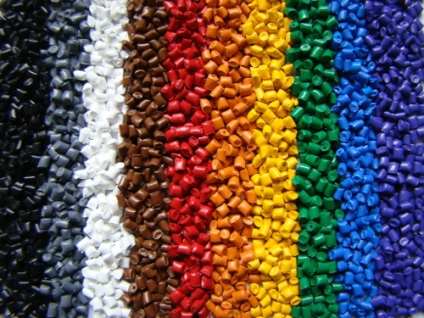
Pe lângă concentrate pure, Masterbatch posibilă utilizarea polimerilor multifuncționale. Acești coloranți și aditivi în combinație au avantajul că, cu controlul nuanței, sub rezerva doza prescrisă, există asigurarea că aditivul conține cantitatea dorită de colorant.
Masterbatch în cataloagele noastre
Astăzi, compania Global Colors este unul dintre cei mai importanti producatori de preamestec din România și Europa. Puteti vedea catalogul produselor companiei noastre.
Masterbatch pentru ajustarea coeficientului de frecare a produselor de film
1. masterbatch antiaderență pentru polimeri
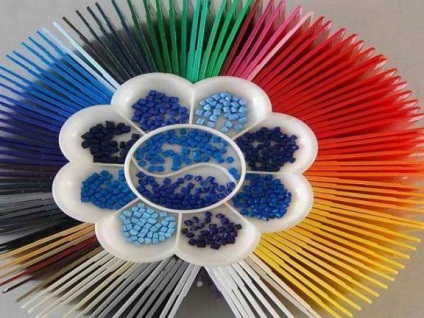
Când adăugați antiaderență microroughness apar, care reduc suprafața de contact a filmului, și astfel - și adezivității. În plus, utilizarea de antiaderență îmbunătățește calitatea sudurii, fixarea și aplicarea de imprimare. Conceput pentru filme de 10 microni grosime. Materiale: LDPE, HDPE, PP. Dozare - 1-2%.
2. masterbatch glisante pentru polimer (masterbatch)
Material clasic pentru a reduce coeficientul de frecare (alunecare (slip) efect) filmelor de poliolefine, destinate pentru ambalarea granulară și materiale lichide. Dacă filmul necesită sudură sau imprimare, se recomandă utilizarea unui aditiv combinat. Este, de asemenea, utilizat ca un ajutor de prelucrare în cazul pieselor turnate cu pereți subțiri pentru a îmbunătăți materialul vărsat.
Materiale: LDPE, HDPE, PP. Dozare - 1-2%.
3. masterbatch combinate (Masterbatch).
Un sistem echilibrat, care asigură un nivel ridicat de anti-blocare și diapozitive. Aditivii sunt utilizate pentru reglarea proprietăților unui film de polietilenă utilizată pentru ambalarea produselor lactate. Îmbunătățirea calității și puterea manșonului sudurilor de polietilenă. Reducerea coeficientului de frecare al filmului pe film, filmul a echipamentului. Consolidarea luciu și strălucire a filmului. grosimea filmului - 10 micrometri. Este, de asemenea, utilizat ca un ajutor de prelucrare în cazul pieselor turnate cu pereți subțiri pentru a îmbunătăți materialul vărsat.
Materiale: LDPE, HDPE, PP. Dozare - 1-2%.
Masterbatch pentru a disipa electricitatea statică
4. masterbatch anti-static.
Una dintre proprietățile prin care materialele polimerice datorează dezvoltării lor și introducerea rapidă a tehnicii, sunt caracteristici electrice foarte bune. Pe de altă parte, ca urmare a rezistenței de suprafață asociate - la 1017 ohmi - pe suprafața materialului polimeric are loc încărcării electrostatice. Astfel de taxe creează diverse probleme:
- Poate provoca descărcări electrice în procesul de fabricație. Asociată cu această scânteie poate aprinde gazele inflamabile, praf sau lichide.
- Există probleme în prelucrarea filmelor polimerice, fibre, benzi, t. K. O sarcină statică duce la faptul că filmul nu poate, de exemplu, să fie cuplate sau separate ca de obicei.
