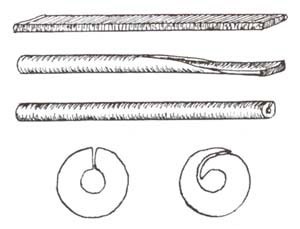
tub baril pas de pliere simplă.
Deasupra - Placă-martor pentru portbagaj
Probabil, mulți oameni vor fi de acord cu mine că partea principală a unui pistol - butoaie. La urma urmei, ei trage. Eficacitatea de fotografii tun cauzat în dorința unei persoane de a face un pic de „manual“ arma. O astfel de armă în mijlocul secolului trecut a găsit într-un castel în Tanneberg Hessene (Germania). Ea a fost aruncat la sfârșitul secolului al XIV-lea. Trage-le din ea cu mâna a fost, desigur, greu și incomod, și în curând adaptat caseta arbaleta. Sa dovedit faptul că precizia de fotografiere și de precizie a unor noi arme în mod serios inferioare unui arc bun, cu toate că energia și, prin urmare, forța de pumn, aceasta depășește în mod semnificativ. Destul de repede a devenit clar că, odată cu creșterea lungimii butoiului, focurile de armă devin mai precise. Din acest moment începe istoria armelor de foc.
Astăzi „basculare“ nostru o pușcă de vânătoare, există trei părți principale: țeava (sau butoaie care formează unitatea de butoi), bloc, cutie.
Trunchiul dă direcția de zbor a glonțului sau împușcat. Corect și cu atenție este făcută, cu atât mai bine împușcat grohotișul și precizie mai mare.
Se blochează blocul pelviana trunchiuri tăiate element de legătură este între trunchiuri și cuibăresc în arma și absoarbe în principal element de absorbție a forței de recul. Pantoful de blocare montare, mecanisme de declanșare și de siguranță.
Schema de obținere a tuburilor baril răsucite
Lodge oferă posibilitatea de direcționare a armelor, cu scopul și efectul de înmuiere naturală a forțelor de recul din cauza conversiei sale parțiale a cuplului.
Înainte de a vorbi despre tehnologia actuală tunurilor de fabricație, vreau să prezint cititorilor într-o parte a istoriei armelor pe excelență în producția de această parte esențială a armei. La urma urmei, pentru a produce un butoi bun - o sarcină destul de dificilă, chiar și cu nivelul actual de dezvoltare a ingineriei mecanice. Cu toate acestea, perseverenta, diligență și ingeniozitatea strămoșilor noștri sunt diverse soluții la această problemă. Iar calitatea celor mai bune produse din secolul al XVIII-lea a profesioniștilor de astăzi pare a fi aproape misterios. Vrem să-ți spun cât de maeștri din trecut au creat o armă minunat pentru a arăta unele dintre probe sale și să se gândească împreună despre măreția spiritului lor, cu speranța că va întări și propria noastră.
În 1811, Henry Anshyutts (de la bine-cunoscutele arme dinastiei) a publicat o carte despre fabrica de arme din Suhl. El scrie despre cele patru tipuri de tehnologii pentru producerea de tuburi baril :. Normal, răsucite, rana, și trunchiurile „Damasc“
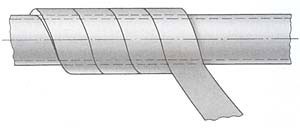
Principiul trunchiurilor plăgilor
Normal (simplu) trunchi preparat din lungimea prebenzii de 32 inch (812,8 mm), o lățime de 4 inci (101,6 mm), de 3/8 inch grosime (9.525 mm). După încălzirea metoda de forjare a fost pliat benzi pe mandrină astfel încât marginile sale longitudinale sunt adiacente unul la celălalt capăt la capăt, paralel cu axa găurii. Aceste suduri comune metoda de forjare și cu atenție prokovyvalsya. Există indicii de netăgăduit că ambele părți lungi ale semifabricatului dreptunghiulare, uneori, au fost conduse „în cap“ și nu sudate cap la cap și se suprapun. După sudare și răcire Ceca au fost matura tetraedrică, un strung pentru a se pisa o suprafață exterioară care este apoi șlefuită manual pe un mare cerc cu diametrul de gresie moale de 1,75 m. Cu partea pelviană este înșurubat în țeava unui capac cu filet, care este, de asemenea, uneori, se fierbe. Desigur, „înecat“ toate trunchiurile dulnozaryadnyh arme, indiferent de tehnologia de producție a acestora.
