Tipuri de blănuri moderne și aplicarea lor
Majoritatea producătorilor de instrumente de tăiere optimizează geometria și proprietățile instrumentului pentru materialele prelucrate specifice. În domeniul fabricării matrițelor de injecție, acest tip de oțel P20, CPMV 10 și metale pulverulente. Este foarte important să alegeți geometria potrivită și clasa de rezistență a sculei în funcție de materialul specific care este prelucrat, pentru a evita uzura prematură sau ruperea sculei. În plus, conformitatea instrumentului și a materialului prelucrat mărește productivitatea și predictibilitatea procesului de prelucrare, ceea ce reduce numărul de înlocuiri ale sculelor, defecțiuni și reparații.
Când se prelucrează materiale cu o duritate de 52 de unități Rockwell sau mai moale, un instrument comun de carbură de un scop general se ocupă destul de bine. Când duritate mai mare a materialului trebuie să fie utilizat un instrument specializat dezvoltat pentru tratarea materialelor solide, de exemplu, freze din carbură, cu o geometrie optimizată a piesei de tăiere și diverse acoperiri, cum ar fi nitrura de titan și aluminiu. În plus față de această acoperire, fiecare producător își dezvoltă propriile tipuri de acoperiri pentru un instrument din carbură solidă. Cutterele cu inserții de carbură interschimbabile cu geometrie optimizată și cu un strat specializat pentru tratarea materialelor dure vor face față celor mai multe materiale pulverulente cu duritate ridicată. În plus, diferite tipuri de inserții de tăiere și freze cu diferite tipuri de discuri de așchiere și caneluri disponibile pentru vânzare permit optimizarea prelucrării materialelor solide utilizate la fabricarea matrițelor de injecție.
După ce ați decis tipul de unealtă de tăiere, trebuie să selectați raza de curbură a colțurilor suprafețelor de tăiere. Raza de rotunjire trebuie să fie mai mică decât raza internă de curbură a elementelor matriței de fabricat. Dacă raza este egală cu raza de curbură a colțurilor formei, poate exista o așa-numită "oprire tare" - gustare. Un instrument cu o rază mai mică va pur și simplu trece ușor prin rotunjire. Pentru finisare, recomandăm utilizarea de tăietori de carbură solidă cu diametre mici sau mașini specializate de tăiat cu carbură solidă pentru prelucrări de mare viteză.
Același principiu al selecției de raze funcționează și pentru operațiile de ascuțire - folosind o unealtă cu rază mai mică decât raza curburii elementelor de formă. Și, în ciuda faptului că în colțurile piesei de prelucrat sunt mai multe materiale nereparate, acest principiu permite menținerea unei încărcări constante și uniforme a sculei în toate etapele, de la prelucrare la finisare.
Nu mai puțin importantă este rigiditatea instrumentului. Conurile și alte elemente ale morii joacă un rol semnificativ în acordarea unei anumite rigidități sculei. Designul celor mai multe mori este conic sau pas cu pas. Când tranziția structurii în trepte de la porțiunea de lucru pentru etapa de măcinare gambei este realizată la structura con - tranziția este netedă, diametrul părții de tăiere a tăietor crește treptat la diametrul gambei. Cele mai multe mori alungite au un design conic.
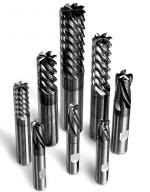
unghi mai mare de conicitate conferă rigiditate instrument suplimentar, cu toate acestea formă de proiectare impune restricții asupra acestui parametru, t. K. Mismatch are loc la contactul dintre dispozitivul de tăiere și suprafața trailing a pereților semifabricatului. Prin urmare, este necesar să se utilizeze un instrument cu unghiul maxim de admisie, dar fără a depăși unghiurile de înclinare ale formei de formă. De exemplu, dacă designul de formă oferă un unghi de înclinare a tuturor pereților de 3 grade, cea mai bună alegere este să utilizați un instrument cu conic de 2,5 grade.