- Ambalare sau bunuri de consum își pierd rapid apel la consumatori, din cauza atracției de praf cauzate de taxa. Din cauza acestui efect negativ este semnificativ redusă de succes de vânzări, în special în domeniul cosmetic (flacoane sampoanele, gelurile de duș și t. D.).
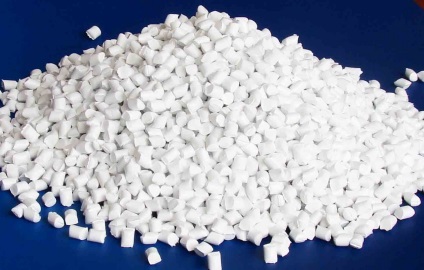
Cele mai frecvente agenți antistatici constau din părți hidrofobe (vlagoottalkivayuschey) hidrofil (iubitoare de apă) și. Ca urmare a migrării la suprafața porțiunii hidrofobe asigură legarea în materialul polimeric, spre deosebire de o porțiune hidrofilă care leagă umiditatea din aer și, astfel, devierile de tensiune. Prin urmare, o umiditate a aerului suficient de mare este esențială pentru eficacitatea agenților antistatici. efect antistatic maxim este atins la 3-6 zile după fabricare.
Depozitarea pe termen lung și impropriu concentrat antistatic higroscopic poate duce la absorbția umezelii. În astfel de cazuri, se recomandă să se usuce înainte de a procesa preamestec. Agenții antistatici au un efect de lubrifiere, din cauza care scade viscozitatea topiturii și adâncitură turnate parte facilitată din matriță. La o temperatură prea ridicată de procesare a majorității substanțelor se evaporă și efect antistatic imediat se deteriorează. În cele mai multe cazuri, a redus sudabilitate și caracterul adecvat al produsului finit pentru a imprima. În acest caz, utilizați anti-blocare aditiv sau transformări ulterioare speciale, de exemplu, prin descărcare corona.
Procentul de AE23 intrare depinde de efectul antistatic dorit; de obicei 1-2% JCGP suficient. Atunci când este administrat într-o peliculă de LDPE de 30 microni grosime de AE23 într-o cantitate de 2% din timpul de descărcare este de 0,01 secunde. t. e. o descărcare imediată. Pentru filme cu alți indicatori, se recomandă să se verifice efectul anti-static asupra companiei de client.
Aplicabilitate în filmele în contact cu produsele alimentare: se supune doza maxima - 4%.
dozare standard - 1,0-2,0% în greutate.
Masterbatch pentru îmbunătățirea calității produselor de reciclare
5. procesare (extrudare) aditivi.
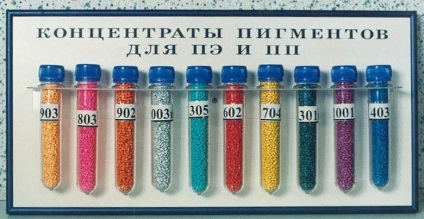
Aplicarea în masă a ajutoarelor de extrudare pe bază de fluoropolimeri a început cu introducerea extrudarea pelicule din polietilenă lineară (LLDPE). Principalele argumente pentru utilizarea polietilenei cresc plante de productivitate de extrudare și îmbunătățirea proprietăților mecanice, comparativ cu LDPE. Cu toate acestea, în procesarea LLDPE în instalațiile standard pentru prelucrarea LDPE în același timp crescând productivitatea defectelor de suprafață a avut loc. Această fractură de topitură (cu alte cuvinte - „piele de rechin“) a fost motivul pentru care fluoroelastomeri au fost folosite mai mult și încă folosit.
Principala cauză a acestui efect este că polietilenă topită are o bună aderență la metale. Acest lucru duce la regiunea exterioară a ambreiajului topiturii din pereții extruderului. La ieșirea din filierelor topitura trebuie să aibă aceeași viteză pe întreaga suprafață. În funcție de materialul și diferențele de viteză, ceea ce poate duce la ruperea straturile exterioare. O astfel de daune apare în suprafața stratului sub formă de „piele de rechin“.
Deoarece fluoropolimeri au o asemănare mai mare la metal decât polietilenă, format din strat (comparabil cu strat de teflon), pe partea interioară a extruderului și matriță. Efectul acestui strat este faptul că topitura de polimer nu mai este în contact cu metalul, ceea ce reduce diferența de viteză în indicele de topire și, la rândul său, se evită formarea de fractură a topiturii și crește productivitatea instalației în ansamblu.
