Tratamentul termic al oțelului, ca urmare a modificării compoziției chimice a straturilor de suprafață, se numește tratament chimic-termic. Produsul este încălzit într-un mediu special selectat, iar compoziția chimică a suprafeței se schimbă datorită tranziției și introducerii atomilor acestei substanțe în rețeaua de cristal a oțelului.
Procesul de penetrare a unei substanțe în alta în contactul său se numește difuzie. În funcție de mediul în care produsul este încălzit, se disting mai multe tipuri de tratament chimic-termic. Cele mai frecvente dintre acestea din industrie sunt: carburizarea, nitrurarea și cianurarea.
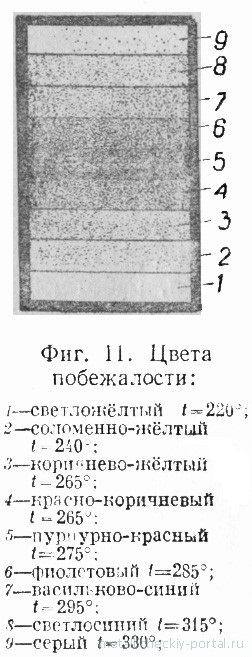
În producția de scule, cimentarea se folosește la fabricarea instrumentelor de măsură, a dispozitivelor, a anumitor tipuri de instrumente de montare etc.
Oțel de ciment într-un mediu solid, gazos și (rareori) lichid, capabil să-i dea carbonul. Aceste medii sunt denumite carburatoare.
Cimentarea într-un carburator solid. Ca un carburant solid în industrie, un amestec de cărbune cu săruri carbonat (carbonat de bariu, carbonat de sodiu, carbonat de calciu) este utilizat pe scară largă.
Pentru pregătirea carburatorului, cărbunele sunt zdrobite în bucăți de dimensiuni de 3-10 mm și se cernează pentru a îndepărta praful. Cărbune este folosit de stejar sau mesteacan, deoarece cărbuni din roci moi arde rapid. Sarurile carbonice se macină într-o pulbere și se cernează printr-o sită fină.
Prima metodă, în care se obține amestecul cel mai uniform, este după cum urmează: sarea este dizolvată în apă, cărbunele sunt turnate peste această soluție, amestecate și uscate. Umiditatea admisă este de 5-7%.
A doua metodă constă în amestecarea atentă a cărbunelui și a sării în formă uscată. Un carburizator slab amestecat dă un strat neuniform de carburizare, pată.
Multe fabrici folosesc un carburier gata fabricat de către uzina din Bondyuzhsky, din cărbune și din mai multe tipuri de săruri de carbonat. Carburatoarele fabricate de plante pentru nevoile lor constau, în general, din cărbune 85-90% și carbonat de sodiu (sodă calcinată) 10-15% în greutate. Pentru cimentare utilizați un amestec de 20-30% carburier proaspăt și 70-80% cheltuite. Pe plante individuale sunt utilizate în locul cărbunelui și rumeguș adăugat la carburizer os carbonizat, piele, și așa mai departe. N. Cu toate acestea, toți acești aditivi precum și înlocuirea cărbunelui praf, degradează calitatea cementarea.
Părțile care vin în vederea carburizării trebuie să fie uscate și fără scântei, rugină, murdărie, ulei, așchii etc.
Protecția suprafețelor produselor care nu sunt supuse cimentării. Secțiunile pieselor, care nu trebuie cimentate în funcție de condițiile tehnologice, protejează de carburizare în următoarele moduri:
1. Indemnizație rămasă în produsele prelucrate prin tăiere. În locurile în care nu se efectuează carburizarea, rezerva de alocare este mai mare decât adâncimea specificată de carburizare. Înainte de stingere, această cantitate este scoasă din mașină.
2. Aplicând o acoperire. Ca acoperire pusă în locuri care nu fac obiectul cimentării, se utilizează următoarele: a) argila amestecată cu sticlă lichidă; b) un amestec de granule de argilă, nisip și azbest, amestecat cu sticlă lichidă; a) un amestec de izolator termic pudră sau nisip de cuarț (75%) și la scară mică (25%), cernut printr-o sită cu 1 x 1 mm.
3. Încetinirea. Locurile care nu sunt supuse carburizării sunt acoperite cu un strat de cupru cu o grosime de 0,03-0,04 mm. Această metodă necesită un echipament galvanic special.
4. Fosfatarea. Locurile care trebuie carburat tsapon pre-acoperite cu lac, după care produsul este complet cufundat într-o baie de soluție apoasă fierbinte de fosfați acidului ortofosforic, locul de fosfatare produse neacoperite, care pot fi observate pe suprafața barbotare a soluției. Terminarea barbotării indică sfârșitul fosfatării. Procesul este simplu și sigur.