Răcire și lubrifiere
În ceea ce privește lubrifierea și răcirea, funcționarea optimă a celor mai multe mori din cele mai recente modele se realizează într-un mod uscat. O excepție este utilizarea răcirii constante cu ceață de ulei. La prelucrarea materialelor cu duritate crescuta, lubrifiere si racire nu sunt folosite, cu exceptia cetei de ulei.
deținătorii
Majoritatea producătorilor de scule de tăiere a metalului recomandă utilizarea amortizoarelor de vibrații pentru a lucra cu modele moderne de freze. Chiar și cel mai bun instrument dintr-un cartuș mediocor nu va fi capabil să obțină performanțe optime și nu va trece la durata de viață dorită, în timp ce cele mai noi modele de cartușe pot chiar să dubleze durata de viață. Amortizarea vibrațiilor este de o importanță excepțională, în special atunci când lucrați cu un instrument lung, cu viteză mare de alimentare și frezare aspră. Principiul amortizoarelor de vibrații, în general, este acela că în elementele lor de proiectare sunt plasate, nu corespund armonicile vibrațiilor apărute în timpul procesului de tăiere.
Traiectoria și programarea
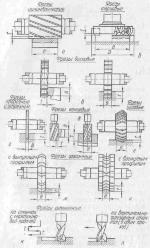
Calea tăietorului de frezat în timpul fabricării matrițelor este optimizată programabil pentru a evita sarcini critice pe scula de tăiere sau pentru a prezenta cerințe nerealiste. De exemplu, pentru fabricarea unghiului de eșantionare se realizează în mod programatic formează traiectoria mișcării netezită, eliminând viraje ascuțite, ceea ce creează o suprafață de contact mare a dinților de tăiat și piesa de prelucrat, rezultând într-o sarcină critică, care ar putea deteriora unealta. În mod normal, un arc este programat cu o rază mai mare decât raza sculei. Deci, dacă utilizați o freză de 20 de milimetri, programul ar trebui să se deplaseze scula de-a lungul traseului cu o rază de curbură de cel puțin 20 de milimetri, dar se recomandă să utilizați raze mai mari.
Programare astfel de arce netede poate fi uneori o sarcină trivială, deoarece, în cazul unei erori ar putea duce la guljanie margini din cauza diferitelor tipuri de tundere fenomene de preluare sau de lovituri de tăiere. Pachetele software moderne vă permit să programați cu exactitate traiectoriile netezite. În plus, un ajutor bun este disponibilitatea unui programator calificat, care înțelege principiul interacțiunii sculelor, pregătirea și utilizarea arcurilor netezite. Cheia aici este mișcarea continuă, non-stop a instrumentului. În cazul în care tăietorul se rotește fără alimentare, de exemplu, atunci când schimbați direcția de mișcare, căldura rezultată poate deteriora grav tăierea
Alegem mașina pentru ascuțirea tăietorilor
Pregătirea pentru operarea tuturor tipurilor de freze este echilibrarea, ascuțirea și poziționarea în mașină.
Echilibrarea tăietorului. Există două tipuri de echilibrare - statice și dinamice. Freza de tăiere, de obicei, se echilibrează static, adică fără a roti tăietorul de frezat la o viteză de lucru. Dezechilibrul cuțitului de frezat montat pe dorn este arătat pe paralele prismatice ale dispozitivului de echilibrare (diametrul maxim al morii este de 400 mm); Partea mai grea a tăietorului este în partea de jos. Verificarea se face de 3 ori. Cantitatea de dezechilibru (dezechilibru) este stabilită prin atașarea la partea ușoară a greutăților frezei de frezat (de exemplu, bucăți de plastilină). După ce sa realizat echilibrul, greutățile sunt cântărite. Produsul de masă suplimentară de raza atașamentului său dă magnitudinea dezechilibrului (r-cm). Pentru mori cu diametrul de 120. 180 mm, dezechilibrul este permis până la 3,5 g-cm. Măcinarea tăiată prin îndepărtarea (șlefuirea, forarea) a metalului din partea greuă a acestuia în zona nefuncțională.