trunchi Twisted. Sudură într-un trunchi convențional, poziționată paralel cu axa tijei, de multe ori a fost un loc de distrugere a armei. Pentru a evita acest lucru, butoi simplu fiert a început reîncălzit în centru și de-a lungul axei răsucită de-a lungul întregii lungimi, astfel încât sudură avea o formă elicoidală. Această tehnică a făcut cusătura este mult mai puțin încărcată cu alice.
baril plagilor a fost preparat prin înfășurarea treptat benzi de oțel pe mandrină sub forma unei tije sau tub. Elicoidală secvențial sudură prokovyvali baros.
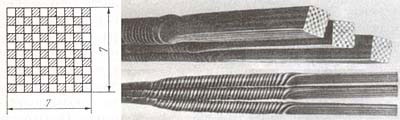
Schema de obținere a benzii de oțel Damasc
Dezvoltarea rapidă a industriei de la sfârșitul secolului al XIX a dus la apariția unor oțeluri carbon cu proprietăți mecanice ridicate. Perspectivele de utilizare a acestora pentru fabricarea trunchiurilor părea evidente. Cu toate acestea, chiar și în primul trimestru al secolului XX, multe armurierii Europa a continuat butoaie pentru „procesul Damaschin“. Astăzi, trebuie să se înțeleagă că aceste arme, deși acestea sunt monumente fantastice due armurierilor generațiile anterioare, dar încă inferior tuturor indicatorilor majori din oțeluri aliate moderne barreled. Amintim compatrioții noștri că 50A de oțel și chiar 50RA din care și în Tula, Izhevsk și trunchiuri face astăzi, nu se aplică în cazul barreled oțeluri aliate. Și despre butoaie Damasc. O sută de ani sau mai mult după producția este foarte probabil ca elemente de sudare forja se pot deteriora în mod semnificativ și puterea de trunchi pot fi insuficiente pentru a asigura siguranța la foc. Fii foarte atent, dacă doriți pentru a trage un pistol cu vechile butoaie Damasc.
Introducerea crom oțel carbon, vanadiu, nichel, siliciu, mangan și alte elemente au condus la o creștere semnificativă în cele mai importante proprietăți ale oțelurilor baril - elasticitate, rezistenta la rupere, duritatea suprafeței, rezistența la coroziune. Mai mult decât atât, aceste tehnologii fac posibilă pentru a începe cu proprietăți predeterminate. Toate acestea este posibil să se procedeze la producția de semifabricate omogene pentru butoaie de arma. Acest proces a început în ultima treime a secolului al XIX-lea, și aproape o jumătate de secol coexistat cu tehnologie „damasc“.
Dezvoltarea de fabricație butoaie tehnologii arma.
Alinierea semifabricatului receptorului
O nouă etapă începe cu respingerea butoaie fabricate din benzi, iar trecerea la trunchiuri, canalul care a format găurire adâncă. Aceasta tehnologie este mult mai productivă, dar a fost nevoie pentru a rezolva o serie de probleme grave, spune-ne despre unde vrem să-l pună în aplicare, cititorilor moderni să-și imagineze ceea ce prețul obținut un pistol, are o luptă remarcabilă. Nou proces de fabricație preforme baril începe cu forjare, care nu numai că dă forma exterioară a piesei baril se apropie de butoi finit, dar oferă, de asemenea structură îmbunătățită de oțel prin reducerea granularitatea acesteia. De obicei piesa tăiată pieselor forjate din bare rotunde cu un diametru de aproximativ 50 mm. Lungimea semifabricatului depinde de lungimea trunchiului viitorului. Bucata de 320 mm, suficient de lung pentru a trage din țagla de forjare 750 mm în lungime, cu un diametru mediu de 30 mm. Desigur, după forjare diametrului preforme în regiunea camerei este mult mai mare decât cea a botului. Trebuie remarcat faptul că, în forjare convențională aproximativ 15% din oțelul merge la scară. Fierari spun că metalul „ugorayu“.