Piesele ce urmează a fi cimentate sunt ambalate în cutii cu un carburator. Cutiile sunt cel mai bine fabricate sub formă de piese. Acest lucru reduce timpul de încălzire a cutiilor și îmbunătățește calitatea stratului cimentat. Cu toate acestea, este suficient să fabricați astfel de cutii atunci când se efectuează cantități mari de carburizare. În toate celelalte cazuri, cutiile sunt rotunde, pătrate sau dreptunghiulare, dimensiunile lor fiind alese în funcție de dimensiunea cuptorului și de numărul de produse încărcate în ele.
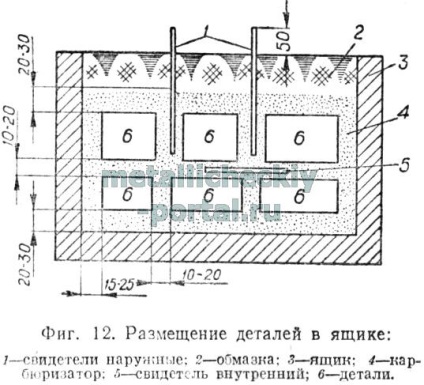
Cea mai mare dimensiune a cutiilor de carburizare în cuptoare cu o dimensiune medie de 250 x 500 x X 300 mm cu o grosime a materialului de 4 până la 8 mm. Materialul pentru cutii este oțel rezistent la căldură, iar în lipsa acestuia, oțel obișnuit cu conținut redus de carbon. La ambalarea pieselor în cutii, distanța dintre părți trebuie să fie de 10-20 mm, iar între părți și partea de jos 20-30 mm (Figura 12).
Atunci când componentele de ambalaj carburizer bine compactat, iar cutia superioară tencuit cu un amestec format din două părți de argilă și un râu de nisip parte, se diluează cu apă până la un aluat. Martorii sunt puse în cutie pentru a determina adâncimea de carburare o prezentare în interiorul pachetului pentru master de control, iar doi de control exterior pentru desfășurarea procesului de lucru în sine. Martorii sunt realizați din oțel de calitate 15 sau 20 cu diametrul de 8-12 mm.
Proces tehnologic de carburizare. Înainte de a încărca cutiile în cuptor, este necesar să se usuce stratul de acoperire astfel încât să nu crape. Încărcarea trebuie efectuată într-un cuptor încălzit la 900 - 950 °. Ca urmare a încărcării cutiilor frigorifice în cuptor, temperatura acestora va scădea într-o oarecare măsură. Încălzirea printe a cutiilor pentru producerea la o temperatură de 780-800 °. Practic, sfârșitul încălzirii este determinat de culoarea plăcii inferioare; cu încălzire insuficientă, placa de sub cutie va fi întunecată, iar cu încălzirea completă culoarea plăcii de bază va fi aceeași peste tot. După încălzirea cutiilor la o temperatură de 780-800 °, temperatura este ridicată rapid la 900-950 ° și procesul de carburizare este efectuat. Încălzirea rapidă a cutiilor la temperatura de cimentare imediat după instalarea lor în cuptor nu este recomandată, deoarece datorită diferenței mari de temperatură dintre centru și marginile cutiei cimentarea nu va fi aceeași. Durata îmbătrânirii, în funcție de adâncimea stratului cimentat, este dată în Tabelul. 12.
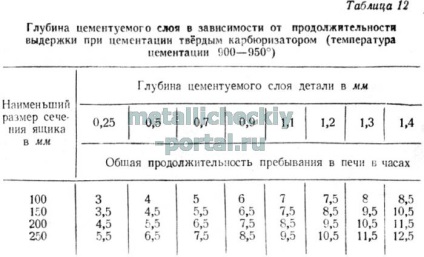
Sfârșitul procesului de carburizare este determinat de fractura martorului întărit. Unul dintre martori este scos din cutie și întărit cu aproximativ o oră înainte de presupusul sfârșit de carburizare, iar al doilea - până la momentul descărcării.
Adâncimea stratului cimentate este cel mai bine determinată prin gravarea reactiv martor fractură temperat constând din 100 cm3 de alcool denaturat, 1 cm3 de acid clorhidric și 2 g de clorură cuproasă.
Timpul de gravare este de un minut. Locurile care nu sunt cimentate sunt acoperite cu cupru.
