În fiecare zi, sistemele de răcire cu apă devin tot mai frecvente. Producătorii eliberează tot mai multe soluții gata făcute. Cu toate acestea, nu este un secret că toate sistemele la un preț mai mult sau mai puțin acceptabil pierd răcitoare de aer bune, care sunt adesea mult mai ieftine și mult mai ușor de instalat și de utilizat. Sistemele, cu adevărat superioare răcirii prin aer, costă clienții cu cel puțin două sute de euro. Nu fiecare utilizator își poate permite astfel de costuri.
Reducerea semnificativă a costului construirii unui sistem de răcire lichid permite utilizarea radiatoarelor auto de pe încălzitor și acvariu sau pompă de fântână. Un astfel de radiator de cupru, cu posibilitatea de a sufla doi ventilatoare la 120 mm, va costa aproximativ 1000-1200 ruble, versiunea din aluminiu - aproximativ 600 de ruble. pompă - în valoare de 600 - 1000 de ruble. Cu toate acestea, rămâne cel mai important detaliu - blocul de apă.
Modelele de înaltă performanță vor costa mai mult de cincizeci de euro. În plus, le puteți cumpăra, de regulă, numai în magazinele online, ceea ce duce și la anumite dificultăți cu marcarea și livrarea (mai ales având în vedere dimensiunea țării noastre).
Singura cale de ieșire din această situație este de a face un bloc de apă pe cont propriu. Cu echipamentul de frezat, este doar o chestiune de tehnică. Ca urmare, veți obține un bloc de apă, nu inferior în frumusețea fabricii. Performanța depinde de designul ales de creator. Dar, din păcate, nu toți cei care doresc să aibă un sistem ieftin de răcire cu apă au acces la astfel de echipamente. Și nu pare să existe nici o cale de ieșire. Cu toate acestea, în acest caz, cum ar fi să scrieți o introducere atât de lungă?
De fapt, există o cale de ieșire, iar procesul de creare a unui bloc de apă fără echipament special va fi descris mai jos.
Deci, primul lucru pe care trebuie să-l faceți înainte de fabricație este să calculați cu atenție toate dimensiunile, să determinați proiectarea blocului de apă și a sculei.
După ce a studiat structura apei blocuri finisate, bazele teoretice de căldură și hidrodinamică, precum și bunul simț, am ales tipul de apă bloc pini cu formă de diamant pini secțiune transversală. Baza a fost decisă pentru a face o grosime de 5 mm, înălțimea pinilor - 8 mm. Forma și dimensiunile știfturilor după mult crezut că sa decis să facă următoarele: latura a tijei de 4 mm, propil între pinii 2 mm mai mic unghi, în ordinea de treizeci de grade pastilei. Desigur, stabilirea lucruri bune necesită materiale corespunzătoare, astfel încât alegerea a căzut pe o bara de cupru de formă cilindrică 60 mm în secțiune transversală. Cuprul este cel mai bun metal în ceea ce privește raportul dintre conductivitatea termică și preț. Instrumentul vom avea nevoie de: o menghină, fierăstrău (instrumentul principal), Dremel cu discuri de tăiere de diametru mare, (nu este necesară nici o cerințe speciale privind forma) un set de burghie, fișiere sau fișiere, șmirghel cu diferite uruială, un fier de lipit, sticluței de ulei cu ulei, riglă, creion sau marcator subțire.
Pentru a tăia piesa de prelucrat cu dimensiunea dorită, marcați cu un punct de riglă la o distanță specificată de margine, rotind în mod constant piesa de prelucrat. Ca rezultat, avem un set de puncte la aceeași distanță de margine, apoi pur și simplu le conectăm cu un marker. Linia rezultată este linia de tăiere.
Apoi fixați piesa într-un viciu.
Piesa de lucru în viciu
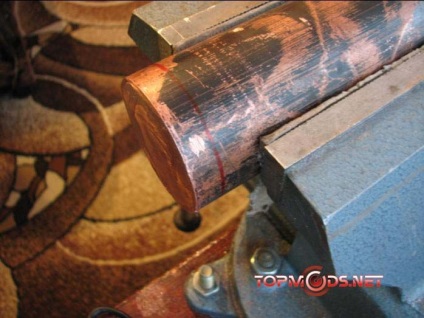
Pentru a vă asigura că nu există urme pe piesa de prelucrat de la fălcile viciului, am folosit plăcuțe groase de carton. Aproape toată munca a fost făcută cu folosirea lor, deoarece componenta estetică pentru mine a fost de asemenea importantă.