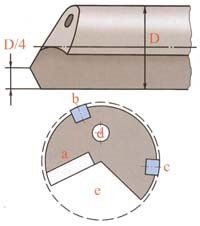
Gun de foraj:
și - Insert,
b și c - șine,
d - un canal de alimentare
lichid de răcire
e - cavitate
cip
Pentru a diminua tensiunile interne din piesele de forjă sunt încălzite la (aproximativ) 850-860 grade și se menține timp de o jumătate de oră. Parametrii de încălzire precise depind de marca si grosimea de otel, receptor. Sarcina a elibera tensiunile interne este foarte importantă pentru toate etapele de producție trunchiuri. Este deosebit de important să se evite tensiunile din tubul terminat receptor destinat să formeze o unitate de butoi de două sau mai multe butoaie. Faptul că lipiri moi și mai ales solide de lipit necesită o încălzire semnificativă și asimetrică a trunchiurilor. Și răcirea are loc neuniform cositorite bloc. Prezența rezultatelor de tensiuni interne într-o deformare trunchiurile vizibile după lipire. În plus, încălzirea puternică a suprafeței interioare a cilindrului în timpul arderii, mai ales intensiv, poate provoca deformarea permanentă a cilindrului în cazul în care acesta a rămas tensiune. După normalizare pentru a stinge. Esența ei constă în obținerea proprietăți optime datorită formării structurii metalice subțiri. Orice oțel este dificilă în ceea ce privește sistemul de fază cuprinzând cel puțin două modificări cristaline de fier pur, carbură de fier, carburi metalice, impurități și soluții solide ale unora dintre aceste componente una față de alta. Tratamentul de temperatură schimbă starea de fază a acestui sistem complex și mărimea fazelor individuale, care este un efect semnificativ asupra proprietăților de performanță. Calirea este uniforma piesele de încălzire la un oțel de formulare dependentă de temperatură care este făcută. Prefabricați de Ck oțel 65, care în Germania este adesea folosit pentru trunchi incalzit la 840 de grade. După aceea, este imersat în ulei având o temperatură a camerei. Apoi, piesa este „eliberat“, pentru care este încălzit într-un cuptor cu retortă la aproximativ 4 ore la o temperatură de 580-600 grade. Un astfel de tratament termic complicat poate afecta semnificativ duritatea, rezistența, elasticitatea și rezistența la tracțiune.
tratat termic țaglă cu atenție Richt. Acest lucru se face pentru foraj care se produce în timpul rotației piesei, nu vibreze. piesa de prelucrat Richt într-o poziție orizontală în timpul rotației, ajustând rolele sale forma presoare. După ce piesa de prelucrat rihtovaniya este din nou supus la încălzire pentru detensionare, apoi cap la cap pe ambele părți și netezite.