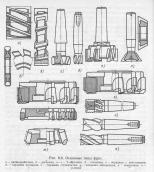
Dinamica echilibrată se realizează pe mașini speciale. Permite echilibrarea nu numai a forțelor, ci și a momentelor cu acuratețe ridicată (dezechilibru rezidual nu mai mare de 1 g / cm). Acest lucru este deosebit de important pentru instrumentele care au o lungime mare.
Ascuțirea morii. La ascuțire, trebuie menținut profilul de prelucrare, unghiurile de tăiere și egalitatea razei aceluiași dinți. Lamele conice integrale și compacte sunt ascuțite de-a lungul feței frontale, păstrând în același timp valoarea unghiului frontal y (vezi figura 2a). Pentru aceasta, axa frezei trebuie să fie decalată față de planul de lucru al roții de șlefuire cu o distanță H1 = Rsin, unde R este raza frezei.
Tăietoarele solid și compuse dintr-o singură bucată (cu o spate dreaptă a dinților) sunt ascuțite pe partea din față și din spate. Fața frontală este ascuțită în același mod ca și marginea anterioară a tăietoarelor plane. Ascuțirea marginii posterioare ar trebui să garanteze că colțul posterior a rămâne neschimbat. Pentru a face acest lucru, cu discul de șlefuire a paharului (vezi figura 2, c), dintele tăierii de frezat ar trebui să fie fixată de vârful de sub axa sa cu valoarea H2 = Rsin.
În absența unei canule, un cerc ascuțit poate fi ascuțit cu un diametru mare (a se vedea figura 2, d). Apoi, axa cercului cu raza Rk trebuie localizată deasupra axei morii la o distanță de H3-Rsin.
Precizia și calitatea preparării morii trebuie să îndeplinească cerințele stabilite de standarde. Sunt permise următoarele deviații limită ale parametrilor morii:
Rulare radială a dinților, mm 0,05 / -
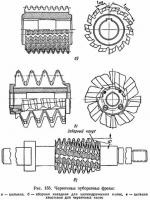
Baterea pe față a suprafețelor laterale ale dinților, mm 0,04 / -
Îndoire longitudinală, mm - / 0,05
Abateri ale unghiurilor de tăiere efective ale conturului de la nominal, °, pentru lamele: fața - / 0,05
Abateri ale unghiurilor de strunjire laterală înclinată și oblică atunci când se întoarce de la o valoare nominală de ± 0,5 /
Rugozitatea frontului, spatelui și suprafețelor laterale ale dinților Ra, micron 1,25 / 1,25
Mori de sfârșit. Ascutit. Selectarea modurilor de frezare.
De multe ori, în prelucrarea lemnului sau plastic, se pune întrebarea: dacă duritatea tăietor este mult mai mare decât detaliile materialului, de ce moara capăt ascuțit, este ideea nu ar trebui să boante.
Cu toate acestea, în viața de zi cu zi nu ne gândim la ce ai nevoie de un cuțit ascuțit, după masa de tăiere alimente foarte moi, cum ar fi pâinea sau cârnați. Ascuțirea apare destul de des, uneori de mai multe ori pe lună. Și de câte ori ascuți un cuțit?
În același timp, toată lumea știe de mult timp că un cuțit ascuțit va tăia și un cuțit va fi zdrobit și zdrobit. Același lucru este valabil și pentru tăietoarele de frezat.
Ce materiale au o duritate suficientă pentru fabricarea morilor? De exemplu, din oțel carbon sau de mare viteză, deoarece duritatea lor este aproximativ aceeași (62-65 HRC au carbon, 62-67HRC la viteză mare). Un aliaj tare este de asemenea potrivit, deoarece aliajul dur are o duritate chiar mai mare.