Aplicarea JCGP POAR11-001 vă permite să:
1. Pentru extrudare:
- asigura uniformitatea controlului și geometriei produselor debitului;
- îmbunătățirea calității și luciul suprafeței (eliminarea efectului „piele de rechin“);
- reduce sarcina pe ax, care va asigura creșterea performanțelor și consum redus de energie permite temperaturi de procesare mai mică;
- elimina penetrarea metalului (lipirea) face pe margini;
- reduce timpul de retenție a materialelor în extruder, care va permite schimbarea rapidă a culorilor și a materialelor;
- reciclați la liniile clasice de extrudare (nici o alterare și modificare) din polietilenă lineară (până la 100% în compozițiile).
turnare prin injecție 2.:
- îmbunătăți luciu de suprafață;
- îmbunătăți materialul de poziționare preaplin;
- îmbunătăți îndepărtarea produselor din matrițe (care elimină nevoia de lubrifianți);
- pentru a reduce sarcina și consumul de energie al echipamentului, temperatura de turnare;
- face posibilă o schimbare rapidă a culorilor și a materialelor.
Avantajele de mai sus nu sunt legate de o modificare a indicelui de curgere și reducerea caracteristicilor fizice și mecanice ale polimerului.
Consum recomandat:
-In activitatea timpurie (randament în modul): 1,2-1,5% în greutate în timpul primelor 50-60 minute.
-După modul de stabilire: reducerea debitului la 0,6-0,8% în greutate.
6. preamestec antioxidant
preamestec Antioxidant este utilizat în cazurile în care este necesar să se obțină o stabilitate termică îmbunătățită în fabricarea articolelor din plastic (produse din HDPE și PP), din materii prime polimer reciclat.
Introducerea aditivi antioxidanți în polimer pentru a inhiba procesul de îmbătrânire termooxidative și îmbunătățește procesul de prelucrare (stabilizare a proprietăților reologice și omogenitatea topiturii, reducând tendința de reticulare și gelificare), pentru a menține proprietățile fizice și mecanice ale materialului (în t. H. Films), reduce tendința de a se decolora sau material îngălbenire. Utilizarea de antioxidanți, în special în combinație cu stabilizatori de lumină, poate crește, de asemenea, durata de viață a produselor din plastic cu mediul.
În funcție de gradul de degradare a plasticului reciclat și conținutul său într-un amestec cu un primar, intrare JCGP procentuală AO11-001 pentru diverse materiale plastice este 1-5%.
7. masterbatch Uscarea polimerilor
Uscarea preamestec utilizate la fabricarea materiilor prime secundare polimerice pentru a absorbi umiditatea din materialele plastice.
Masterbatch permite drenarea, chiar și în cazurile când umiditatea ajuns în granule (în acest caz, materiile prime nu pot fi supuse metodelor convenționale de uscare).
Astfel, DC 500 se aplică efectiv în următoarele cazuri:
- umiditate excesivă de material polimeric;
- hârtie reciclată;
- lipsa de echipament de uscare, sau, în cazul eficienței energetice.
Suntem gata să ofere un eșantion gratuit pentru testarea aditiv în producție. Va rugam sa ne contactati pentru mai multe sfaturi, dacă sunt utilizate în producție, în același timp, și alți aditivi, pentru a evita efectele secundare.
Masterbatch pentru reducerea inflamabilității polimerilor
8. Masterbatch ignifuganți pentru polimeri.
Substanțe ignifuge sunt utilizate pentru a crește rezistența de polimer la inflamatiei si poate incetini raspandirea incendiului. Aplicații plastice, care necesită introducerea unei construcții de ignifugare materiale, sectorul de transport, industria electrotehnică, electronică și așa mai departe ..
Comparativ cu alți aditivi, cum ar fi antioxidanți, stabilizatori la lumină, agenți antistatici, și așa mai departe. G. retardanți de flacără trebuie să fie administrate în cantități mari.