Este necesar să porniți ușor tăierea prin rotirea piesei de prelucrat, astfel încât ferăstrăul să nu aibă urzeală și piesa de prelucrat să aibă o grosime egală în toate părțile. Sa decis decuparea piesei cu o grosime de 14 mm. Această operație mi-a luat cam o jumătate de oră.
Un detaliu important îl reprezintă uleiul, care ar trebui să se strecoare în locul tăierii, când ferăstrăul a intrat în metal mai adânc de 3 mm. Acest lucru va facilita foarte mult procesul de tăiere, deoarece uleiul va reduce semnificativ forțele de frecare.
Următorul pas este fabricarea de pini. Pentru a face acest lucru, trebuie să tăiați viitorul radiator din matricea de cupru. Acest lucru se face, de asemenea, cu un ferăstrău. Anterior, după ce am subliniat limitele părții de lucru a viitorului radiator, am văzut excesul de pe margini.
Scoateți excesul de material din laturi
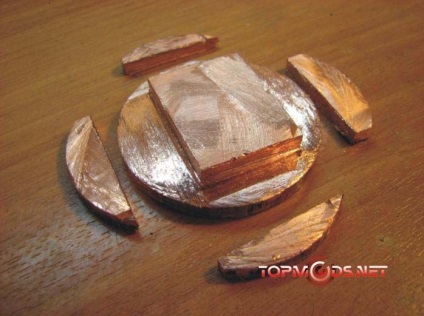
Procesul de fabricare a pinilor include trei etape. La inceput, marcam viitoarele reduceri cu un dremel. Acest lucru este necesar pentru a face mai ușor începerea tăierii cu un ferăstrău. Am preferat să folosesc un ferăstrău pentru tăiere, deoarece sa dovedit a fi un mod mai rapid, mai silențios și mai puțin costisitor. În procesul de tăiere, de asemenea, picurăm uleiul (am folosit o seringă veche de 5 ml și ulei de motor).
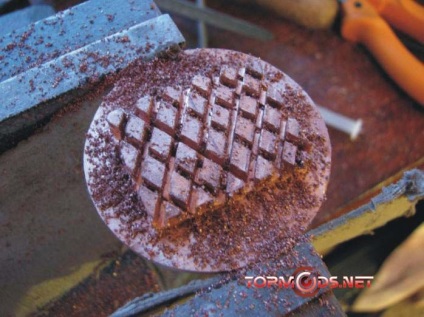
În etapa finală, vom aborda din nou dremelul, deoarece este foarte dificil din punct de vedere tehnic să se facă tăieturile la un nivel cu un ferăstrău. Este mult mai convenabil să folosiți cercuri cu diametrul suficient de mare. Am folosit cercuri de 45 mm, realizate independent de discurile de tăiere cu un diametru de 125 mm. Decupările mai profunde ar trebui să fie foarte atenți. Cuprul este un metal foarte vâscos, astfel încât oprirea lui dremel, chiar și la puterea maximă, este suficient de simplă. Și acest lucru poate duce la supraîncălzirea motorului dremel sau la deteriorarea duzei.
Baza rezultată pare puțin brută, poate fi procesată cu un filet de unghii pentru a îndepărta toate spărturile și colțurile ascuțite, pe care le-am făcut ulterior.
Semifabricate după adâncirea tăieturilor cu un dremel
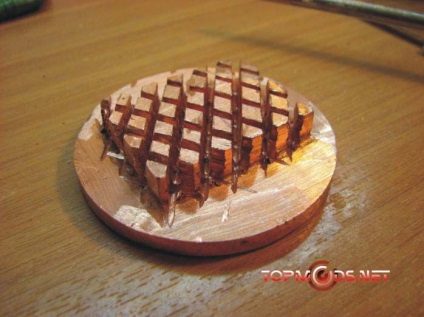
Cu foaie de cupru, alamă sau oțel inoxidabil, puteți suda cu ușurință capacul blocului de apă. Dar atunci ar fi impartita. În plus, astfel de materiale nu au fost găsite în vânzare. Prin urmare, sa decis să se facă un capac de două inele de plastic și o placă de oțel de 1,2 mm grosime. Și că oțelul nu corodează, era planificat să zaludit cu un fier de lipit.
