Din moment ce acest material este pentru amatori, este necesar să se spună despre unele etape ale producției de porțelan, care sunt foarte cunoscute de profesioniști, dar rămân în afara oricărui alt popor. Mulți colectori și vânzători de produse din porțelan nu au fost niciodată produși și nu au cunoștințele necesare.
Cele mai frecvente întrebări mi-au dat ocazia să înțeleg că, în general, oamenii nu au ocazii de a obține răspunsuri simple care nu necesită imersiune în complexitatea tehnologică.
Întrebarea cea mai obișnuită: De ce sunt produsele din porțelan în interior?
Desigur, întrebarea se referă la sculpturi și vase. Există produse plate care sunt realizate prin turnare sau presare și nu au cavități interioare.
Există procese care sunt mai bine de arătat decât să explice. În primul rând recomand să vizionați un mic film despre producția de porțelan:
Masa cremoasă lichidă (alunecare din porțelan) este turnată pentru o anumită perioadă de timp într-o matriță de ghips. Ghipsul absoarbe umezeala, formând o cremă a produsului. De îndată ce grosimea șarjei devine suficientă, golul rămas în formă se revarsă prin orificiul de scurgere. Grosimea pereților produsului, în funcție de volumul său, poate fi de 3 mm. până la 8 mm.
Porțelanul, în procesul de fabricație, are o contracție a aerului și a focului, adică diminuat proporțional cu 14-16% din modelul original. (Foto).
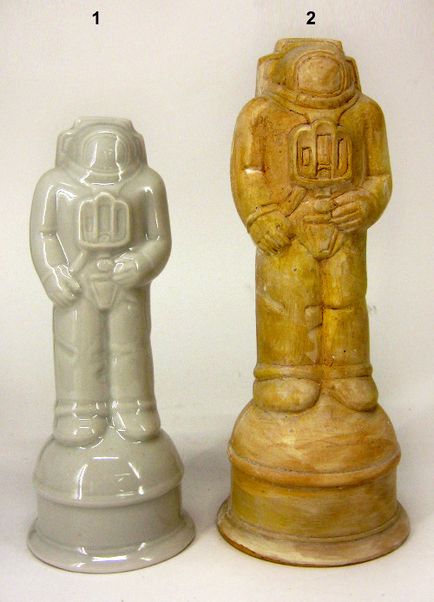
Temperatura arderii porțelanului ars este de 1350-1410 grade. Procentul de contracție depinde de temperatura finală. În cuptoarele cu cameră, temperatura poate fi diferită în funcție de locația cuptorului. În consecință, contracția va fi diferită. Contracția depinde de grosimea pereților (crock) a produsului. Cu cât zidul este mai gros, cu atât mai mult contracția. Dacă produsul este turnat pereți prea groase și au o grosime a peretelui neuniformă, ardere când se udă se poate produce deformarea suprafeței. Produsul prea subțire este chiar mai deformat în cazul unei prăjiri lustruite. Cele mai multe porțelan căsătorie după care se manifestă udate de ardere: muște, glazura pleshiny pori (prostuplenie mat ciob, în consecință glazura grosime neuniformă), bule etc., și glazura de asamblare Trebuie spus că procentul de respingeri după ardere arsă poate ajunge la 50% la o rată de 15%.
În producția pe scară largă, pregătirea alunecării este controlată de tehnologi de la CPL. Densitatea alunecării este de 1,72 g pe 1 centimetru cubi. Densitatea este măsurată prin hipermetru. Densitatea glazurii este de 1,28 g. Glazul este crescut într-un recipient mare, pentru a putea fi complet înmuiat complet. Când se usucă, se pot forma picături și picături, care sunt îndepărtate cu atenție din produs prin intermediul pâslei. Pentru a pregăti produsul pentru viteza de ardere, fundul este complet curățat de glazură și spălat cu un burete umed. În cuptor, produsul este plasat pe plăci carborundum acoperite cu caolin. Caolin protejează produsul de lipirea pe placă în timpul procesului de ardere.
Prima ardere se efectuează la o temperatură de până la 900 de grade pentru a asigura prăjina și geamurile ulterioare.