- FR 300 - PP utilizate în produse, de exemplu, un scaune stadion și mobilier de exterior. Aceasta se bazează pe o combinație de compus brom și oxid de antimoniu (Sb2O3). procentul recomandat de aditivi 8-12% - V2 pentru clasa (pentru UL94) și 25-30% - pentru V0 Class.
- FR 400 - conține o combinație sinergică a unui compus brom și antimoniu anhidridă organică pe bază de LDPE. Aditivul este destinat pentru produsele de extrudare PE (de exemplu, filme, tevi), la o temperatură maximă - nu mai mult de 210 ° C, Pentru a realiza UL94 V2 (cu o grosime de 15,5 mm), 10-12% recomandat pentru produsele LDPE și HDPE pentru - 12-15%.
Masterbatch pentru protecția împotriva razelor UV
9. Premaestecul UV de stabilizare lumină
Orice produse din materiale polimerice (LDPE-peliculă, materiale plastice) sunt expuse la căldură, lumină solară și oxigen, ceea ce duce la degradarea lor, t. E. La o pierdere a proprietăților mecanice și fizice adecvate.
Una dintre principalele cauze ale procesului de degradare, un ultraviolete (UV) de la soare. Acesta inițiază și accelerează reacția chimică ireversibilă, cum ar fi o reacție de scindare și reticulare a moleculelor de polimer. Acest lucru nu numai că schimbă aspectul, dar, de asemenea, are o influență negativă asupra proprietăților mecanice și fizice. Datorită absorbției oxigenului variază în structura moleculară a polimerului, ceea ce conduce la tipic cunoscută la acele manifestări ale îmbătrânirii: plesnire migrația de decolorare și proprietăți mecanice. Filmele se schimbă transparența lor, cutiile sunt acoperite de un dram de cretă, iar suprafața este crăpată, scaune de gradina rupte sub greutatea ei sa așezat pe un om. Procesul de degradare ar putea fi suspendat și perioada de utilizare a producției este mărită prin adăugarea de stabilizatori de lumină în polimer.
Până în prezent, stabilizatori de lumină, cum ar fi HALS (amine împiedicate) sunt cele mai eficiente. Preamestec „JCGP-001 PO-AL22 stabilizator de lumină“ se face pe baza înaltă moleculare fotostabilizatori HALS, pentru protecția împotriva polietilenă și polipropilenă filme radiații UV cu o grosime de 15 um. T. k. Acțiune POAL22 preamestec nu depinde de absorbția intrinsecă în regiunea UV, se stabilizează produsul, fără a afecta culoarea lor.
Concomitent cu acțiunea de mai sus a produsului este un poliolefine eficient de stabilizator termic care evită utilizarea unor componente suplimentare, dacă este necesar, materialul termofixare.
Stabilizatorii uzate macromoleculare asigură nici migrarea către suprafața produsului care nu cauzează sudabilitatea și apăsați deteriorarea de fixare și scurtarea acțiunii de stabilizare a luminii datorită componentei „eliminare“.
Introducerea preamestec într-o cantitate de 1,0-3,0% în greutate (în funcție de grosimea) în producerea filmelor de poliolefine asigura protecție împotriva expunerii la soare pentru 3 sezon. Prin cererea clientului, tonifiere preamestec posibil pentru a conferi filmului de culoare nuanța dorită pe o rola.
Masterbatch pentru curățarea echipamentelor industriale
10. Premaestecul de curățare pentru polimeri
Masterbatch pentru curățarea mașinilor de turnare și extrudere, procesare LDPE, HDPE, PP, CMEA, PVC flexibil la care apar în timpul prelucrării cocs pe pereții cilindrilor materiale și melcii (în special în prelucrarea materialelor secundare), precum și pentru a reduce timpul de tranziție de la o culoare la și reducerea volumului de material destinat pentru spălare.
Utilizarea unui concentrat pentru mașini de curățare nu produc un efect abraziv și coroziune elimină timpul de proces complicat și lung a curățării mecanice prin dezasamblarea echipamentelor și salvează din plastic pentru mașini de spălat și în timpul tranziției de la o culoare la alta.
Global Culorile exportă produsele sale la mai mult de 50 de țări. Producția și vânzarea ulterioară a masterbatch - activitatea noastră principală.