 = 1,0625
Indicatori de gradul x, y și n sunt acceptate pentru degroșare:
x = 1,0; y = 0,75; n = - 0,15.
forța de tăiere în procesul de transformare:
PZ1 = 9,81 0,8 0,75 1 martie 62,8 -0,15 1,0625 = 5041,4 H.
putere de tăiere, kW
Puterea pe ax
Deoarece Np Ungere și răcire mijloace de procesare (MWF) sunt caracteristică obligatorie a majorității proceselor tehnologice de măcinare de prelucrare a materialelor. Sunt ulei mineral de viscozitate la 50 # 730; C, în general, de la 2 la 40 mm 2 / s Compoziția poate conține agenți de emulsifiere, inhibitori de coroziune, biocide, aditivi de presiune extremă protivoiznostno-, aditivi antispumanți, agenți de legare (apă, alcooli, glicoli, etc.) și alte substanțe organice și anorganice. miscibil cu apa de tăiere fluide au o serie de avantaje față de ulei: capacitate de răcire mai mare, de siguranță la foc și mai puține riscuri pentru sănătatea personalului care lucrează, soluții de lucru cost. Dar există, de asemenea, o serie de dezavantaje - a crescut susceptibilitatea microorganismelor, spumă, nevoia de reciclare a apelor uzate soluții. Cele mai multe dintre noi sunt fluide de tăiere adecvat miscibil cu apa ca noi suntem cele mai importante proprietăți pe care le posedă, adică, o mare capacitate de răcire. Ne se potrivesc "Ukrinol-1" (3%), emulsie (E) fără aditiv reactiv jet însumat la viteze de până la 300 m / s și un debit de 500 l / h. 1. Markov V. V. Calculul condițiilor de tăiere 2. Modurile de tăiere metalului: referință / V. Baranovsky. - ediția a 2-a. - M. Mașini, 1972.- 982 p. 3. Precizia de prelucrare a piesei de prelucrat și a certificatelor de emisii în inginerie mecanică. Tehnologie / referință AG Kosilova, RK Meshcheryakov, MA Kalinin.- M. Inginerie Mecanica, 1776. - 657s. 5. Lubrifiere și răcire fluide tehnologice pentru prelucrarea metalelor: un ghid / editat. Ed. SG Entelis, EM Berlinera.- M. Inginerie 1986.- 352 p.
Scopul principal al fluidului de tăiere - pentru a reduce parametrii de temperatură și de tratament de putere și de uzură a sculei de tăiere, moare, pentru a oferi o calitate a suprafeței satisfăcătoare. Utilizarea de tăiere fluidelor în tăiere și presiunea poate crește productivitatea echipamentului, pentru a îmbunătăți precizia suprafețelor prelucrate și pentru a reduce rugozitatea lor de suprafață, reduce căsătoria, pentru a îmbunătăți condițiile de muncă, în unele cazuri de metal, reduce numărul de etape ale procesului. La prelucrarea freze din oțel de scule, cele mai importante proprietăți de răcire ale fluidelor de tăiere.
În funcție de aplicație și cerințele SOTs sunt împărțite în clase:
(. antifrictiune, antiuzură, presiune extremă, oxidare, detergenți, anti-spumare, anti-coroziune etc.), fără aditivi sau cu aditivi pentru diferite scopuri funcționale, cu bune proprietăți lubrifiante, uleiuri și fluide de tăiere au dezavantaje: o capacitate de răcire scăzută, costul ridicat, volatilitatea crescută și inflamabilitatea.articole similare