0 C. Încălzirea înainte de forjare a metalelor este responsabil de operare, care depinde în mare măsură de calitatea viitoare s doar părți, dar, de asemenea, productivitatea, funcționarea satisfăcătoare a echipamentelor, de viață a sculei și a costurilor de producție.
In timpul procesului de încălzire variază în dimensiunile piesei de prelucrat, starea straturilor de suprafață din metal, structura și proprietățile sale.
Modificarea dimensiunilor preformei. Atunci când este încălzit, metale extins, și când răcirea este comprimat cu o sumă numită contracție. Atunci când forjare forjate din oțel contracție este determinată aproximativ presupunând că acesta este de 1,2% din dimensiunea lingoului în stare fierbinte. De exemplu, lungimea forjare la cald de 500 mm, după răcire la temperatura atelier va avea o lungime de 494 mm. În cazul în care contracția de metal nu ia în considerare, vom obține dimensiunea pieselor forjate căsătorit.
Impactul contracție asupra formei și dimensiunii mai ales a pieselor forjate ia în considerare atunci când forjare eboșe de formă complexă, cu procese lungi, ca și contracție poate duce la colmatare severe piese forjate. De asemenea, este important să se ia în considerare contracția metalului în timpul fabricării de lucru fluxurilor de forjare moare, mai ales atunci când precizie scump forjare aliaje.
Modificări în straturile superficiale ale semifabricatelor. Odată cu creșterea temperaturii activității interacțiunii metalelor cu atmosferă crește cuptor. Când încălzirea oțelurilor pe piesa de suprafață un strat de oxizi de fier (FeO, Fe2 03. Fe3 04), de asemenea, numit scorii. Grosimea scală depinde de temperatura și de disponibilitatea timpului de încălzire a semifabricatelor în cuptor, compoziția gazelor de furnal și compoziția chimică a aliajului. Cel mai intens devine oxidat la o temperatură de peste 900 ° C. Astfel, prin creșterea temperaturii țaglei la 900 până la 1000 ° C, viteza de oxidare este crescut de 2 ori și până la 1.200 ° C - 5 ori.
Formarea scară duce la pierderi de metal crește cotele de prelucrare, reducerea productivității. Mai mult decât atât, la scară, fiind solidă, reduce durabilitatea sculei la prelucrarea și presiunea de procesare.
Încălzirea este însoțită de formarea de oțel carbon scară strat în vrac, care este ușor de îndepărtat, dar nu protejează metalul de oxidare în continuare. În oțeluri aliate cu crom, siliciu, wolfram, nichel, strat de scară este structura foarte subțire, dens, nu crapă și este protejat de oxidare în continuare. oțel CrNi conținând 15 ... 20% nichel, substanțial nu este oxidat și, prin urmare, se numește rezistentă la căldură. La încălzirea oțelurilor carbon și arderea carbonului se produce din stratul de suprafață până la o adâncime de 2 mm. Reducerea conținutului de carbon al BAA numit Zuglo zhivaniem ro conduce la o reducere a rezistenței și durității oțelului și deteriorarea detaliu călire. Decarburare deosebit de dăunătoare pentru dimensiuni mici având piese forjate alocația de prelucrare mici și supuse la rigidizarea ulterioare. Pentru marile piese forjate decarburare mai puțin periculoase, deoarece în timpul forjării și răcirea carbonului din straturile interioare ale preformei diffuses la exterior, cât și compoziția chimică a aliajului este nivelat.
Pentru a reduce formarea de scară și decarburare aplică căldură într-o atmosferă protectoare (aliaj special este încălzit și tratat sub vid), viteza de încălzire, diferite strat de spălare și, aplicată lingoului înainte de încălzire. nu se spală protejează numai metalul de la formarea la scară, decarburare și gaz de saturație, dar, ca lubrifianți, reduce căldura și forța deformatoare a sculei deformante și, de asemenea, să faciliteze curgerea plastică a metalului în timpul tratamentului de presiune.