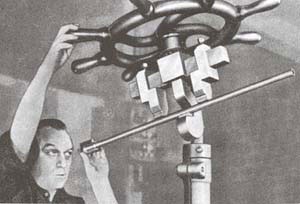
Îndreptarea trunchiul de inele de umbră
utilizând o presă cu șurub
După aceea, se trece la procesele cele mai delicate în fabricarea țevii - găurire. foraj de găurire adâncă, mai ales în piesa de prelucrat lung, cu o stabilitate longitudinală scăzută - un cântec special. În cazul în brațe pentru că folosesc instrumente speciale, cum ar fi strunguri. Asociau piesa de prelucrat se rotește, și un exercițiu de construcții se mișcă înainte. In acest proces, două probleme majore: retragerea axei de foraj a piesei de prelucrat și eliminarea chips-uri. Prima problemă poate fi rezolvată datorită omogenitatea structurii semifabricatului și viteza de avans relativ scăzută și viteza de tăiere a burghiului pentru a evita vibrațiile piesei. Desigur, aceste limitări crește durata de foraj. Problema îndepărtării cip, care este, uneori, nu numai că strică suprafața canalului, dar, de asemenea, burghiu blocat, se realizează prin tehnici speciale. În secolul al XIX-lea a folosit „burghie pușcă“, construcția ei au fost aproape de matura, adică, ele se bazează a avut un bar pe toată lungimea de lucru a sectorului cilindric care a fost selectat, cu un unghi de aproximativ 100 de grade. Design de foraj este destul de simplu și bine înțeles de desen. Printr-o mică gaură în corpul de foraj în zona de tăiere a servit emulsie de răcire, care este o canelură paralelă cu axa burghiului, poartă cu ea jetoanele rezultate. Astfel de mașini au devenit mult timp multi-ax și destul de automatizat. Acest lucru permite unui singur lucrător pentru a controla foraj pe mai multe mașini. Acest proces încă nu garantează un grad ridicat de finisaj al suprafeței alezajului. Chips a fost de multe ori principalul motiv pentru acest lucru. În plus, rata de găurire a fost scăzută.
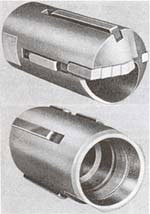
Baysnera de foraj -
de lucru
partea din spate
În 1937, Manfred Burgsmüller a schimbat calitativ schema de foraj. El a sugerat că poziția verticală a pieselor și a napravle¬nie de foraj de jos în sus pentru o mai bună îndepărtare a cip. Drept bază se aplică țevi de foraj pe un cap de lucru care sunt atașate trei plăci de ghidaj și sudate una de tăiere. procesul de tăiere are loc în timpul răcirii cu aer comprimat, care este alimentat în spațiul dintre suprafața și peretele găurii de foraj generat. Chips de același lucru nu este în contact cu peretele găurii și, împreună cu aerul purtat în jos. Semnificativ mai mare moment de torsiune de rezistență, care posedă o „țeavă“, în comparație cu tija de formă, de asemenea, face posibilă obținerea unor suprafețe bune utilizate pentru găurire viteză de tăiere mai mare și furaje.
În 1942 Baysner perfecționat această metodă. El a revenit poziția orizontală instalație de foraj, a propus utilizarea uleiului ca agent de răcire și capul de foraj îmbunătățit. Uleiul a fost alimentat sub presiune în spațiul format între burghiului și suprafața cilindrică și transportă așchiile printr-un canal central în volumul special. suprafață foarte netedă este obținută într-o anumită măsură, din cauza ghiduri de lustruire. Cu toate acestea, după găurire alezajul este prelucrat prin scanarea.
Înainte de procesare la suprafața exterioară a acestuia baril Richt: este verificată axa canalului și, dacă este necesar, rectitudinea îndreptați-o cu ajutorul unei prese cu șurub. Verificați corectitudinea canalului este realizată în inelele de umbră, fiecare vânător se poate face. Dar procesul de editare, nu numai că necesită o viziune bună, dar, de asemenea, un sentiment de metal mare, care vine doar cu experiență. Faptul că cilindrul are o elasticitate. Prin urmare, în cazul în care este îndreptată sub sarcină, apoi, după îndepărtarea acesteia se întoarce parțial la starea sa inițială. maestru cu experiență se simte, cum trunchiul trebuie să „cot“, astfel încât, după îndepărtarea sarcinii a fost perfect corect.