Răcirea cutiilor după carburare se efectuează în aer. Despachetarea cutiilor fierbinți nu este recomandată, deoarece nu este sigură în combaterea incendiilor și nu este carburator consumat economic.
proces carburare Gas, dezvoltat de oamenii de știință sovietici NA Minkevich, SK Ilinsky Prosvirin și VI, se realizează prin încălzirea pieselor într-o atmosferă de gaze care conțin carbon. Comparativ cu un carburare carburizer solid în gaz carburare carburizer are următoarele avantaje: nu este nevoie de carburare pregătire; Reduce timpul de rezidență al cutiei cu părți din cuptor; numărul locurilor de muncă și atelierului necesar scade, iar condițiile de lucru se îmbunătățesc semnificativ. Piesele ce urmează a fi cimentate sunt așezate într-o muflă de cuptor încălzită la 900-950 °, etanșată ermetic și furnizată gaz.
Pentru cimentarea gazelor se folosesc următoarele: 1) gaze naturale (Dashavsky, Saratov, Priazovsky); 2) gaze artificiale; 3) generarea de gaze etc.
Din gazele artificiale, cea mai mare utilizare a gazului a fost preparată prin descompunerea produselor petroliere. Gazul de proces de preparare este ca kerosenul este alimentat picături într-un vas de oțel încălzit și în acesta se descompune într-un amestec de gaz (proces numit descompunere piroliză). O parte din gazul de piroliză este supus prelucrării ulterioare - procesul de cracare în care compoziția se schimbă de gaz, deoarece carburari un gaz de piroliză obținute depozite dense funingine pe detalii, adâncimea mică de carburare, etc. Pentru carburari, un amestec de 40% din gazele de piroliză și 60 .. % din gazul cracat.
Tratamentul termic al produselor cimentate
Piesele cimentate sunt supuse întăririi și temperării. Încălzirea se face dublu sau unic. Când primul dublu-călirea se realizează la o temperatură de 860 -900 ° pentru îmbunătățirea structurii de bază, iar al doilea, la o temperatură de 760 -800 ° pentru a conferi stratului exterior duritate.
Unele plante consideră că este rațional să producă o singură întărire la o temperatură de 760-800 °. Instrumentele supuse carburizării trebuie să aibă o duritate ridicată și, prin urmare, pot fi limitate la o singură întărire, cu excepția cazurilor specificate în tehnologie. După întărire, produsele sunt supuse temperării scăzute pentru a ușura solicitările interne. Instrumentul care trece carburizarea cu gaz poate fi turnat direct din mufla cuptorului de cimentare, răcit ușor în aer.
Nitridarea și cianurarea
Nitrurare. Procesul de nitrurare este saturarea stratului de suprafață al oțelului cu azot. Ca urmare a nitrizării, acest strat obține o duritate foarte mare și îl reține când este încălzit la 530-550 °. Pentru nitridare, se utilizează în principal oțel, care conține aluminiu, crom și molibden.
Procesul de nitrurare este trecerea amoniacului prin mufla etanșă ermetic în care se află componenta. Temperatura de nitrurare este de 500-600 °. Gazul, constând din azot și hidrogen, se descompune la această temperatură în părțile constituente, din care azotul penetrează în oțel, iar hidrogenul este îndepărtat din cuptor. Difuzarea azotului în oțel are loc foarte lent - în decurs de 40-90 de ore. Durata lungă a procesului și fragilitatea stratului nitridat sunt dezavantaje ale acestui tip de tratament.
Cianurare. Procesul de saturare a stratului de suprafață prin oțel cu azot și carbon se numește cianurare. Există două tipuri de cianurare: temperatură ridicată la 750-850 ° și temperatură scăzută la 530-560 °. În cazul instrumental, se utilizează, în principal, cianurarea la temperaturi joase a uneltelor fabricate din oțel de mare viteză pentru a crește durabilitatea acestora. Cianurarea se efectuează în mediu lichid, gazos și solid.
Cianurarea lichidă se efectuează în sărurile de cianură topită. Adâncimea cianurii depinde de compoziția băii și de durata expunerii.
Cianurarea este supusă unei scule prelucrate și ascuțite, astfel încât procesul trebuie efectuat cu atenție atât în ceea ce privește respectarea temperaturilor, cât și în ceea ce privește manevrarea atentă a sculei.
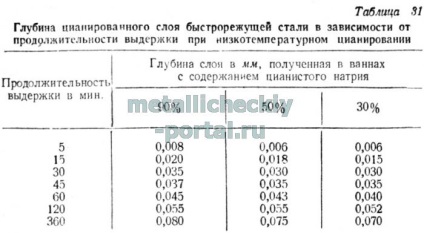
Cianurarea tare se efectuează într-un amestec de cărbune uscat (60-70%) și sare de sânge galben (30-40%). Pregătirea amestecului, ambalarea în cutii și învelișul se face în același mod ca și carburizarea. Durata de expunere de la 1 la 3 ore. în funcție de dimensiunea instrumentului. La sfârșitul expunerii, cutia este răcită în aer la o temperatură de 100-200 °, după care este despachetată.