Cu toate acestea, pentru a proteja pe deplin metalul de oxidare în condiții de producție, prin urmare, nu se pot folosi diferite metode de decojire țagle înainte de ambutisare la cald - prin diverse dispozitive cu perii racloare leu okalinolomate- și hidrotratare din cauza expunerii pe termen scurt la suprafața piesei de prelucrat jeturi de apă sub presiune ridicată .
Distribuția temperaturii pe secțiunea transversală a semifabricatului. Încălzirea secțiunea transversală a piesei de prelucrat se realizează prin transfer de căldură din exterior spre straturile interioare. Cu cât coeficientul de transfer termic al metalului viteza de încălzire mai mare și aria secțiunii transversale a piesei, cu atât mai mare diferența de temperatură dintre straturile exterioare și interioare ale preformei. Sub straturile exterioare la temperaturi ridicate extinde mai interior, prin care tensiunile apar între ele, ceea ce poate duce la distrugerea metalului. Cea mai mare parte a piesei de secțiuni de oțel structurale carbon până la 100 mm și conductivitatea termică datorită metalului ductilitate ridicată „fără frică“ încălzire rapidă, astfel încât acestea să poată pune la rece în cuptor la o temperatură de până la 1300 0 C.
oțeluri Vysokouglerodastye și înalt aliate și multe aliaje complexe având o conductivitate termică scăzută și ductilitate pentru a evita fisurarea necesită încălzire lentă. Eboșe din aceste oțeluri și aliaje se încarcă într-un cuptor având o primă temperatură scăzută pentru ceva timp sa menținut la această temperatură și numai după încălzirea preformelor peste creșterile de secțiuni transversale. După ce straturile exterioare ale preformei încălzite până la temperatura de forjare, preforma este lăsat pentru câtva timp în cuptor pentru egalizarea temperaturii în întreaga secțiune metalică. De data aceasta se numește timp de staționare. lingouri mari din oțeluri aliate prin încălzire se supune multiple expuneri la temperaturi diferite.
Forjarea preforme inegal încălzit este periculos datorită diferit secțiunii sale de deformare metal și posibila fractură acestuia. Prin forjare mor și forjare moare Backer în încălzirea neuniformă duce la fluxul de curentul inferior al ștampilei de lucru și de viață a sculei de jos.
Trebuie amintit că, în procesul de forjare, mai ales la viteze mari de deformare și temperaturi scăzute ale piesei de prelucrat generează căldură să fie distribuit uniform peste volumul semifabricatului.
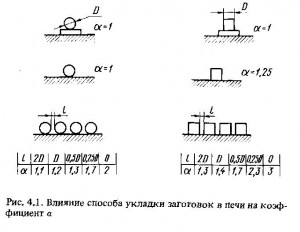
Efectul încălzirii pe o structură metalică conectată cu transformarea alotropică (diferite grilaj cristalin la diferite temperaturi) în glanda. După încălzire peste 723 ° C, din oțel are o rețea cubică cu fețe centrate cu atomi de carbon încorporat - soluție solidă interstițială, numită austenită. Oțel cu structura austenitică au cea mai mare ductilitate.
Modul de încălzire. Selectarea unui mod de încălzire este informat preforme de încălzire de temperatură ales cu intervalul de temperatura de procesare și determinarea timpului de încălzire țaglă. Limita inferioară de forjare interval de temperatură depășește 723 ° C, iar partea de sus ar trebui să fie de la 100 până la 150 ° C sub temperatura de topire. După încălzirea la temperaturi mai ridicate în metal apar două tipuri de defecte - supraîncălzire și epuizare. Dacă supraîncălzirea crește mărimea granulelor scade ductilității metalului și proprietățile sale mecanice se deterioreze. Acest defect poate fi eliminată prin forjare suplimentare sau tratament termic, care necesită costuri suplimentare. Încălzirea la temperaturi mai ridicate (1350. 1400 ° C) duce la epuizare - oxidarea metalelor la limitele granulelor, care rezultă în comunicațiile perturbate între granulele și prăbușirilor de metal forjare. Burnout este căsătoria incorigibil.