gât Groove pentru lunetele:
1 - Centru 2 - alunecare manșon,
3 - Arm 4 - gât pentru timpan
După formarea butoiului se ridică o altă sarcină dificilă: de cotitură trunchi mânerul exterior. În acest caz, principala dificultate la suprafața exterioară a centrului a coincis exact cu centrul butoiului canalului. Dacă nu, atunci variația tubului receptor, la rândul său. Mai mult decât atât, datorită valorii mari a raportului dintre lungimea baril la diametrul cilindrului în timpul suprafeței de cotitură este necesar să se stabilească două lunete, fiecare dintre acestea trebuie să fie pre-prelucrate gât. Pentru a efectua corect această operație în mijlocul lungimii baril stabili un ambreiaj special care permite dreptul de a deține țeava suprafața brută a canelurii atunci când gâturile pentru lunete. Atunci când gâtul prelucrat, cuplarea poate fi îndepărtată și de a efectua rotirea cilindrului exterior al copiatorului. Aceste strunguri de tratament poate provoca o anumită deformare a cilindrului. Prin urmare, butoiul din nou monitorizate pentru inelele de umbră și Richt, dacă este necesar. Finish măcinare și lustruire se realizează după un gât proshlifovyvayutsya separat pentru lunetele. Etapa finală a tuburilor baril de producție - șlefuirea fină, numit în cazul armelor de honuire.
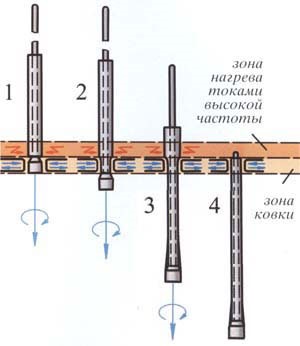
De conducere forjare rotativ:
1 - încălzirea curenților de înaltă frecvență,
2 - start forjare, 3 - procesul de forjare,
4 - se încheie forjare
progrese semnificative în fabricarea tunurilor este mandrină de forjare. Desigur, echipamentul pentru acest proces nu este ieftin. Prin urmare, țeava de turnare forjare profitabil numai pentru volume mari de producție. Cu toate acestea, costul și timpul se pare prea mult. La fabricarea de arbori rotativi cu blank de forjare la cald folosind 260-280 mm lungime și aproximativ 35 mm în diametru. Acesta fora Baysnera face o gaură cu diametrul de 20,5 prin mm. Piesei de prelucrat fixat pe mandrină întărită, foarte lustruite având forma suprafeței interioare a cilindrului finit. După încălzirea preforme de inducție electrică la o temperatură dorită, este alimentat în zona de forjare, în cazul în care acesta se rotește de-a lungul axei sale se extinde transversal sub sunt situate ciocanele de impact. Timp de cincisprezece minute preforme ia forma cilindrului exterior și interior cu camera cartușului. Calirea după o astfel de forjare nu se realizează. Forma exterioară a cilindrului este reglată strung de măcinare și măcinare. gaura este deplasată de scanare aspră. procesare finală a găurii, alezajul incluzând o cameră și contracție se efectuează după asamblarea unității baril.
Chiar mai avansată metodă de fabricare a baril este de forjare la rece pe un dorn. Unul dintre avantajele sale este că se economisește aproximativ 15% din receptor de oțel scumpe, datând din nou pe scară în timpul forjării la cald. În plus, suprafața interioară a cilindrului se obține o copie exactă a mandrinei, astfel încât să puteți obține trunchiurile complet gata (compartimentate, Choke feliere). Suprafața alezajului necesită doar lustruire. Pe lângă structura baril holodnokovanogo asigură un proprietăți mecanice ridicate. Cu toate acestea, ciocane de forjare la rece necesită o durată mai puternic și mai mult. Acesta durează doar peste trei minute. Forma exterioară este reglată șlefuire și lustruire. Validarea axei canalului se realizează și după tehnologia și, dacă este necesar, Richt. Etapa finală de fabricare este singurul butoi de fotografiere eboșe și marcare.