Coroziunea metalelor
Distrugerea materialului sub influența mediului extern se numește coroziune.
Orice design, inclusiv sudat, este expus mediului (aer, apă, gaze de producție, curenți rătăciți). Mediul poate fi agresiv sau ușor agresiv. În primul caz, designul poate servi timp de mai mulți ani sau chiar luni, iar în cel de-al doilea caz, de zeci de ani și chiar de secole.
Coroziunea metalelor poate fi cauzată de procesele chimice și electrochimice. Procesele chimice includ cele care apar în timpul interacțiunii chimice directe între un metal și un mediu agresiv și nu sunt însoțite de un curent. Electrochimice se referă la procesele în care distrugerea metalului este însoțită de apariția unui curent electric (procese în apă, electroliți, gaze umede, săruri topite și alcalii).
Este deosebit de periculos coroziunea intergranulară, caracterizată prin apariția de fisuri. Distrugerea are loc de-a lungul granițelor cristalitelor, ceea ce perturbe legătura dintre ele și conduce la o distrugere neașteptată, deoarece foarte des apariția produsului în timpul coroziunii intercristaline nu se schimbă.
Coroziunea este procesul de distrugere fizică și chimică a metalului sub influența mediului extern. Prin natura procesului se disting coroziunea chimică și electrochimică. În primul caz, procesul de oxidare metalic are loc prin expunerea directă la mediu în contact cu ea fără apariția unui curent electric, iar în al doilea caz, apare coroziunea în electroliți și este însoțit de un curent electric. În funcție de natura corosivă coroziunii electrochimice de mediu poate fi atmosferic, solului, structural (datorită heterogenității metalului în structura), biologice (fluxuri în condiții subterane care implică microorganisme), alcaline, acide, contactul (la intersecția a două metale diferite), coroziunea provocată de curenți rătăciți sau soluții apoase de săruri. Rezistența la coroziune depinde de compoziția chimică, structura, starea suprafeței, starea de stres a metalului, precum și compoziția chimică, concentrația, temperatura și viteza mediului coroziv pe suprafața articolului. O măsură a rezistenței la coroziune a unei rate de metal de coroziune în condițiile date și mediu, care se exprimă prin adâncimea de coroziune, în milimetri pe an, sau de pierdere în greutate în grame per oră per 1 m2 de suprafața metalică.
Coroziunea este distrugerea metalelor datorită interacțiunii cu mediul extern (coroziv). Acest termen vine din cuvântul latin coroziune - corodare. Coroziunea este un flagel teribil de industrie, de construcții, de transport. O parte semnificativă a metalelor produse anual este cheltuită pentru recuperarea pierderilor cauzate de coroziune.
Metalele sunt obținute prin separarea lor de compușii stabili naturali, de exemplu oxizi. În procesul de coroziune, metalul sub influența mediului, tinde din nou să se mute într-un compus mai stabil. În particular, în timpul coroziunii oțelului, se produc adesea oxizi de fier și hidroxizi care au o structură liberă și sunt puțin legați de metalul de bază. În cele din urmă, suprafața secțiunii transversale a produselor scade, iar puterea lor scade. În cele mai severe cazuri, coroziunea afectează produsele și este distrusă.
Gradul de deteriorare a coroziunii a metalelor și a aliajelor depinde în principal de următorii factori: compoziția chimică și structura metalului sau a aliajului, compoziția chimică a mediului extern, temperatura mediului, starea de stres a metalului în structură. Coroziunea este clasificată în funcție de natura geometrică a deteriorării și de natura interacțiunii metalului cu mediul.
În funcție de natura geometrică a deteriorării coroziunii, se distinge o coroziune selectivă continuă, locală, subterană, intercristalină, selectivă. Cu coroziune solidă, metalul este distrus uniform pe întreaga suprafață. Coroziunea locală perturbă integritatea metalului în anumite părți ale suprafeței produsului și se exprimă prin deteriorarea suprafeței prin puncte, pete, ulcere. Coroziunea subterană începe în grosimea metalului. Produsele de astfel de coroziune, în creștere în volum, vin pe suprafața metalului și provoacă distrugerea locală a produsului. Coroziunea intergranulară se desfășoară de-a lungul marginilor granulelor metalului și agravează brusc proprietățile sale mecanice. Coroziunea electromagnetică reduce dizolvarea componentelor structurale individuale ale aliajelor.
Prin natura interacțiunii cu mediul, coroziunea este chimică și electrochimică.