Procesele care au loc în timpul porțelanului de ardere sunt descrise în detaliu în literatură. După ardere în cuptoare electrice există o creștere progresivă a temperaturii, care este afișat pe dispozitivele de control și eventual testate cu ajutorul unor conuri ceramice, care au o temperatură de topire predeterminată. Conul cu o anumită etichetă de temperatură este topit și atinge partea superioară a bazei atunci când se atinge temperatura dorită. Politic, produsele de porțelan de ardere sunt cel mai bine realizate în cuptoarele cu gaz, unde puteți obține cea mai mare albă a porțelanului. În cuptorul cu gaz există încă o schimbare a modurilor prin reglarea alimentării cu aer și gaz. Posibila ardere porțelan viteză în care produsul bine uscat poate fi încălzit până la 900 de grade pe oră, într-un mediu oxidant puternic cu creșterea ofertei de aer. Cu arderea rapidă, începutul perioadei de recuperare corespunde unei temperaturi de 1000 de grade, la sfârșitul a 1200 de grade (creșterea fluxului de gaz). Creșterea suplimentară a temperaturii are loc cu un mediu redus. În mod tipic, pentru fiecare cuptor de gaz, se efectuează o schemă optimă de ardere cu indicatorii prescrise de gaz și de presiune a aerului. Arzătoarele cu experiență determină temperatura în cuptor în funcție de culoarea flacării. Când se atinge temperatura dorită, se face o expunere timp de 15 minute pentru a egaliza temperatura în întregul volum al cuptorului, după care alimentarea cu gaz este oprită. Apoi cuptorul este răcit cu purjare de aer. De la 1350 la 900 de grade, este posibilă răcirea rapidă. În plus, este mai bine să se efectueze o răcire naturală, în care cuptorul este mai puțin distrus.
Pentru acei cititori care doresc mai multe detalii cu privire la tehnologia de ardere, am da un citat din manualul: „ardere Politi poate fi împărțită în mai multe perioade, fiecare dintre care are loc la anumite temperaturi și atmosferă controlată, care asigură formarea treptată a oală cu proprietățile necesare.
Prima perioadă de porțelan de ardere (20-950 ° C), se caracterizează prin diferite reacții fizico-chimice, în funcție de produsele cu precondiționarea adăpate calcinare și uscarea produselor după geamurilor. Pregătirea preliminară depinde de gradul de prăjire și este determinată de prezența produselor gazoase în compoziția produsului.
Mai întâi, apa reziduală legată mecanic și higroscopic este îndepărtată. Ambele tipuri de apă se evaporă la o temperatură de 110-130 ° C.
După încălzirea produselor din porțelan, are loc o creștere mai accentuată a temperaturii. În acest interval de temperatură are loc deshidratarea finală a substanței de lut și îndepărtarea completă a apei hidratate legată chimic, dacă acest proces nu a fost finalizat la prima ardere. Cele mai active perechi de apă hidratată sunt eliberate în intervalul de temperatură de 500-600 ° C.
Deoarece porțelanul are o porozitate suficient de mare la aceste temperaturi, eliberarea rapidă a umidității în această perioadă nu duce la crăparea produselor. Mediul de gaz al cuptorului nu afectează îndepărtarea apei hidratate.
Aproximativ de la o temperatură de 200 până la 500 ° C, produsele sunt absorbite (adsorbite) de negru de fum din gazele de ardere în timpul prăjirii. Peste 700 ° C începe arderea treptată, care este mai activă în mediul de oxidare. În același timp, se efectuează sublimarea substanțelor organice conținute în materialele de lut, care este însoțită și de carburizarea șarpelui. Pentru a reduce carburizarea produsului în acest interval de temperatură, atmosfera de oxidare (a = 2-4) este menținută.
Nu arsă la atingerea 1000 ° C carbon ca reziduuri care nu sunt îndepărtate de umiditate, în etapele ulterioare de sinterizare contribuie la formarea vezicule în „pete“ formă care rezultă din închiderea fazei lichide, care începe să se formeze la o temperatură de 950 ° C, o porțiune de capilare din ciob calcinată .
Nu ars în vârful ciobul perioada de recuperare de carbon adsorbit poate provoca defecte în perioadele ulterioare din porțelan de ardere, în special în perioada inițială de răcire, deoarece, după o perioadă de recuperare, atunci când raportul dintre CO: CO2 devine mai mică de 0,1, este posibil să se formeze bulele de gaz de ardere, cauzand apariția pe unghiile de porțelan și depresiunile cuțite.
Materialele organice precum și carbon și adsorbit, trebuie îndepărtat complet din partea de sus a perioadei de recuperare a ciob oxidant brusc atmosfera cu un exces de oxigen (aproximativ 4-6%), deoarece la temperaturi de peste 1050 ° C calcinare este deja realizată într-o atmosferă reducătoare .
Nevoia de ardere a materiei organice la o temperatură de 950 ° C, se datorează faptului că la această temperatură porțelan are o porozitate suficient de ridicată (permeabilitate), facilitând gazele de ieșire fără obstacole care sunt formate în timpul arderii substanțelor organice. Durata arderii substanțelor organice din porțelan depinde de grosimea și conținutul de oxigen său precum cuștile de volum.