Astfel, metalele tratate într-o anumită presiune pentru fiecare interval de temperatură Gn ... Hx. în cazul în care dl și Tc - temperatura, respectiv, la începutul și sfârșitul forjare. Pentru a avea proprietăți mecanice piese forjate mari tind să termine forjare la o temperatură apropiată de Tc. furnizarea unei structuri de granulație fină a metalului. Dacă forjare sau termina forjare la temperaturi mai ridicate în timpul pieselor forjate de cereale de răcire crește dimensiunea și proprietățile mecanice ale oțelului se deterioreze.
Intervalul de tratament de presiune la temperatură depinde de gradul aliajului prelucrat. oțelurile carbon reduse au o lățime (până la 500 ° C), intervalul de temperatură și tratament timp pentru a efectua un număr mare de operații Smith fără încălzire suplimentară a piesei. Cu toate acestea, în ingineria modernă sunt din ce în ce este necesar să se ocupe de aliaje care au un interval de temperatură foarte îngustă de deformare. De exemplu, aliajele de aluminiu VD17, D19 și alte procese necesare în cuprins, între 400 și 470 ° C, respectiv. E. Processing interval de temperatură este de numai 70 ° C, astfel încât, în unele cazuri, necesită o încălzire suplimentară de tagle pentru finalizarea prelucrării acestora.
Atunci când forjare piese forjate mari și complexe, atunci când este nevoie de o lungă perioadă de timp pentru a efectua operația de forjare, piesa se raceste si este nevoie de suplimentare încălzirea acestora. Pentru a reduce numărul acestora din urmă, să ia măsuri pentru a încetini răcirea metalului în timpul forjării. Pentru această utilizare ekrany- reflectoare pliabile 66 din tablă de aluminiu, un capăt al piesei de prelucrat în timpul forjării celălalt capăt închis azbest sau capac special carcasă lingouri de acoperire izolante pe baza unui pahar cu compoziție specială.
Forjarea Temperatura de pornire T este selectat astfel încât podstyvaniya calcul terminată forjare preforme, la o temperatură de 20 .... 30 ° C peste temperatura admisibilă Tc (tabelul 4.1.) Și temperatura de încălzire este stabilit puțin mai mare decât Ti pe bază răcirea semifabricatului în timpul transferului de la dispozitivul de încălzire la ciocan sau apăsați.
Timpul de încălzire se determină pe baza două cerințe contradictorii. Pe de o parte, pentru a reduce formarea de scară și de a crește productivitatea, este de dorit să se reducă timpul de încălzire prin creșterea vitezei acestuia, pe de altă parte, pentru a evita crăparea - pentru a reduce viteza de încălzire și de a crește durata acestuia. Acesta din urmă este valabil mai ales pentru achiziționarea de secțiune transversală mare a aliajelor mari.
Semifabricate din oțeluri carbon, având o arie a secțiunii transversale de 100 mm 2 și prelucrate manual maleabil, permite rata ridicată de încălzire și pot fi încărcate rece în cuptor cu o temperatură de aproximativ 1300 ° C În acest caz, timpul de încălzire poate fi determinată fie de masă. 4.2, sau formula NN Dobrokhotova: T = akd \ fd, unde T - timpul de încălzire, h; k - factor în funcție de gradul de oțel (pentru carbon și oțeluri slab aliate k = 10, pentru oțeluri carbon și de înaltă k = 20); d - diametrul (sau partea pătrată) a semifabricatului, m; o - metodă de contabilizare coeficient pentru stivuire semifabricatelor în cuptor (Figura 4.1.). Mai dens este semifabricatul stivuite în cuptor, mai coeficientul a și mai mare timpul necesar pentru încălzirea semifabricatelor.
4.1. domenii de temperatură forjare oteluri si aliaje de nichel
Semifabricate din oțeluri aliate mari datorită distrugerea eventuala lor este încălzită în două etape: mai întâi, au încălzit lent la 650 C, și apoi, când creșterea ductilității aliaj, în cele din urmă este încălzit până la o temperatură de forjare viteză mare. Timpul total de încălzire T = TH + T2. unde Tx si T2 -, respectiv, în timp ce primul și al doilea încălzirile (T = a = ab, ld Ggde -y ^ d - diametrul
sau o parte țaglă pătrat).