Coroziunea chimică are loc în medii care nu conduc un curent electric, de exemplu, în gaze uscate, lichide organice-ulei, benzină, alcool etc. Cea mai intensă coroziune are loc la temperaturi ridicate. Ca rezultat, se formează o peliculă de oxid pe suprafața pieselor. Filmul dens protejează straturile interioare ale produsului de oxidare. Astfel de filme sunt obținute, în special, în coroziunea aluminiului și cuprului. Un film slab nu protejează metalul de alte daune.
Procesul de oxidare este mărit de influența temperaturii. Astfel, viteza de coroziune a oțelului carbon în gaze cu o temperatură de până la 600 ° C este foarte mică, la o temperatură mai ridicată permeabilitatea filmului de oxid crește brusc. Aceasta mărește grosimea stratului de scală, care, atunci când este lipit de metalul de bază, dispare. Oțelurile aliate permit încălzirea fără oxidare apreciabilă la temperaturi mai ridicate.
Coroziunea electrochimică apare în soluții apoase de electroliți - săruri, acizi, alcalii. Aceasta este cea mai comună formă de coroziune. Structurile metalice structurale, care lucrează în cea mai mare parte în aer umed, sunt supuse coroziunii în principal electrochimice, care este îmbunătățită cu concentrații crescătoare de dioxid de carbon și dioxid de sulf în aer. Structurile cu coroziune intensă situate în pământ, cum ar fi conductele.
În cazul coroziunii electrochimice, unii dintre atomii din rețeaua cristalină a metalului sau aliajului trec în soluția de electrolit sub formă de ioni. Cantitatea echivalentă de electroni rămâne în metal. Ca rezultat, metalul este încărcat negativ, iar soluția de electrolit din jurul acestuia este pozitivă. Există o pereche galvanică în care particulele metalului descompun trec treptat în soluție.
Procesul de coroziune electrochimică depinde de tipul de metal. Dacă tânăr galvanic este format din două metale, metalul se dizolvă, stând în picioare la dreapta în electrochimică seria de aur, argint, cupru, plumb, staniu, nichel, fier, crom, zinc, mangan, titan, aluminiu, magneziu. Astfel, la contactul fierului cu zinc, zincul este dizolvat, iar fierul cu cuprul este fier. Într-o pereche metal-nemetalică, metalul se dizolvă în electrolit.
Perechile galvanice apar, de asemenea, între cele mai mici granule de aliaje, dacă diferă în ceea ce privește compoziția chimică și proprietățile fizice. În special, ferita și cementitul din oțel formează o pereche galvanică, în care anodul va fi ferită, catod - cementită. Prin urmare, în procesul de coroziune ferită se dizolvă (Figura 14).
Coroziunea electrochimică a oțelului în mediu alcalin este încetinită semnificativ. Această circumstanță este utilizată la fabricarea betonului armat. În timpul întăririi majorității cimenturilor, apare un mediu alcalin care promovează formarea unui film de protecție pe suprafața armăturii din oțel din compușii de fier insolubili, cum ar fi Fe (OH) 3. Există așa-numita pasivare a fierului. Filmul protejează metalul împotriva coroziunii. Prin urmare, în structurile din beton armat situate în aer cu o umiditate relativă de cel mult 60%, nu există coroziune a armăturii. Cu umiditatea din ce în ce mai mare a mediului, probabilitatea de coroziune a armăturii din oțel crește. Prin urmare, îndeplinește cerința obligatorie - de a proteja în construirea unui strat de beton dense grosime de 15. 40 mm, ușor permeabil pentru vaporii de apă. În medii extrem de agresive, se aplică măsuri suplimentare pentru protejarea structurilor de armare din oțel.
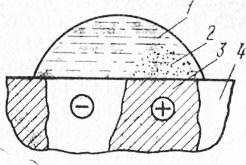
Fig. 14. Schema de coroziune electrochimică a oțelului:
1 - apă, 2 - produse de coroziune, 3 - ferită, 4 - ciment
Protecția împotriva coroziunii este o măsură constructivă și preventivă, care mărește rezistența la coroziune a metalelor, izolarea suprafeței lor din mediul înconjurător, protecția protectorului.
Măsurile constructive și preventive constau în îmbunătățirea calității tratamentului de suprafață al produselor metalice, precum și în protejarea structurilor împotriva precipitațiilor atmosferice. În detaliile responsabile, recurg la suprafețe de lustruire. Aceasta reduce suprafața reală a metalului în contact cu mediul. În plus, de pe suprafețele lustruite, umiditatea curge mai repede. Pentru a preveni coroziunea, mașinile și mecanismele scumpe sunt protejate cu lubrifianți de protecție.