În această perioadă (la o temperatură de 575 ° C) a reacției de conversie are loc calcinarea? -kvartsa in? -kvarts, care este însoțită de o creștere a volumului de produse care, cu toate acestea, nu provoacă apariția defectelor. Aceasta se datorează prezenței unui număr mare de pori în masa porțelanului încălzit. În plus, atunci când se extind în straturile superficiale ale articolului, există forțe compresive cu care materialul rezistă bine.
La temperatura de 1000 ° C, decarbonizarea (descompunerea termică) a carbonatului de magneziu MgCO3 și CaCO3 de calciu prezentă în masa porțelanului se termină. Carbonatul de magneziu MgCO3 începe să se descompună la o temperatură de 650 ° C, iar carbonatul de calciu CaCO3 - la 920 ° C
La temperaturi relativ scăzute, materialul are o permeabilitate la gaze chiar mai mare, ceea ce facilitează eliberarea nestingherită a dioxidului de carbon CO2 produs în timpul descompunerii carbonaților.
A doua perioadă de ardere are loc la o temperatură de 950 până la 1050 ° C într-un mediu puternic de oxidare. Pe parcursul acestei perioade, cu excepția reacției este decarbonatarea completă și conversie - -kvarts în loc arderea intensivă de carbon în ciob eliberarea completă a materialului din reziduurile de apă de hidratare precum oxidarea compușilor de fier.
Încălzirea produselor în a doua perioadă de ardere este aproape izotermică, ceea ce ajută la egalizarea câmpului de temperatură în volumul cuștii produsului.
A treia perioadă de frigere este regenerativă. Perioada de recuperare este creată prin creșterea concentrației de CO în produsele de combustie a combustibilului în intervalul de temperatură 1050-1250 ° C. Monoxidul de carbon CO recuperează oxid de fier Fe2O3 la oxid de FeO și sulfat de calciu CaSO4 și Na2SO4 de sodiu - sulfit pentru sulfurat și care previne ciob flambaj și contribuie la efectul de „albire“ porțelan. În plus, FeO favorizează formarea fazei vitroase (lichide), extinde intervalul de sinterizare. Faza sticlos, la rândul său, contribuie la intensitatea reacției mullitoobrazovaniya (mulitul - componenta principală a porțelanului fazei cristaline).
Reacțiile de reducere a oxidului de fier Fe2O3 la FeO se efectuează conform următoarelor scheme:
3Fe2O3 + CO = 2Fe3O4 + CO2
Fe3O4 + CO = 3FeO + C02
O2 + 2CO = 2CO2
2FeO + Si02 = 2FeO • Si02
Creșterea temperaturii în timpul acestei perioade de ardere și concentrația de CO accelerează reacția, dar prea intens sau prea târziu (la temperatură) în timpul ratei de recuperare a formării fazei sticloase poate depăși reacțiile de reducere a vitezei și gazele nu a găsi ieșire ciob, cauza formarea în ea de blistere. Faza sticloasă este formată, în principal, în intervalul de temperaturi 1150-1170 ° C, deși o cantitate mică de ea se formează la o temperatură de 950-1000 ° C Într-o masă de porțelan conține alte componente, emit gaze atunci când sunt încălzite, cu toate acestea, aceste gaze trebuie să fie eliminate pentru a atinge o temperatură de 1170 ° C, adică. E. Înainte de topire feldspat, porțelan are o alta atunci când permeabilitatea la gaz suficient.
Reacțiile de reducere a sulfatului de calciu CaS04 și a Na2S04 de sodiu se desfășoară conform următoarelor scheme:
CaSO4 + CO = CaS03 + CO2
CaS03 + CO = CaO + S02 + CO2
Na2S04 + CO = Na2S03 + C02
Na2S03 + CO = Na20 + S02 + C02
Dacă mediul reducător în timpul acestei perioade este înlocuit cu unul oxidant, descompunerea sulfatului se va termina la temperaturi care depășesc punctul de topire al feldspătului, ceea ce va conduce, de asemenea, la formarea de blistere. Mediul de reducere reduce în mod semnificativ temperatura de evacuare a gazelor componentelor masei, ceea ce contribuie la producerea unui vas fără defecte (fără umflare).
În produsele de ardere, CO poate fi conținut într-o cantitate de 3 până la 8%, în funcție de tipul de cuptor. Creșterea conținutului de CO este nedorită, deoarece în acest caz, produsele de ardere formează negru de fum, care precipită pe produse. Odată cu arderea ulterioară, pot apărea defecte ale glazurilor - nuburi.
Durata perioadei de recuperare este determinată în principal de grosimea și forma produselor arse.
