Puteți face o comandă pentru materialele de construcție necesare sau de lucru.
Lăsați o cerere, iar furnizorii sau maeștrii vă vor trimite ofertele la oficiul poștal sau sunați înapoi.
Veți alege între ele cele mai bune oferte.
Lăsați o cerere Anulați
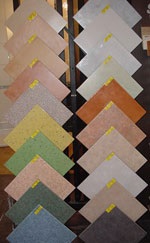
Granit ceramic - unul dintre cele mai durabile și rezistente la uzură materiale de finisare, chiar mai greu decât cele mai bune grade de granit natural, sa născut în anii '80 ai secolului trecut în Italia, unde poartă totuși numele <грес порчелланато> (gres porcellanato). Dacă traduceți în limba rusă, sunați ca o ceramică de porțelan din porțelan (porcellano - porțelan, gres - piatră - produs ceramic). Trebuie să spun că această frază reflectă foarte precis esența materialului: compoziția este porțelan legată, prin fabricarea de experți pe care îi atribuie gresie tehnologie unică pe bază, cât și proprietățile finale și frumusețea este comparabil cu piatră naturală (și, în multe privințe depășește ). Aplicarea largă a acestui material unic a început în prima jumătate a anilor '80. Și în Rusia, granitul a apărut la începutul anilor 90.
Granitul ceramic are caracteristici tehnice deosebite care o disting mult mai departe printre alte materiale de finisare. În primul rând, acest lucru se realizează printr-o tehnologie neobișnuită de producție. Să ne ocupăm mai mult de ea pentru a descoperi secretul unicității <грес порчелланато>.
Caracteristicile tehnologice ale producției de granit ceramic
Un amestec format din porțelan care constă din ceramică din mai multe soiuri de argile, nisip de cuarț, feldspat și pigmenți, dintre care majoritatea sunt oxid de metal convențional - adică în întregime din ingrediente naturale.
În mod direct, procesul de producție a porțelanului începe deja în cariere, unde se extrag componentele originale. Tipurile de lut utilizate trebuie să aibă o compoziție chimică strict definită. În viitor, aceasta determină în mare măsură proprietățile materialului și comportamentul acestuia în timpul ștanțării și arderii. Argilele intră în fabrică, unde sunt depozitate în containere speciale, fiecare recipient are propriul grad de lut. Apoi, amestecând cu alte componente într-o proporție strict calculată, acestea intră în secțiunea de pre-măcinare la o anumită dimensiune. Toate acestea se întâmplă în fabrici speciale - țevi de diametru mare în formă de con de rotație, partea interioară a căreia are o acoperire specială și este umplute cu morcovi în formă de bilă din stânci foarte solide. procesul de măcinare are loc cu furnizarea de apă, are, prin urmare, mai amestec lichid este introdus în containere speciale, unde să stea timp de câteva ore, în care mai grea parte conținând zameshennye și componentele frezate separate de o, care cuprinde în principal apă brichetă. Procesul de uscare are loc în coloane verticale speciale - așa-numitele atomizoare. Amestecul umed este pulverizat deasupra, iar aerul fierbinte este furnizat de aerul inferior. Fluxul de aer fierbinte se învârte și se usucă amestecul astfel încât, la ieșirea atomizorului, amestecul aproape uscat constă din granule identice cu un diametru de aproximativ 50 microni (0,05 mm).
Această frământare este deja pregătită pentru presare și prăjire, iar caracteristicile de culoare sunt deja introduse în ea, care vor apărea ca rezultat al producției. Este destinat depozitării în silozuri speciale, există aproximativ 80 dintre ele, iar în fiecare dintre ele numai tipul de lot este stocat întotdeauna. Frământarea poate rămâne acolo până când este în cerere pentru o etapă ulterioară.
La comanda calculatorului, în conformitate cu programul de producție al fabricii, materiile prime dintr-un anumit siloz intră în turnul tehnologic-construcție, unde are loc amestecarea finală cu alte tipuri de dozare. Acest amestec determină tipul final de plăci care vor fi produse. Apoi amestecul este introdus în presă în porțiuni definite strict.
Cel mai important lucru
Păstrarea în cuptoare are loc la o temperatură cuprinsă între 1200 și 1300 ° C (cea mai mare valoare care este utilizată numai în industria ceramică), iar această temperatură se realizează în etape. În același timp, sunt finalizate cele mai importante reacții chimice, iar structura plăcii este structurată, ceea ce determină proprietățile unice ale materialului granit ceramic. Amestecul este sinterizat, formând un singur produs omogen. Ca urmare, după răcire, se obține un material foarte poros, vitrificat, neporos, cu o absorbție aproape de zero a umidității și cu dimensiuni aproape ideale.
În prezent, putem distinge următoarele tehnologii speciale pentru producția de articole din ceramică din porțelan:- încărcare dublă (doppio caricamento) - permite primirea pe fiecare placă originală a nuanțelor și divorțurilor nerepetabile;
- microtech (microtech) - frământarea suplimentară la sol permite obținerea unui model de suprafață cu o mare precizie a pieselor;
- trece o venă (un Passante cavă) - ca în marmură naturală, unde modelul (vene de culori diferite) se extinde în mod aleatoriu întreaga grosime, și aici, cu o specială de frământare, se obține același efect.
În centrul său, producția de granit ceramic repetă procesul de producere a pietrei naturale naturale, dar numai într-o formă accelerată. Prin urmare, gresia din porțelan poate fi recomandată ca o alternativă la piatra naturală - mai accesibilă și în același timp cu caracteristici tehnice superioare.
Tehnologia producției de granit ceramic afectează în mod direct proprietățile unice ale acestui material. Și, într-adevăr, are caracteristici excelente de performanță care o deosebesc între alte materiale de finisare.