Pentru inele, plasticul era de 4,5 mm grosime. Desigur, în acest caz este de dorit să se folosească o foaie groasă, dar acest lucru nu a fost găsit, deci a fost decis să se facă două inele. Pe foaie, am marcat un cerc cu un diametru de 60 mm. După aceea, două pătrari au fost tăiate dintr-o piesă mare, respectiv, cu o latură de asemenea 60 mm. În centrele golurilor s-au găurit găuri, pentru a le strânge cu un șurub și apoi pentru a lucra împreună. Folosind un ferăstrău pentru metal, am tăiat două cercuri din ele.
Blocurile sunt strânse cu un șurub și procesate împreună
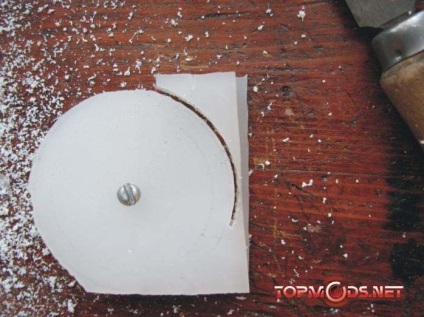
Pentru a îndepărta partea interioară, trasăm perimetrul găurii și tăiem cu grijă piesele transversale cu ajutorul fileului superior.
Din tabla de oțel, am tăiat un cerc cu diametrul de 60 mm cu ajutorul unui dremel. Găuriți găurile în blocul de apă și detaliile capacului. Am pus totul împreună folosind șuruburile M5 și le procesăm împreună într-un viciu pentru a oferi tuturor părților aceeași dimensiune. Pentru a elimina semnele brute din fișier, am folosit șmirghel cu o dimensiune a granulei de 320.
Tragem detaliile blocului de apă împreună și se înalță în viciu
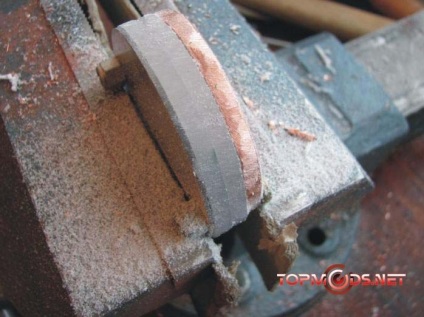
Aproape perfect chiar și talpa din blocul de apă
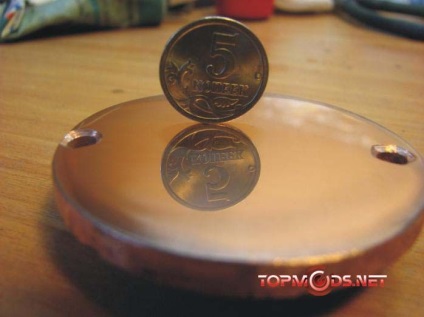
Un punct important în forarea unei baze este aceea că capetele șuruburilor trebuie să pătrundă complet printr-un material, deoarece plăcile de bază moderne întâlnite adesea condensatori de înălțime egală și procesor de suprafață dispuse suficient de aproape de soclu. Șuruburile proeminente le pot deteriora la instalarea blocului de apă. Pentru a vă asigura că sunt complet adânci, ar trebui să utilizați șuruburile cu capete încrucișate și să creați caneluri sub ele cu ajutorul unui burghiu mai mare. În special, am folosit un burghiu cu diametrul de 8 mm.
În cele din urmă, toate părțile blocului de apă sunt gata!