Dar, pe lângă duritate, există și alte câteva caracteristici care limitează utilizarea anumitor materiale. De exemplu, morile de capăt din oțel carbon nu. Sa constatat că, la o temperatură mai mare de 170 de grade, începe eliberarea oțelului. În același timp, duritatea cade rapid. În oțelul de mare viteză, temperatura critică începe de la 490-540 grade, pentru un aliaj dur cu mai mult de 900-920 grade. Prin urmare, mori de capăt de carbură au o rezistență mai mare. În știință, acest fenomen se numește "rezistență roșie".
Cea mai clară unealtă are cel mai mic unghi de ascuțire posibil. Cu toate acestea, aceasta reduce puterea instrumentului. După cum se spune, "briciul este ascuțit, dar sabia nu este sora". De îndată ce marginea de taiere a instrumentului, așezat, patch-ul de contact devine mai puternic crește temperatura în zona de lucru, uzura instrument apare mai repede temperatura crește și mai mult.
În practică, prelucrarea diferitelor materiale (lemn de frezat, chiar și lemn de esență tare, din plastic) încercați, dacă este posibil, pentru a alege unghiul drept ascutit frezei.
Cele mai vizibile rezultate pot fi obținute prin alegerea corectă a tehnologiei de procesare a pieselor. În acest caz:
1. Timpul total de prelucrare al piesei este redus.
2. Îmbunătățește rugozitatea suprafeței.
3. Extinde durata de viață a morii.
4. Încărcarea echipamentelor (ghidaje, șuruburi cu bilă, ax) este redusă și, în consecință, durata lor de viață.
A. Când se macină cu o moară finală:
1. Alegeți diametrul maxim posibil al morii de capăt, puterea determinată a axului și rigiditatea mașinii.
2. Selectați modurile de tăiere, ținând cont de rezistența mecanică a sculei. Modurile excesive pot duce la defectarea instrumentului de tăiere.
3. Selectați corect configurația miezului final. Amintiți-vă că canelura dintelui tăietorului trebuie să fie mai mare decât stratul materialului care este îndepărtat. Rândurile trebuie să se potrivească în canelură și să fie evacuate liber din zona de tăiere. În caz contrar, chips-uri înfundate în canalul tăietor și instrumentul va împinge elementul, nu taie (A se vedea. Hârtia și modurile de control al cip de tăiere).
4. Dacă sunteți pe un material fragil (plastic, lemn: stejar, fag, tei, mesteacan, etc), amintiți-vă că condițiile excesive de tăiere poate duce la ciobire sau chiar întreruperea completă a piesei de prelucrat.
5. În plus, vă rugăm să rețineți că condițiile de tăiere sunt determinate de calitatea pieselor de prindere pe masa mașinii și dispozitivul de tăiere în mandrina mașinii, care este o grămadă de „masa mașină-snap-detaliu-cutter-holder-mașină.“ Bad clemă duce la sistemul de vibrații și de ieșire a frezei în jos înainte de timp, căsătorie sau accident.
B. Pentru finisarea cu o moara de capat:
1. Utilizați tăietoare ascuțite de înaltă calitate pentru a obține o rugozitate mai bună a suprafeței.
2. Pentru a obține precizia necesară a prelucrării piesei de prelucrat, acordați atenție toleranțelor diametrului fabricilor utilizate.
3. Amintiți-vă, de asemenea, despre rigiditatea sistemului "Mașină-mașină-rigidizare-detaliu-frezat-mașină-chuck-machine". Rigiditatea insuficientă a sistemului poate duce la strângerea frezei și a piesei.
În prezent, GOST prevăd prezența a cinci soiuri de placaj, care diferă în principal în prezența și numărul de defecte de prelucrare permise [1].
clasa E (elite). Defectele nu sunt permise, cu excepția modificărilor minore ale caracterului aleator în structura lemnului;
clasa I. Lungimea maximă a fracturii sau fisurilor pentru placajul din clasa I nu trebuie să depășească 20 mm;
Cum se poate utiliza placajul în gospodărie?
În prezent, GOST prevăd prezența a cinci soiuri de placaj, care diferă în principal în prezența și numărul de defecte de prelucrare permise [1].