Intervalul de temperatură analizat 1050-1250 ° C este însoțit de o contracție intensă a masei. În acest caz, capilarele și porii din șarpe se închid treptat, iar difuzia gazelor se stinge. Cea mai intensă contracție are loc în intervalul de temperatură 1000-1200 ° C. Cea mai mare contracție corespunde celei mai mari compactări a shard-ului.
A patra perioadă de ardere (1250-1410 ° C) - sinterizarea porțelanului - are loc într-un mediu neutru.
Pe parcursul acestei perioade, extinderea continuă aluminosilicați conținute în masa ceramică, asupra oxizilor de disponibilitate cu formarea ulterioară a mulitul (3A12O3 • 2SiO2) și fără dioxid de siliciu; formarea fazelor vitroase și cristaline este finalizată; există o sinterizare a porțelanului, în care se obține proprietățile fizice și mecanice de bază, precum și rezistența chimică.
Această perioadă se execută de la temperatura de 1250 ° C până la temperatura finală de sinterizare, mărimea care depinde de compoziția masei de porțelan poate varia de la 1280 (porțelan moale) până la 1410 ° C (porțelan tare). Pentru a obține microstructura dorită caracterizat printr-o porozitate închisă de la 2 până la 4%, temperatura optimă de calcinare este stabilită la 20-50 ° C peste temperatura maximă de etanșare. Creșterea temperaturii deasupra optimului va cauza o arsură a porțelanului, la care albitatea scade, porozitatea crește, iar puterea produselor scade.
A patra perioadă de coacere se termină prin menținerea la temperatura maximă a timpului necesar pentru a finaliza reacțiile de sinterizare, precum și o distribuție mai uniformă a fazei cristaline în faza vitroasă. Durata expunerii depinde de volumul produselor arse. Expunerea excesivă provoacă arsuri. Absența umidificării la o creștere rapidă a temperaturii de la 1250 ° C la maxim creează un curent subteran de produse.
Cea de-a cincea perioadă de ardere este o răcire puternică. La răcirea porțelanului, punctul de tranziție al fazei vitrece de la starea elastică topită în stare solidă și punctul de întărire a glazurii este de o mare importanță.
Temperatura trecerii la stare solidă corespunde punctului de întărire al glazurii pe porțelan. În portelanele solide, acest punct este de aproximativ 700 ° C, pentru glazuri din portelan moale de 550 ° C. Pentru a evita solicitările termice între șarpe și glazură, se recomandă reducerea vitezei de răcire în aceste intervale de temperatură. În caz contrar, poate apărea fisurarea capacului glazurii. Răcirea extrem de lentă poate duce la pierderea strălucirii glazurii datorită cristalizării sale.
În stadiul inițial de răcire (1410-1000 ° C) asupra produselor din porțelan pot exista două tipuri de defecte: stingerea pe suprafață și glazura glazurii. În cazul oxidării fierului rezultă galbenele: 4FeO + O2 = 2Fe2O3. Oxidul de fier Fe2O3 dă o nuanță galbenă pe suprafața produselor. Deși nuanța galbenă nu agravează celelalte proprietăți ale porțelanului, în același timp, aspectul produsului se deteriorează. Stralucirea poate fi eliminată prin arderea repetată efectuată în modul normal. Glazul este matzat datorită cristalizării sale.
Cu răcire rapidă 1410-1000 ° C în aer (oxidant) mediu datorită intensității ridicate a etapei inițiale de răcire și cristalizare FeO oxidare glazura devine imposibilă, prin care ciob menține albului și luciu luciu.
A șasea perioadă de ardere este răcire. Cu o răcire suplimentară în intervalul de temperatură de 1000-700 ° C, faza lichidă se întărește în cele din urmă și portelanul trece de la o stare vâscoasă la o fază fragilă. În această perioadă, produsul produce solicitări termice și mecanice. Tensiunile termice, care se datorează diferenței de temperatură în timpul perioadei elastice, dispar după ce temperatura este egalizată pe grosimea articolelor, astfel încât acestea sunt numite temporare. Acumulările termice pot duce la distrugerea produselor în timpul răcirii. Când faza lichidă se solidifică, în articol apar solicitări mecanice datorită contracției inegale a masei de-a lungul grosimii acesteia. Astfel de stresuri pot duce, de asemenea, la distrugerea produselor atât în procesul de răcire, cât și în consumator. Prin urmare, solicitările mecanice sunt numite solicitări reziduale.
Timpul și tensiunile reziduale depind de rata de răcire a produselor în această perioadă. Rata de răcire permisă depinde de proprietățile materialului, dimensiunile și forma produselor, precum și de volumul cuștii. Pentru a reduce solicitările ambelor tipuri, rata de răcire în această perioadă este oarecum redusă. Rata de reducere a temperaturii este determinată de rezistența termică a articolelor și a armei de foc. "