Proprietățile granitului ceramic.
Poate că cea mai bună calitate a granitului ceramic este porozitatea scăzută și, prin urmare, duritatea fenomenală. Limita forței sale la așa-numita <сосредоточенной нагрузке> 10-20 de ori mai mare decât cea a cimentului sau a betonului armat. Adevărat, acest dale de proprietate uimitoare arată doar dacă este corect așezat! Granitul ceramic are o mare rezistență mecanică în comparație nu numai cu plăcile ceramice, ci și cu piatră naturală.
Rezistența la abraziune
O altă proprietate excelentă a acestui material este rezistența la uzură sau, cu alte cuvinte, rezistența la uzură. Porțelanul din porțelan a crescut rezistența la abraziune. Deoarece culoarea este aceeași pe toată grosimea plăcii, deteriorarea mecanică a suprafeței rămâne invizibilă. Prin urmare, acest material este pur și simplu indispensabil în încăperile cu flux uman intens.
Non-marcare
Mizeria nu pătrunde în pori, deci este mai ușor de îndepărtat. Actualul granit ceramic nu lasa pete de murdarie.
Rezistența la îngheț
Când apa pătrunde în porii plăcii, devine mai fragilă, deoarece apa se îngheață în timpul răcirii, creând o mare tensiune în țiglă. Aceste sarcini, repetate cu fiecare înghețare ulterioară a apei, pot duce la crăpare, apariția de chipsuri caracteristice și la distrugerea completă a stratului de acoperire. avantaj porțelan că valoarea mărimii porilor materialului și gol (rata de absorbție a apei - aproximativ 0,05%, este cea mai mică dintre toate materialele ceramice și chiar mai mică decât cea a oricărei piatră naturală). Această calitate permite utilizarea gresiei din porțelan pentru placarea exterioară a clădirilor în orice zonă climatică.
Refractare și rezistență la foc
Datorită acestei calități, placa poate fi utilizată pentru a face sobe și șemineuri. Rezistența la foc înseamnă că nu arde deloc și, în plus, protejează suprafața confecționată de foc. Și acest material nu emit gaze toxice atunci când este încălzit.
Rezistența la culoare și rezistența chimică
Granitul ceramic nu este sensibil la efectele razelor solare și nu schimbă culoarea în timp. Este, de asemenea, rezistent la acțiunea substanțelor chimice active, acizilor și alcalinelor (se tem doar de acidul fluorhidric).
Proprietăți izolatoare antistatice și electrice
Placile ceramice nu conduc un curent electric si, in consecinta, socul descarcarii de energie electrica statica este absolut exclus.
Apel extern
Clasificarea dalelor din porțelan.
Prin compoziție:
Plăci de porțelan omogene
(altfel - complet colorat) este unul dintre cele mai comune tipuri de granit ceramic, și, probabil, cele mai diverse. Tehnologia producției sale poate fi deja considerată clasică: toată masa plăcii este supusă pigmentării în etapa de pregătire, iar modelul rămâne neschimbat atât la suprafață, cât și la adâncime. Datorită acestui granit omogen poate presupune practic veșnică: operațiune pe termen lung chiar și „uzură“ nu poate deteriora ireversibil suprafața de lucru, deoarece abraziune a stratului superior nu conduce la un model de încălcare.
Porțelan parțial colorat.
În această formă de granit ceramic există de obicei 2 straturi: un strat de substrat și un strat pigmentat. Substratul se face, de obicei, în gama standard de "sare-piper", și numai stratul superior cu o grosime de câțiva milimetri este colorat. Datorită acestui fapt, se economisesc pigmenți care economisesc costurile, iar costul de producție este redus.
Gresie din porțelan.
În exterior, acest tip de granit ceramic este practic imposibil de distins de țiglele obișnuite: același glazură pe substrat. Principala diferență este că baza de rulment a acestei plăci este porțelan și, prin urmare, caracteristicile de performanță ale acestei plăci sunt mult mai mari.
În aparență:
Pe suprafața texturii, porțelanul este neșolat (mat), lustruit, lustruit, satinat (glazurat), structurat, re-certificat, glazurat.
care nu face obiectul unei prelucrări suplimentare, păstrează factura, care a fost achiziționată la ieșirea cuptorului. Suprafața sa nu strălucește, ci se caracterizează printr-o duritate ridicată.
semi-lustruit
și în special lustruit este mai captivant: tratamentul cu materiale abrazive, pe de o parte le oferă o strălucire oglindă, iar pe de altă parte - reduce rezistența la uzură. La fel ca o piatră naturală lustruită, aceste tipuri de granit trebuie tratate în mod regulat cu masticuri speciale, creând un strat suplimentar de protecție.
satin
În producția de plăci de satin pe suprafață înainte de ardere, se aplică un strat de săruri minerale, ca urmare a faptului că materialul obține un luciu special, moale. Structura și caracteristicile sale de performanță rămân aceleași.
Pentru pregătirea matrițelor de porțelan din porțelan structurat sunt folosite matrițe. Materialul finit poate simula textura pietrei, lemnului sau are crestături anti-alunecare.
- procesul de calibrare a mărimii plăcilor după ce este ars, cu alte cuvinte marginea produsului este tăiată cu roți diamante. Astfel de materiale formează o suprafață uniformă, fără sudură, în timpul instalării.
Porțelanul din porțelan glazurat este acoperit cu smalț și ars într-un cuptor. Placile sunt glazurate (smaltuite) daca producatorul cauta sa creeze o imitatie minutioasa de marmura, travertin, lemn, placi ceramice sau decorul luminos, fara a recurge la o scutire scumpe intreaga. În locurile cu mișcare intensă, porțelanul din piatră din sticlă este mai bine să nu se folosească - stratul de glazură se învârte în timp.