În urma procesului de forjare răcire piese forjate (în special din oțeluri aliate) este un pas responsabil de proces care, atunci când sunt efectuate în mod necorespunzător, poate duce la căsătoria lor. După răcire fisuri de forjare sunt formate în ele mai des decât în timpul încălzirii, astfel încât viteza de răcire nu trebuie să depășească valorile admisibile a pieselor forjate. Forjarea otelurilor carbon mediu pot fi răcite cu aer individual sau în rafturi. piese forjate mari, realizate din oțel aliat se răcește lent, în cuptorul oferind expunere timp de câteva ore sub anumite temperaturi. 68
Ciclul de răcire depinde de compoziția chimică a metalelor și dimensiunile forjate și poate dura mai multe zile.
Clasificare. Prin selectarea și funcționarea dispozitivelor de încălzire corespunzătoare sunt performanță de forjare în mare măsură dependentă și de calitatea pieselor forjate fabricate. Fierărie aplică diferite în construcție și funcționare a dispozitivului de încălzire. La selectarea dispozitivele de încălzire sunt ghidate de diverși factori, cele mai importante sunt caracteristici tehnologice forjare sau ștanțare, compoziția chimică a metalului încălzit, dimensiunile și forma matrițelor, forjare în producție și condițiile de muncă. Dispozitivele de încălzire sunt clasificate în funcție de metoda de încălzire semifabricatele și caracteristici de design care definesc preforme modul de descărcare.
Prin metoda de încălzire aparat de încălzire este împărțit în cuptor și dispozitivul de încălzire electrică (fig. 4.2). În cuptoare încălzite preforme la o temperatură dorită de căldura spațiului de lucru a cuptorului (sursa de căldură este situată în afara semifabricatul) și dispozitive de încălzire electrică de căldură are loc în interiorul piesei. Cuptor, la rândul lor, sunt subdivizate în flăcări și electrice. Spațiul de lucru cuptoarele de ardere este încălzit prin arderea combustibilului (gaz sau ulei) în electric - trecerea unui curent electric prin elementele de rezistență montate în interiorul camerei de încălzire.
Prin caracteristici de proiectare încălzitoare sunt împărțite în dispozitive cu încărcarea și descărcarea pieselor periodice și continue. Prima, numita camera, piesa încărcate și descărcate din dispozitivul de încălzire prin aceeași fereastră, și în procesul de încălzire ele rămân nemișcat. Al doilea tip de dispozitive de încălzire numite instructivă sau bucșe, caracterizat prin aceea că semifabricatele sunt încărcate printr-o mișcare fereastra de încărcare în timpul încălzirii pentru prelucrare și la ieșire prin fereastra de evacuare.
Design mecanizată complex cuptor și un dispozitiv electric de încălzire rentabilă în producția pe scară largă. În producția la scară mică din cauza frecvente procese și comutările schimbările inevitabile ale ritmului de lucru este indicat să se utilizeze cuptorul universal mai puțin sofisticate.
În ciuda că cuptorul electric și dispozitivele de încălzire electrice au mai multe avantaje față de cuptorul de foc, ultimii 70 dintre cele mai des utilizate în producția de forjare, în special în scară mică și individuală. Motivul este că costul și timpul de încălzire în mai mare electrică decât gazul, iar dispozitivul de încălzire electrică este imposibil de utilizat în unitate de producție din cauza lipsei lor de versatilitate.
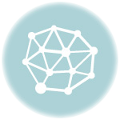
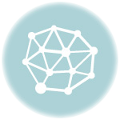
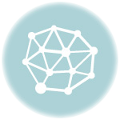
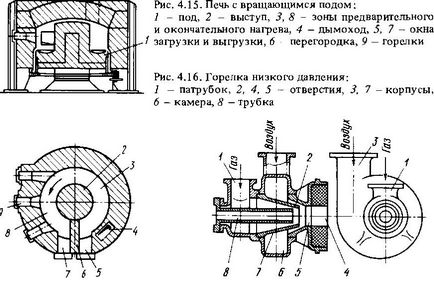