Piese finisate ale blocului de apă
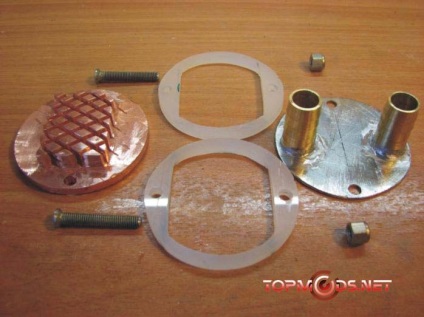
Următoarea etapă a fost fabricarea unei plăci de prindere, fără care blocul de apă este inutil. După meditații și un triplu de schițe, forma sa a fost determinată. Ca material, sa decis utilizarea unei foi de aluminiu de 2,5 mm grosime, deoarece practic nu este supusă deformării, ceea ce este foarte important în placa de presiune. Cu ajutorul unei plăci standard multicircule de la răcitorul procesorului, au fost planificate găuri de pe foaie. Apoi, folosind busola, rigla și marcatorul, conturul părții viitoare a fost evidențiat.
Aluminiu foaie de marcare
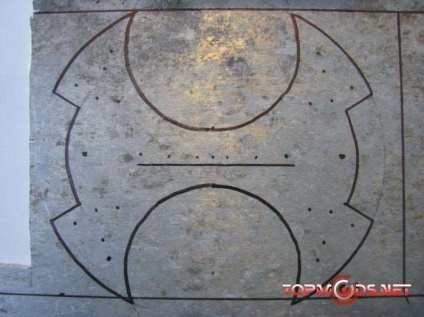
Folosind un ferăstrău pentru metal, a fost tăiat. Mai mult, au fost tăiate colțurile inutile ale piesei de prelucrat. Pentru a îndepărta părțile interioare ale plăcii, tăieturile au fost făcute la adâncimea maximă, apoi, de-a lungul perimetrului, unde nu era posibil să se facă acest lucru, a fost forat un număr necesar de găuri de un burghiu de 5 mm. Forarea lor în aluminiu nu este la fel de simplă cum pare. În ciuda locurilor de foraj planificate anterior cu ajutorul miezului, forajul în acest proces merge adesea în lateral. Prin urmare, am forat mai întâi găuri cu un burghiu de 4 mm, iar după corectare au forat un burghiu de 5 mm. După aceea, părțile inutile au fost sparte cu ajutorul cleștelor.
Scoaterea excesului de material
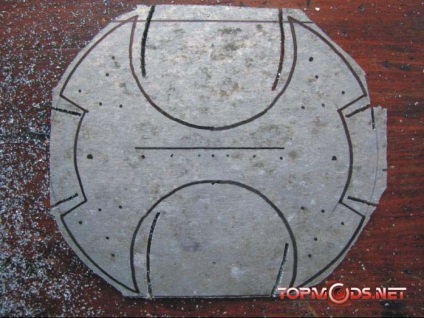
Găurirea găurilor pe contur
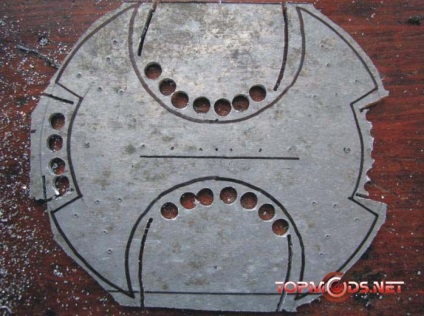
După ruperea excesului de bucăți de aluminiu cu clești
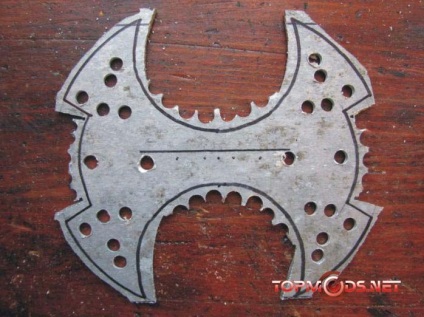
Următoarea etapă este cea mai laborioasă și mai dureroasă. Cu ajutorul unui fișier, metalul extra este șters și contururile se apropie de limitele prevăzute ale plăcii. La locul de muncă am folosit în esență un dosar plat și la prelucrarea marginilor curbe semicirculare. Pentru a elimina bastoanele și semnele din fișier, am folosit aceeași șmirghel. Rezultatul este o placă care se potrivește tuturor platformelor moderne și seamănă cu articulațiile din alamă din jocul Lineage II.