O creștere a rezistenței la coroziune este realizată prin introducerea în compoziția oțel a aditivilor de aliere - crom, nichel, mangan, titan, cupru. Foarte rezistent la aliajul din oțel inoxidabil cu coroziune atmosferică, care conține o cantitate mare de crom, care creează un film de oxid dens pe suprafața produselor. Acest film trece prin oțel. Utilizate în construcția oțelurilor cu carbon și aliaturi slab aliate sunt uneori realizate prin adăugarea de cupru de 0,2 ... 0,5%, ceea ce mărește rezistența la coroziune de 1,5 ... 3 ori.
Izolarea suprafeței metalice din mediul înconjurător este cea mai obișnuită metodă de protejare a structurilor clădirilor prin utilizarea de acoperiri sau prin obținerea unui film de protecție pe suprafața metalică.
Acoperirile nemetalice formează un film de protecție pe suprafața produselor, care împiedică pătrunderea umezelii. Acest lucru previne posibilitatea coroziunii.
Acoperirile nemetalice includ în principal lacuri și vopsele. Utilizați lacuri sintetice bituminoase, gudronate, precum și vopsele de ulei, alchidice și alte emailuri. Articole sanitare - băi, chiuvete, chiuvete - protejați cu emailuri anorganice. Pentru a face acest lucru, un strat subțire dintr-un amestec constând din cuarț, feldspat, argilă și borax se aplică pe suprafață. În procesul de ardere la o temperatură de 750 ... 800 ° C, se formează o topitură de silicat, acoperind uniform suprafața articolului. Emaila rezultată se distinge prin rezistența ridicată, duritatea și rezistența la coroziune. Adesea, acoperirile protectoare sunt fabricate din polimeri - polietilenă, clorură de polivinil, polistiren, rășini epoxidice. Suprafețele componentelor încorporate ale structurilor din beton armat prefabricate sunt protejate cu acoperiri de ciment-poli-stiren sau ciment-perclorovinil.
Acoperirile metalice sunt obținute prin aplicarea unei pelicule subțiri de alt metal pe suprafața produsului. Se disting acoperirile anodice și catodice. Straturile de acoperire cu anod sunt realizate din metal în picioare într-un șir de solicitări din partea dreaptă a metalului protejat. Pentru produsele din oțel, protecția anodică este un film de zinc, aluminiu. Dacă stratul de acoperire este rupt, atunci stratul de acoperire, mai degrabă decât metalul de bază, este distrus. Acoperirile de zinc și aluminiu sunt adesea folosite pentru a proteja suprafața pieselor încorporate în structurile prefabricate din beton armat.
Acoperirile catodice protejează metalul de contactul direct cu mediile corozive. Protecția catodică este realizată din staniu, plumb, nichel. O astfel de protecție este operabilă până când se deteriorează integritatea stratului de acoperire. Dacă filmul de protecție este deteriorat local, începe coroziunea oțelului.
Filmele de protecție sunt formate prin prelucrarea intenționată a pieselor cu reactivi chimici speciali. După acest tratament, compușii cu rezistență ridicată la coroziune se formează pe suprafața metalului. Filmele de protecție sunt create, de exemplu, prin oxidare, tratând părțile într-o soluție apoasă fierbinte de oxidanți puternici - hidroxid de sodiu, nitrat și peroxid de mangan. Un film dens și puternic de culoare neagră pe suprafața oțelului, constând în principal din oxid de fier magnetic, protejează metalul împotriva oxidării ulterioare. Uneori recurge la fosfatarea oțelului, procesând produse cu soluții de acid fosforic și sărurile sale. Pelicula gri rezultată protejează în mod fiabil metalul de coroziune atât în aer cât și în apă proaspătă.
Protecția protectorului constă în combinarea metalului structurii protejate cu metalul care se află în partea dreaptă a liniei de tensiune.
În perechea galvanică formată în acest fel, metalul benzii de rulare servește ca un anod. Se va rupe treptat, iar metalul de bază va rămâne intact. Această metodă este utilizată pentru a proteja structurile din apa de mare, solurile umede. Structurile de oțel ale poliilor de alimentare cu energie electrică, rețeaua electrică de contact, conductele sunt alimentate cu protectori sub formă de plăci de zinc, aluminiu-zinc sau aliaje de magneziu.